1.1 玻纤作为主流增强材料,下游应用可涵盖交通领域
玻璃纤维是以叶蜡石、石英砂、石灰石等矿物为原料,配合纯碱、硼酸等化工原料经高温熔制、拉丝、络 纱、织布等工艺制造成的纤维增强材料;传统的金属材料及非金属材料相比,玻纤具有耐高温、抗腐蚀、强度高、比重轻、延伸小及电绝缘性能好等特性。玻璃纤维复合材料是以玻璃纤维及其制品(玻纤纱、布、毡等) 为增强材料,以合成树脂为基体材料,经复合工艺制作而成的功能型材料;玻纤复材不仅继承了玻纤自身的优 点,还具备节约能源、设计自由度大、以及适应性广等特点。目前玻纤类占到增强纤维复材整体约 90%,广泛 用于建筑、工业管罐、汽车与交通运输、电子电气、风电等领域。
玻纤多样性决定玻纤增强材料多元化发展。目前,国际上玻纤应用品种已达 5,000多种,60,000多个规格用途,品种与规格以每年平均增长1,000-1,500种的速度迅猛发展,品类繁多的玻璃纤维也决定了玻璃纤维增强材料的多元化。玻璃纤维增强材料按增强材料的类型可以分为玻纤纱增强复合材料以及玻纤毡增强复合材料;按照基体树脂的不同,可分为玻纤增强热固性复合材料以及玻纤增强热塑性复合材料,其中玻纤增强热固性复合材料主要以热固性树脂如不饱和聚酯树脂、环氧树脂、酚醛树脂、乙烯基酯树脂等为基体,热塑性以聚丙烯树脂(PP)、聚酰胺(PA)为主。多元化的玻纤增强材料性能各异,为适应不同领域的需求奠定了基础。
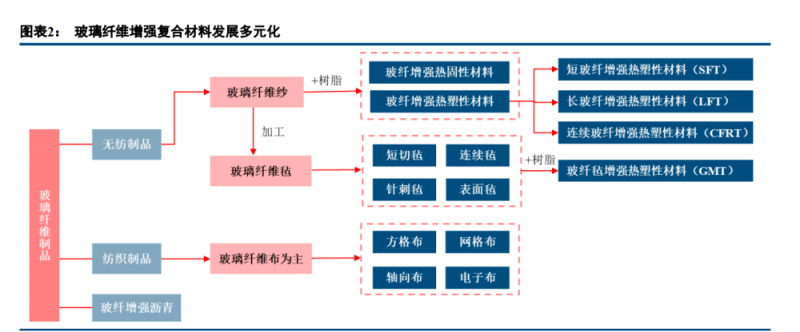
玻纤增强复合材料已形成完整产业链,应用领域广泛。目前,世界玻纤产业已形成从玻纤、玻纤制品到玻纤复合材料的完整产业链,其上游产业涉及采掘、化工、能源,下游产业涉及建筑建材、电子电器、轨道交通、 石油化工、汽车制造等传统工业领域及航天航空、风力发电、过滤除尘、环境工程、海洋工程等新兴领域。
中国交通领域玻纤需求占比16%,较全球尚有提升空间。据OC 统计,2020年全球玻璃纤维市场中建筑领域(包括住宅、商业建筑、水储运等)的玻纤需求约占35%;交通运输(轿车、卡车、公共汽车、火车、航海等)约占26%,电子电器等消费领域 15%,工业领域(管罐等)13%,风电及能源领域 11%。国内玻纤应用领域与全球类似,但交通运输领域占比16%,较全球比例尚有一定提升空间。
1.2 技术升级提高材料性能,长玻纤增强热塑性材料成为主流
从热固到热塑、从短玻纤到长玻纤,汽车领域玻纤应用场景持续开拓。20 世纪30年代玻璃纤维问世以来, 如何将玻纤更好的用于增强复合材料成为热点问题。1972年人们第一次将玻璃纤维毡用做增强材料,研发出 GMT 即玻纤毡增强热塑性材料,多应用于座椅骨架、车顶棚、发动机保护罩等。20世纪90年代,长玻纤热塑材料LFT的推出,将应用领域拓展至汽车前端支架、仪表盘、车底护板等。当前玻纤增强材料技术大幅提升,应用领域也明显拓宽。从技术发展的步伐判断,玻纤增强材料整体的发展趋势:由玻纤增强热固性复合材料向玻纤增强热塑性复合材料发展,由短玻纤增强复合材料向长玻纤增强复合材料发展。
2013-2021年,中国热塑产量复合增速9.05%,高于热固 7.45 个百分点。热塑性复合材料投资门槛较高, 但产品生产过程自动化程度高、较易实现清洁生产及产品回收再利用,并且凭借其优良的性能对热固实现一定 替代。2013-2021年,热塑产量从 137万吨提升至274万吨,CAGR达9.05%;同期热固产量从 273万吨提升至310万吨,CAGR仅1.60%,低于热塑7.45 pct。热塑产量长期增长趋势明显,主要受益于汽车、家电等领域复合材料的快速渗透;热固2020年增速激增,超过 30%,主要受益于陆上风电抢装需求。
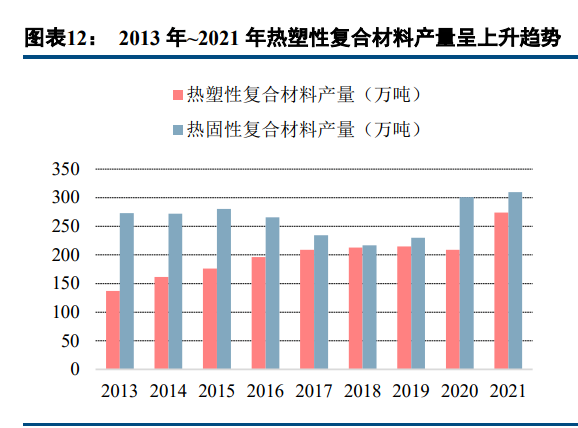
欧洲市场热塑产量增速也明显超过热固,目前仍以 SFT 为主。据 AVK 公司编制的《2021 复合材料市场报 告》,欧洲热固产量从2011年的94.4万吨小幅提升至2021年的94.8万吨,CAGR 仅0.04%。同期SFT、LFT、 GMT、CFRTP等热塑产品CAGR 达3.26%。2021 年,热塑类产品产量同比增长25.57%至 166 万吨,占比提升3.12pct 至56.04%。2021年欧洲碳纤维增强塑料产量5.2 万吨,过去10年CAGR为10.59%,处于较快发展的阶段。
