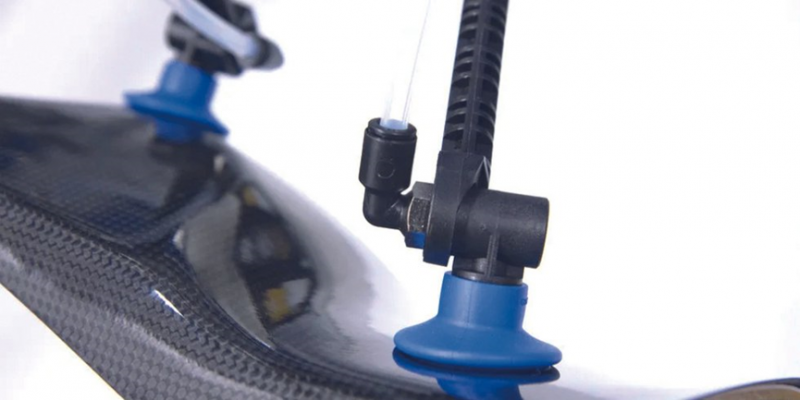
目前汽车和运输行业正在发生的颠覆性变化进一步增加了对轻量化部件的需求。此外,其他领域,如可再生能源,利用风能是我们未来能源安全的关键部分,是复合材料用于先进结构的另一个领域,将继续扩大复合材料的需求。
复合材料生产中使用的不同制造阶段和工艺带来了各自独特的挑战。在树脂转移成型(RTM)制造过程中,在CNC切割台上从干燥的纤维增强塑料上切割出所需的形状。然后,这些敏感的工件必须从刀具上取下,转移到工作台或暂时装入匣子中,然后再进行进一步加工和“堆叠”。
在此操作过程中,不同的层以定义的顺序放置在彼此之上,以此创建特定的层结构。这些操作需要小心处理单个工件,例如在航空航天领域,由于担心破坏纤维的完整性,不可能使用针夹。相反,使用专业的高流量真空夹持器。
这些夹持系统的吸力高达每分钟650升空气,仅产生100mb的真空,因此可以成功处理这些精致的部件而不会使产品变形。
然而,在汽车行业,允许使用针夹系统处理单个切割工件,并且为高性能汽车和赛车运动生产的许多单个复合材料部件都使用该技术处理。
针夹用最多24根针穿透工件。夹钳两侧的针朝相反的方向移动,产生必要的张力以牢固地握住纺织品。预浸料的处理则更具有挑战。在对预浸料进行加工之前,通常是通过热压来完成的,将胶粘剂材料在切割台上切割到合适的尺寸。
人工去除材料上的保护膜,然后将预切割的预浸料片以特定的顺序堆叠在一起,各层形成一个成套材料。然后将该套件放入模压机中,在模压机中对材料进行压制和固化。
处理预浸料面临的挑战是确保在处理过程中切割件不会粘在夹具上,并允许其精确释放。此外,需要注意确保夹持器不会受到太严重的污染。
在这种应用中,Schmalz吸盘提供均匀的真空分布,其平面设计也可以防止工件被吸入夹持器,保护半成品免受永久变形。
加工片状模塑料(SMC)需要一种完全不同的方法来克服材料处理的挑战。将这种材料的长纤维从卷中切割成所需的尺寸和形状,嵌入到硬塑性基质中并随机定向。
用于处理和放置这些工件的夹持器通常是特殊的针夹持器,具有高穿透力,可以拾取单个层的堆叠并将其放置在模压机中。
在复合材料部件生产的最后阶段,固化且通常仍热的部件在从模具中取出时必须牢牢夹持住,但又不能在工件表面留下痕迹。
由HT1制造的吸盘是这个过程的理想选择。这些吸盘既耐热又不含有机硅或可能损害任何后续油漆过程的物质。
如果纤维增强塑料组件在后期进行涂层,则可以避免潜在的表面缺陷。正如复合材料已经在许多不同的应用中找到了自己的方式,加工这些材料所需的夹具和处理技术也在不断发展,以提供满足工艺每个阶段独特标准的最佳解决方案。