玻纤增强热塑性材料更能适应当前环境,市场拓展不断有新突破。随着中国经济绿色化转型和绿色经济发展,热塑性复合材料已经在汽车及轨道交通轻量化、智能物流、绿色建筑、体育休闲及现代农牧业养殖等领域展现出了巨大市场潜力。例如,福建海源成功研发出建筑模板制品,进入建筑模板市场;杭州华聚的连续挤拉成型的热塑性蜂窝夹芯板材已经成功应用于国内外各类箱式货车、物流车和房车领域;河北立格与中铁联运物流股份有限公司签订战略合作协议,成功进军物流运输行业。
从短玻纤到长玻纤
玻纤长短对复合材料性能影响较大,长玻纤性能优于短玻纤。玻璃纤维增强热塑性复合材料根据玻璃纤维增强方式的不同,分为短玻纤(SFT)、长玻纤(LFT)和玻璃纤维毡(GMT)增强三种类型。短玻纤长度一般在 6mm 以下,长玻纤一般在 10-15mm。据研究显示,玻纤的长度越长,玻纤复合材料制品的性能就越好。SFT是玻纤增强热塑性复合材料的主要品种,具有成型工艺简单、周期短等优势,但是其性能在很多地方仍不能满足汽车零部件的需求。相比之下,LFT增强热塑性复合材料的性能比SFT高很多,在相同玻纤质量分数的情况下,长玻纤增强材料的拉伸强度、弯曲强度、冲击强度均高于短玻纤增强材料。因此,LFT产品在汽车领域的应用将会比SFT更加广泛。
长玻纤相较于短玻纤、玻纤毡具备超额增速。据 RePort link 的市场研究预计,2017 年至2021年之间全球 长玻纤增强材料的复合增长率为 8.5%,短增强玻纤热塑性塑料的复合增长率仅为 4.5%;同期欧洲市场LFT实际产量复合增速3.68%,SFT产量复合增速仅0.61%。从玻纤加工形态来看,由一步法直接生产的 LFT 生产成本理论上要比GMT材料成本低 20%~50%,抗冲击性能和生产效率等综合性能反而有所提升,因此近年来欧洲市场 LFT 的市场份额更具优势且逐年提升。全球汽车行业的 LFT 消耗量约占 LFT 总消耗量的 80%,而当前汽 车等交通工具轻量化已经成为交通行业的增长热点,需求空间将进一步扩大。
02 汽车轻量化需求拉动玻纤市场
政策推进“以塑代钢”,汽车及交通领域受影响显着。我国自“十一五”以来,就明确将“以塑代钢”作为节约能源和资源的重要举措,并将“复合材料、高分子材料、工程塑料及其低成本化、新型塑料合金生产”作为调整产业结构、发展高新技术的重点。我国改性塑料产量从2010年的705万吨增长至2021年的2650万吨, CAGR达12.8%,改性化率从16.2%逐步提升至24.0%。据前瞻产业研究院统计,2020年汽车领域改性塑料需 求大约占比19%,仅次于家电领域。考虑到汽车改性塑料对于强度有更高要求,因此对玻纤增强材料的需求拉动更为明显。
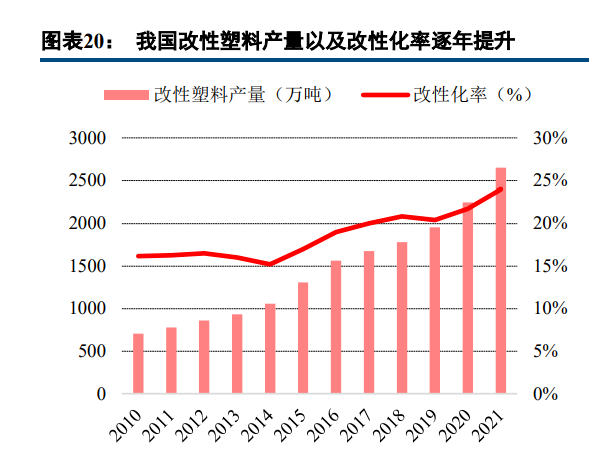
微观数据层面,汽车改性塑料销量占比呈提升趋势。以国内最大的改性塑料龙头企业金发科技为例,2021年车用材料销量同比增长26.82%至61.75万吨,在改性塑料销量中占比提升3.9pct 至 35.4%,这主要受益于国内新能源汽车销量的翻倍式增长。
横向比较:我国塑钢比处于较低阶段,人均玻纤消费量尚有较大提升空间。相较于国外市场改性塑料行业 的成熟发展,我国塑钢比水平较低。2012年,美国塑料和钢铁应用(体积)比例为70:30,德国为63:37,世界平均水平也达到50:50,同期国内塑钢比仅30:70。从细分的玻纤增强塑料市场来看,虽然我国是世界玻纤产量 第一大国,但2018年玻纤人均消费量仅为 2.4 千克/人,不到美国人均消费量的45%,未来国内玻纤增强材料渗 透率存在长期提升空间。
纵向比较:当前我国塑钢比还有持续提升的动力。通过跟踪钢材、塑料产量,并假设钢铁密度7.85g/cm3、 塑料密度 0.9g/cm3,折算出2021年塑钢比约为42:58。塑钢比较10年前提升明显,目前仍低于世界平均水平, 未来仍有提升动力。
2021年国内玻纤增强复合材料制品产量维持较高增长,结构上实现从风电到汽车轻量化的交棒。2021年全国玻璃纤维增强复合材料制品总产量为584万吨,同比增长14.51%,延续了2020年的亮眼增速。2020年主要受益于风电市场的强劲增长,而 2021 年则受益于新能源汽车产量的增长,以及电子电气领域玻纤增强材料的支撑。随着下游需求完成“交棒”,2022年及以后汽车领域有望成为拉动玻纤需求最快的马车。
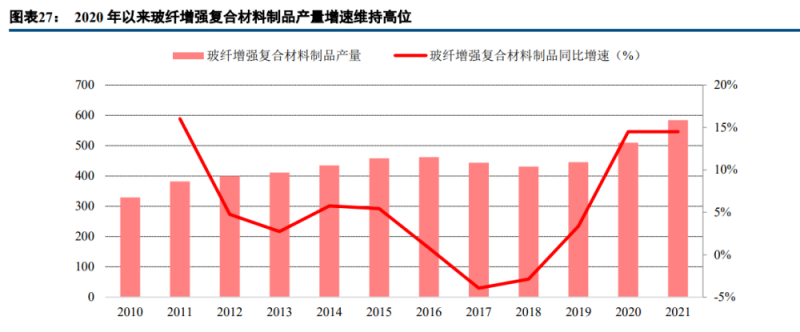
2.1 汽车:轻量化趋势持续创造需求,新能源车大爆发贡献新动能
传统汽车:轻量化持续渗透
汽车减重为长期趋势,轻量化势在必行。汽车工业发展的过程中,轻量化一直为多方关注的重要领域,就 其原因在于以下几点:汽车轻量化是节油和降低排放的重要方法和途径。实验表明:油耗与车体质量成线性 关系,每百公里油耗 y(单位 L)和汽车自身质量 x(单位 kg)的关系为:y=0.003x+3.3434,即对一般汽车而 言,质量减少 10%,可节油 6%~8%,可以相应减少二氧化碳排放;从驾驶方面来讲,汽车自重减轻后,加速 性提高,稳定性、噪音、振动方面也均有改善;从安全性考虑,汽车质量减轻后,碰撞时惯性小,制动距离减小,车辆对人的冲击小得多,所以更加安全。因此,在双碳政策背景下,叠加环保、交通安全要求趋严,汽 车轻量化是长期趋势。
中国制造2025规划明确轻量化路线,材料为轻量化筑牢根基。汽车轻量化的途径一般主要表现在三个方面:结构轻量化:最容易实施也是成本最低的一种设计手段;轻量化材料:最基础也是最有效的手段;先进 工艺:先进轻量化材料应用的保障。中国制造2025规划了重点领域技术路线图,从上述3种途径对汽车轻量化 做了重要规划和思路建设,其中轻量化材料方面多次强调使用纤维复合材料作为发展方向。随着该技术路线图 的不断推进,纤维增强材料已经承担起轻量化的重任,成为轻量化材料中的“主力军”。
玻纤增强材料质轻价廉,为当前汽车轻量化材料首选。玻纤增强的复合材料已成为汽车工业的主要原材料 之一,其优势在于拥有优良的材料特性、良好的经济性、大量供应的可能性、较好的可回收性。玻璃纤维增强型热塑性复合材料具有低密度、设计自由度高、耐腐蚀、抗冲击以及吸收震动等优点,可以替代钢、铝用于结 构件,轻量化效果显着。现在最常用的长玻纤增强型材料已经可以完全取代金属材料用于前端模块上,达到轻量化目的,减重达30~50%。目前,大众和马自达等合资企业已有较普遍的应用,改用长玻纤增强型材料后,无论是重量还是成本都有明显下降,可谓“质轻价廉”。
玻纤增强材料应用场景广泛,由内而外对全车实现覆盖。随着玻纤增强材料工艺技术的不断发展,玻纤增强材料在汽车轻量化中的应用场景也越来越广泛。回顾玻纤增强材料的发展过程我们可以看出,前期玻纤热固性增强材料,例如片状模塑料(SMC),树脂转移模塑(RTM)技术,一般用于车门、引擎盖、翼子板等 A 级 表面制件,而现阶段广泛应用的玻纤热塑性增强材料进一步扩大了应用范围,包括仪表盘支架、前端支架、保 险杠、车底护板以及发动机周边部件,实现了对全车大部分零件和次结构件的覆盖。
玻纤增强材料能较完美的配饰各个部件,轻量化效果显着。玻纤增强材料不仅在汽车轻量化中的应用场景 实现了多元化,更是在多种类的同时保证了每一个组件都能发挥玻纤增强材料的优势。在福特和捷豹的车门板 中应用了 Cslstran+PP-GF20-05 热塑性长纤维增强材料,在高度集成的基础上实现了高强度、高颜值以及高冲击 吸能效果;在福特的前端板块中使用了长玻纤(LFT)增强聚丙烯(PP),实现了单车减重 1.4kg,降低成本 3 美元,并满足了传统车辆上部件变形。
国内车用玻纤增强材料渗透空间巨大。20 世纪90年代,发达国家汽车平均用塑料量100~130kg/辆,占整车重量的10%左右;日本每辆汽车平均使用塑料量 100kg,占车重的12%。欧洲汽车塑料占车重量的 10%左右。1996年,北美轿车的塑料平均用量为 116.5kg/辆,2003 年增加到 142kg。截至2013 年,以德国为首的欧洲国家 单车用塑料复合材料(以玻纤增强塑料为主)已经达 300~365kg,占车重22.5%;美国的单车用量也达到 200~249kg, 约占车重16.5%;而我国单车用量仅为 90~110kg,仅占车重 8%,远远低于发达国家的平均水平。在汽车轻量化的大趋势下,国内玻纤增强材料市场前景广阔。
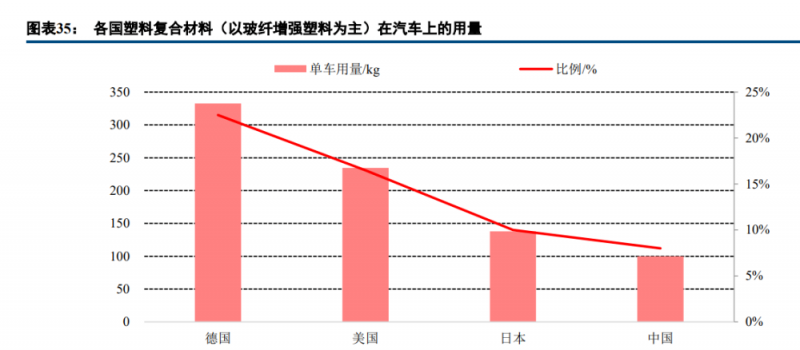
新能源车:需求大爆发贡献新动能
燃油车退出是大势所趋,新能源汽车轻量化成为行业痛点。随着石油资源的逐渐变少以及人类生态环境保 护的需要,近年来许多汽车工业发达国家已开始布局汽车产业升级战略,荷兰、挪威、德国、印度、法国、英 国等先后通过不同的组织和方式提出了停售燃油汽车时间表,沃尔沃、宝马、大众、丰田等名车企也先后透露出停止生产燃油车的动向和计划时间表,燃油车退出市场,新能源汽车“新王上位”已成定局。然而据国家新 能源汽车技术创新中心总经理原诚寅表示,新能源汽车由于电动化、智能化等配置需求,增加了三电系统及大 量智能化设备,相比较传统汽车增重较多。研究表明,新能源汽车质量降低 10%,对应续航里程可增加5%~10%, 节约 15%~20%的电池成本以及 20%的日常损耗成本。因此,新能源汽车整车减重的需求比传统汽车更加迫切。
当前主流新能源车普遍偏重,日系燃油车整体最轻。以各大厂商部分中型车为例,特斯拉Model Y 的质量 达 2010kg,基本处在其所有车型的中位数水平,最轻的 Model 3 也重达 1761kg。国内新能源车以比亚迪为例, 各车型重量中位数大致在 1940kg。德系奔驰、奥迪中型燃油车质量约 1600-1700kg;而宝马则更接近日系车, 质量在 1400kg 的量级。
除了传统部件轻量化,新增部件也将带来玻纤增强材料需求。除了对传统部件轻量化的需求迫切,新能源 汽车新增的零部件以及配套装置也面临减重需求。玻纤增强尼龙因为质量轻、强度高、耐磨耐腐蚀、绝缘性能 好而在新能源车中广泛使用,具代表性的应用有交流电机外壳、电池箱、充电系统(例如充电枪模块)、电子控 制器零部件、旋转变压器等。因此,玻纤增强材料不仅在传统车型、传统部件中快速渗透,也将在新能源车、 新模块中也将占据份额。
2021 年我国汽车市场实现恢复性正增长,新能源车销量占比 13.4%。我国汽车销量经历了2018-2020年连续3年下滑,在 2021 年实现恢复性正增长。2021年汽车总销量达2627.5 万辆,同比增长3.81%;其中新能源汽车销量同比增长157.48%至352.05万辆,在汽车总销量中占比提升8pct至13.4%。
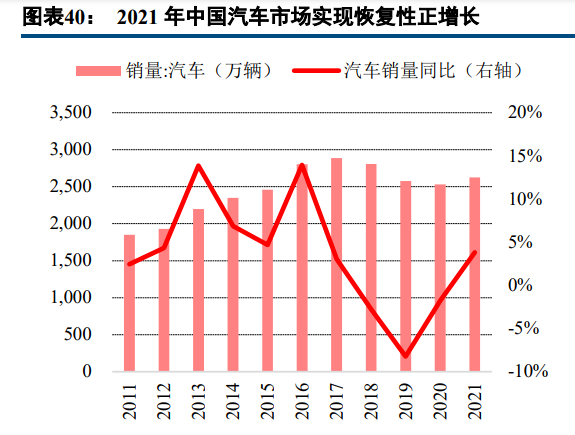
2022年1-6月新能源汽车销量继续实现翻倍增长,同比增长 115.61%至259.95万辆。1-6月,汽车总销量 同比下滑6.47%至 1205.7万辆,剔除新能源车后降幅约19.07%,主要系疫情扰动下增速受到压制。而随着新能源汽车销量的爆发式增长,将带动全年汽车总销量增速回升。
需求测算:2025 年国内汽车用玻纤增量需求超 80 万吨,CAGR 达 16%
参考重点领域技术路线图(2015 版),要求2015-2025年汽车累计减重30%,平均每年减重 3%,参考大约2.0/1.6吨的初始重量,大约每年减重60/50kg。到2025 年,预计新能源汽车/燃油车改性塑料使用比例分别提升至24%/20%。参考中信建投电新团队对新能源汽车销量的判断,以及我们对于燃油车逐年减量 的保守估计,预计2025年汽车改性塑料需求量提升391万吨,几乎全部由新能源汽车贡献;单车平均用量提升约136kg,其中新能源车平均提升181kg,燃油车平均提升71 kg。预计 2025 年国内汽车用玻纤增量需求超80万吨,2021-2025年CAGR 达 16%。热塑短切属于玻纤粗纱中的高端制品,若按照 8000 元/吨的均价,2025年汽车用玻纤市场约145亿元;近 3 年金发科技改性塑料均价约1.37万元/吨,由此估算2025年汽车改性塑料市场规模约1180亿元。
2.2 其他领域:紧扣交通与轻量化主线,玻纤材料长期渗透
航空航天:特种高性能玻纤不可或缺,金属材料之友
航空航天复合材料用量比重逐年增大,特种高性能玻纤优点显着。当前复合材料与铝合金、钢、钛合金3大金属材料成为航空工业不可或缺的材料。无论是民用客机还是军用飞机,都需要使用高性能玻璃纤维增强的复合材料,这种材料具有优良的力学性能、优异的抗疲劳和耐腐蚀性,优良的透波介电性能;其结构利于整体设计和制造,可实现20%~30%的结构减重,在提高飞机结构效率和可靠性的同时,降低制造成本。欧洲空客公 司最具代表性的A380-800飞机重约583吨,机身大部分是铝,但也采用了20%以上的先进复合材料。除了碳/ 环氧、玻纤/环氧复合材料,还有 GLARE(玻璃纤维增强铝)复合材料,它是由多层玻璃纤维和铝合金粘合而 成,比传统用的铝合金轻,但有更佳的抗侵蚀和抗撞击能力。目前,先进的军用飞机、民用客机的复合材料用量迅速增加,预计今后复合材料的用量将超过飞机总重量的50%。
特种高性能玻纤在航空领域多元化发挥优势,提高飞机性能。航空用特种高性能玻璃纤维的种类主要包括2大类,一类用于结构增强的主、次承力结构件中,如 GLARE 层板、直升机旋翼等;一类是应用在有特殊电性 能要求的功能结构件以及内饰中,如机头罩、天线罩和雷达罩,以及舱内地板等。在主承力结构件中,玻纤增强材料主要用于直升机的旋翼桨叶,提高了桨叶的抗拉刚度、挥舞及摆振刚度以及抗冲击性能;在次承力结构 件中,玻纤增强材料主要用于飞机的机翼固定前缘、方向舵、尾翼和尾锥等部件上;在内饰方面,主要将高均匀性缎纹玻璃纤维织物与阻燃环氧、酚醛制成的复合材料用于飞机的地板和天花板等部分,其具有高比强度和比刚度的特点,阻燃和低烟雾的优势明显。

玻纤复合材料占航空复合材料市场比例不断提升,其需求量在 2023年有望将达到5.02万吨。据前瞻产业研究院数据,玻纤复合材料在我国航空航天领域应用较广,占航空复合材料市场的比重有望逐年提升;2017年该比例约为14.2%,预计2023年将提升至18.5%。随着我国航空领域的发展对耐用、重量轻、无腐蚀产品的需 求日益增加,2023年玻纤复合材料在航空领域的需求量有望达到5.02万吨。
船舶:中小渔船乘风破浪,玻纤材料广阔蓝海
玻纤增强材料为FRP(玻璃钢)渔船的主流材料,玻璃钢渔船或代表渔船行业的发展趋势。FRP渔船的主流材料为玻璃纤维增强材料。相比于木材和金属材料,玻璃钢在满足力学性能要求的同时,具有自重小,耐盐 水腐蚀,隔热性能好,可设计性强等特点。
1)航行性能方面,玻璃钢船在波浪中行驶稳定性更强,抗风能力更 好;相同条件下,玻璃钢渔船的航速比钢制渔船提高了 0.5-1.0 节。
2)在经济性方面,玻璃钢船燃油消耗比同尺寸的钢制、木质渔船更小。玻璃钢本身耐腐蚀、抗老化的优点也增加了玻璃钢渔船的寿命,玻璃钢渔船的理 论寿命一般在50年左右,为钢制渔船的4-5倍,维护频率和费用也远低于钢制渔船。
当前我国木制渔船存量巨大,渔船更替将带来玻纤增强材料需求。目前,FRP渔船是国内外渔船的主流方 向。在欧美发达沿海国家,木质和金属制中小型渔船已经基本淘汰,FRP渔船的占比高达80%~90%。其中,美国的近海渔船已经全部更换为 FRP 渔船,每年用于制造渔船的FRP总量超过20万吨。日本的 FRP 渔船起步较晚,但通过木质渔船FRP改造,2008 年其 FRP 渔船的保有量为35万艘,占日本渔船总量的 90%。2021 年末我国渔船总数52.08万艘,较2015年削减一半,仍是全球渔船最多的国家,但玻璃钢渔船占有率 极低。截至 2013 年,全国 20 米以上纯复合材料作业渔船不足 500 艘,所有尺寸的玻璃钢渔船仅占渔船总量的 1%左右。同等船长的玻璃钢渔船造价比钢制渔船高 30%~50%,但考虑到使用寿命,玻璃钢渔船更具性价比。借鉴国外“大型渔船钢质化,中小型渔船玻璃钢化”的经验,倘若未来10年我国FRP渔船保有量逐步达到 30 万艘,每艘使用10吨FRP,则面临300万吨总替代空间,年均玻纤复材需求30万吨。随着“以塑代钢”推进, 在如此大的存量、如此低的占有率下,船舶用玻纤增强材料将面临一片广阔“蓝海”。
家电:轻量化、定制化持续推进,拉动玻纤增强复合材料增长
玻纤增强复合材料性能优良,拥有丰富的家电产品应用场景。家电行业是改性塑料行业最重要的下游产业 之一,改性塑料拥有质轻而高刚度、安全、无毒、节能环保、抗菌抗霉变、低成本等特性,能满足人们对家电 轻量化、健康化的需求。随着改性设备、改性技术不断发展成熟,过去占塑料行业 90%以上的通用塑料通过改 性提高了强度、耐热性等指标,具备了工程塑料的性能,并已经抢占了部分传统工程塑料的应用市场。玻纤增强改性作为塑料改性的重要途径之一,在家电产品中应用广泛。
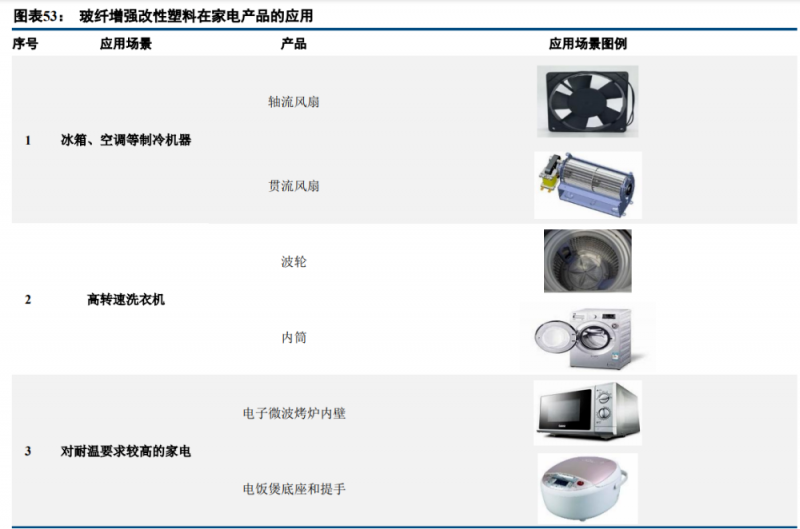
家电为我国改性塑料第一大消费领域,2020 年应用占比 34%。改性塑料下游主要为家电、汽车、办公设备、 电子电气和电动工具,其中家电是第一大消费领域,2020 年占比约 34%。2021 年,我国空调产量为 21835.7 万台,同比增长 3.66%,彩电产量为 18496.5 万台,同比下降 5.76%,家用电冰箱和洗衣机产量分别为8992.10万台和8618.50万台,同比分别下降0.25%和增长7.17%。整体来看,2021年我国四大家用电器产量较2020年实现小幅增长。
以空调、冰箱为例,2021年城镇和农村冰箱渗透率均超过 100%,农村空调保有量快速提升至 89%,但仍有较大的增量空间。随着我国经济的恢复和居民收入不断提高,家电市场特别是县城、农村等下沉市场将带来 较大的增量需求,进而拉动改性塑料及玻纤增强复合材料销量的增长。未来家电行业加快向智能化方向升级, 消费者不仅对家用电器的阻燃性、强度、耐候、环保等基础性能有较高要求,而且对易成型、色彩丰富、吸震 消音等定制化和轻量化提出了挑战,未来高端家电对改性塑料及玻纤增强材料的用量及性能需求将不断提升。
供需判断:2022 年产能投放加快,格局仍然集中
中国是全球最大的玻纤生产国,产量占比超过 66%。2012 年至 2020 年,全球玻纤总产量由 530 万吨增加 至 820 万吨,年均复合增长率 5.61%;同期国内玻纤总产量由 288 万吨增加至 541 万吨,年均复合增长率 8.20%。2021 年国内玻纤产量达 624 万吨,同比增长 15.2%。玻纤是建材行业中少有的出口产品,2021 年度玻纤及其制 品出口量为168.3万吨,同比增长 26.54%,出口占国内产量比例提升2.4pct 至26.97%。
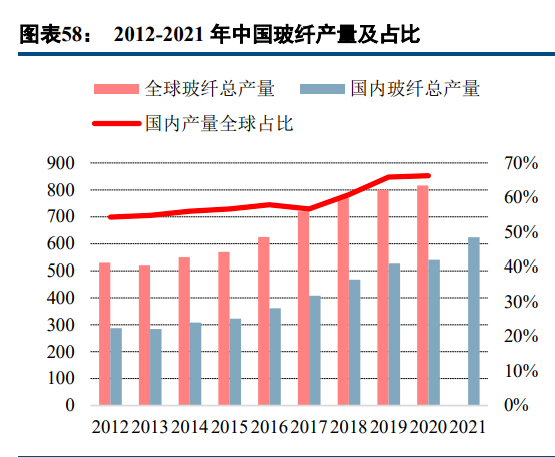
玻纤行业资金与技术壁垒驱使玻纤产能集中,整体市场格局稳定。1)资金投入方面,以粗纱为例,每万吨玻璃纤维所需固定资产投入约为 1 亿元。国家发改委、工信部不断提高玻纤行业准入标准,新建无碱玻璃纤维 池窑法粗纱拉丝生产线单窑产能规模从 2012 年的 5 万吨/年提高至 2019 年的 8 万吨/年,则投资一条年产 8 万吨 的粗纱生产线需要约 8 亿元的固定资产投入。高模、电子、低介电等类型玻纤等投资则更为巨大,这构成了玻 纤行业新进企业的资金壁垒。2)技术方面,玻纤企业需要掌握池窑设计、节能燃烧、玻璃配方、漏板设计与制 造、表面处理、纤维成型等多项技术。其中浸润剂原材料及配方技术是体现各类玻纤制品内在质量的关键技术, 玻纤及其制品的竞争很大程度上依赖于浸润剂原材料及配方技术。根据卓创资讯和星智研究数据,世界玻纤产能集中度 CR3 和 CR5 分别为 47%和 64%;截至 2022H1 国内玻纤在产产能 663.5 万吨,集中度 CR3 和 CR5 分别高达 60%和 71%。
从发展路径看,龙头企业与二三线企业实现了差异化发展。粗纱领域,中国巨石享有行业内最为显着的规 模优势和成本优势。风电纱领域,中国巨石、泰山玻纤、国际复材、山东玻纤优势较突出,分别研发E9、THM-1、TMII和ECER的超高模量玻璃纤维纱,逐步应用于大型及超大型叶片中。电子纱领域,国内以宏和科技为首的 企业逐步攻克高端电子纱、电子布制备技术,实现国产替代。玻纤复合材料方面,长海股份已经成为国内短切 毡、湿法毡等细分领域龙头,形成玻纤、树脂和玻璃钢完整产业链。2021 年龙头玻纤企业营收显着增长,毛利 率同步回升。从时间序列来看,毛利率变化均受行业供需影响;但横向比较,龙头在盈利能力方面具有稳固的行业地位。
预计2022年新增粗纱产能76万吨,新增电子纱22万吨。2021年国内主要新增产能来源于邢台金牛新点火10万吨粗纱,中国巨石15万吨短切原丝及6万吨电子纱,长海股份、泰山玻纤、山东玻纤各10万吨粗纱, 黄石宏和 6 万吨电子纱,同时存在少量计划冷修的产线。合计增量 55万吨粗纱及 12 万吨电子纱,大部分在 9 月以后释放。据卓创资讯统计,2022 年新增无碱粗纱产能为巨石成都 3 线 15 万吨,国际复材长寿 F12 线 15 万 吨,重庆三磊、邢台金牛各 10 万吨,以及九江华源、四川裕达分别 6 万吨、3 万吨产能。考虑潜在的冷修技改增产,预计合计新增 76 万吨,产能增长15%左右,节奏较 2021 年有所加速。2022 年中国巨石、泰山玻纤、建 滔化工合计新增电子纱 22 万吨,对电子纱价格的冲击已经在上半年充分体现。
远期行业落后产能将逐渐出清,行业扩产将转向有效供给。根据国家发改委《产业结构调整指导目录(2019 年本)》,文件将“中碱玻璃纤维池窑法拉丝生产线;单窑规模小于 8 万吨/年(不含)的无碱玻璃纤维粗纱池窑 拉丝生产线;中碱、无碱、耐碱玻璃球窑生产线;中碱、无碱玻璃纤维代铂坩埚拉丝生产线”列入限制类。政策端对玻纤小产能、落后高耗能产能进行了强管控,占比近 10%的坩埚产能将逐步被淘汰,小企业小产线将逐 步出清。根据玻璃纤维“十四五”发展规划,文件指出“十四五”期间,要严格控制玻璃纤维纱总产能过快增 长,将行业年度玻璃纤维纱实际总产量同比增速控制在不高于当年 GDP 增速 3 个百分点。我们预计能耗双控和 双碳目标大背景下,远期供给端产能将逐渐与需求端匹配,市场供需失衡和恶性竞争情况将大幅改善,行业重 点将转向有效供给扩产,从而对玻纤长期价格形成支撑。
价格判断:1)粗纱:2022年上半年 2400tex缠绕直接纱均价约 6190 元/吨;7 月底多数厂报价5400-5900元/吨,均价5657元/吨。8 月仍未走出需求淡季,且前期新点火产能逐步释放、库存积累,粗纱价格将逐渐触底,考虑到龙头企业挺价意愿较强,均价跌破 5000 元/吨的概率不大。预计 9 月以来产量环比逐渐趋稳,下游 需求提升,粗纱价格弱势复苏。我们判断 2022 年全年均价 5800-5900 元/吨,较 2021 年全年均价(约 6080 元/ 吨)降幅仅 3.0%-4.6%。2023 年预计汽车、风电需求提升,能耗指标持续收紧,但成本支撑有望弱化,综合来看,均价展望平稳。2)电子纱:2022年价格底部(约 8750 元/吨)已经在4月体现,下半年价格向上弹性充足, 但难以超越 2021 年全年 15500 元/吨的高基数。截至 7 月底暂无较大新增产能规划,因此即便不考虑下游需求 超预期,本轮价格复苏趋势也有望持续到 2023 年三季度。
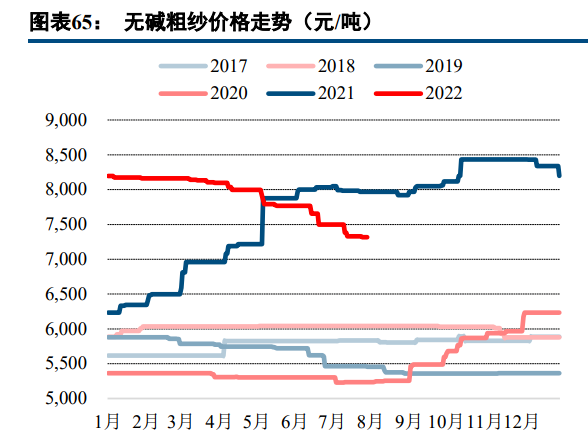
03 重点公司分析
3.1 中国巨石:全球领先的玻纤龙头,短切热塑扩产锁定高端市场
玻纤行业翘楚,产能领跑全球,十年净利润复合增速 35.34%
中国巨石为中国建材控股子公司,玻纤业务始于桐乡问鼎全球。中国巨石的前身为“中国化学建材股份有 限公司”,于 1993 年成立、1999 年上市交易,证券简称“中国化建”,并在 2004 年、2015 年依次变更为“中国 玻纤”、“中国巨石”。经过 22 年的股权变更,中国巨石目前是中国建材控股的主营玻璃纤维业务的核心子公司, 持股比例为 26.97%,第二股东振石集团持股比例为 15.59%。巨石的玻纤业务自桐乡开始逐渐布局全国,2000 年收购九江玻纤总厂并崛起为国内玻纤龙头企业;后在桐乡建成数条 10 万吨级别超大玻纤生产线,迅速扩大产 能,年产 60 万吨玻纤的桐乡生产基地的落成,标志着公司生产规模达到全球第一;2012 年后,公司实施全球 布局战略,在五大洲均设立子公司并建立销售网络。
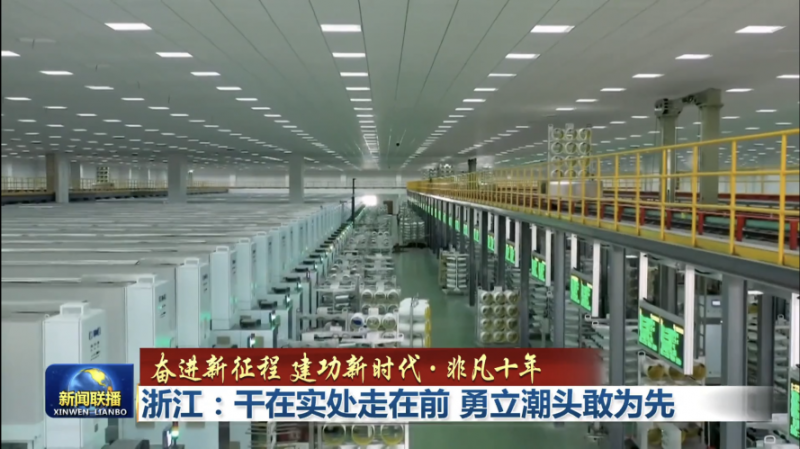
巨石 2021 年营收和归母净利润同比大幅增长,行业处于持续高景气。公司 2021 年度实现营业收入 197.07 亿元,同比增长 68.92%;归母净利润 60.28 亿元,同比增长 149.51%;扣非归母净利润 51.50 亿,同比增长 165. 22%。2021 年,公司国内营收占比 67.15%,与上年基本持平;玻纤及制品占总营收比例为 94.97%。2021 年公 司实现粗纱及制品销量 235.28 万吨;电子布销量 4.40 亿米,处于历史最高位。过去 10 年公司业绩实现稳定增 长,营收复合增速为 14.61%,归母净利润复合增速为 35.34%。
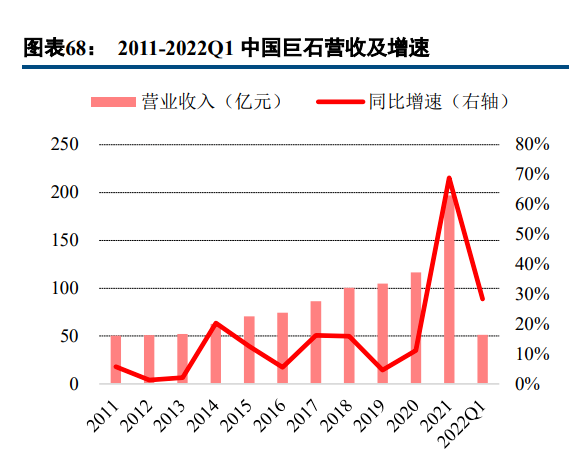
公司成本管控优势明显,2021 年净利率创 10 年新高。经历了 2018-2020 年的玻纤下行周期后,公司玻纤制 品 2021 年全年毛利率大幅回升。2021 年公司毛利率为 45.31%,同比提升 11.53 个百分点;净利率 31.15%,同 比提升 10.49 个百分点。2021 年公司期间费用率同比下降 0.25 个百分点至 12.76%,延续下降趋势;其中财务费 用率同比下降 1.68 个百分点至 2.48%的新低水平。利率水平的下行,以及公司融资手段从公司债、定向工具、 中期票据逐渐转换成短期融资券,是长期中公司财务费用率持续下降的重要因素。2022Q1 公司销售毛利率提升 1.05pct 至 44.57%,净利率提升 10.07pct 至 36.81%,再创历史新高。
2021年公司产能超过230万吨,智能化产线人均效率领先全球。1)总产能:公司目前已建成包括浙江桐乡、江西九江、四川成都、埃及苏伊士、美国南卡的五大生产基地,2021年合计产能超过230万吨。考虑到冷 修技改、在建拟建,未来供应能力还将大幅增长,预计2023年公司产能将超过300万吨。2)智能制造:公司 投资超过 100亿元的桐乡新材料智能制造基地,最初计划建设 45 万吨粗纱生产线和18万吨细纱生产线;截至2021年,3 条智能化粗纱、2 条电子纱已经实现点火,还顺利扩建智能化4线,年产 15 万吨短切纱;2022 年第 3 条智能制造电子纱产线从计划6万吨变更至10万吨,并于 6 月顺利点火。智能制造生产基地所有产线均可实现 480 吨/人的效率,领先全球,效益的提升将使得平均成本显着下降。
把握海外需求+短切热塑两条主线,产能扩张顺应轻量化行情
海外短切热塑产品需求增长,外国本土企业受成本提升影响产能出现调整,利好公司海外市场份额的提升。2021 年我国玻纤及制品出口总量达 168.3 万吨,同比增长 26.5%;2022 年以来海外需求持续景气,上半年出口量同比增长 42.1%至 107.9 万吨。2021 年公司海外营收占比约 33%,2022 年随着海外需求的不断释放,占比有望显着提升。近年来,欧美汽车工业市场复苏,对热塑产品的需求增速较快,而欧美本地企业供应能力并未显 着提升;2022 年欧洲天然气成本激增进一步加剧了供需矛盾,因此对中国玻纤企业的依赖度明显提升。中国巨 石通过埃及、美国产能实现“以外供外”,并从国内海运出口实现“以内供外”,海外市场份额有望持续提升。
公司热塑性玻璃纤维品类齐全,广泛用于汽车、家电、基建等领域。2021 年公司热塑短切产品比例快速增 长,全年高端产品比例已超过 80%。未来随着国内双碳目标的不断推进和国外需求持续高景气,汽车轻量化主 要利好的热塑产品需求有望保持高增长,公司业绩有望持续提升。
短切原丝产能持续扩张,积极布局热塑性复合材料产品高端市场,力争实现公司十四五发展目标。2021 年 3 月,公司拟投资 17.96 亿元,建设年产 15 万吨玻璃纤维短切原丝生产线建设项目;2022 年 2 月,巨石成都投资 17.98 亿元,建设年产 15 万吨玻璃纤维短切原丝生产线建设项目。当前上述项目均已投产,专用于提升热塑 短切产能,优化产品结构,迎接汽车轻量化行情。未来公司将持续着力扩大生产规模和产品结构升级,“十四五” 末粗纱中热塑的比例有望提升至 45%-50%;整体实现热固粗纱、热塑短切、电子纱及电子布“三足鼎立”的产 品结构。
3.2 长海股份:国内车顶短切毡市占率超 50%,热塑领域核心受益标的
国内短切毡、湿法毡等细分领域龙头
江苏长海复合材料股份有限公司(简称“长海股份”)成立于 2000 年 5 月,2011 年在创业板上市。公司主营业务为玻纤制品及玻纤复合材料的研发、生产和销售,主要产品包括玻纤纱及玻纤制品短切毡、湿法薄毡、 蓄电池复合隔板、玻纤涂层毡等,其中短切毡应用于汽车顶棚、卫浴洁具、大型储罐等,湿法薄毡应用于内外 墙装饰、屋面防水、电子基材等。经过多年创新发展,公司深耕无纺玻纤制品赛道,已经成为国内短切毡、湿 法毡等细分领域龙头。除了玻纤业务以外,公司通过子公司天马集团进行树脂产品的研发和生产,基于不饱和聚酯树脂等和玻纤打造复合材料一体化产业链。
长海股份实际控制人为杨国文、杨鹏威父子,持股 52.28%,持股比例较高,股权结构稳定。截至2022年一季度末,杨国文、杨鹏威父子合计持有21367.44万股,占公司总股本的 52.28%,二人为一致行动人且为公司 的实际控制人。自公司成立以来,杨国文、杨鹏威父子的合计持股比例一直维持在 47%以上,公司股权结构稳定。截至 2022Q1,前 10 大股东合计持股 64.00%,其中机构投资者合计持股 9.49%。
公司 2021 年以来业绩屡超市场预期,2022Q1 归母净利润大幅增长115%。公司长期业绩稳步提升,2021 年以来持续爆发式增长,2008-2021 年,公司营收CAGR达20%,归母净利润 CAGR达28.22%。截至2021 年, 公司实现营业收入 25.06 亿元,同比增长 22.71%;实现归母净利润 5.72 亿元,同比增长 111.46%。2022Q1,新增产能快速释放使得公司业绩再超预期;其中营收同比增长 36.05%至 7.54 亿元,归母净利润同比增长 115%至 2.28 亿元。公司规模仍处于快速成长的早期阶段,产能及产销量弹性高,相较于同行业获得显着的超额增速。
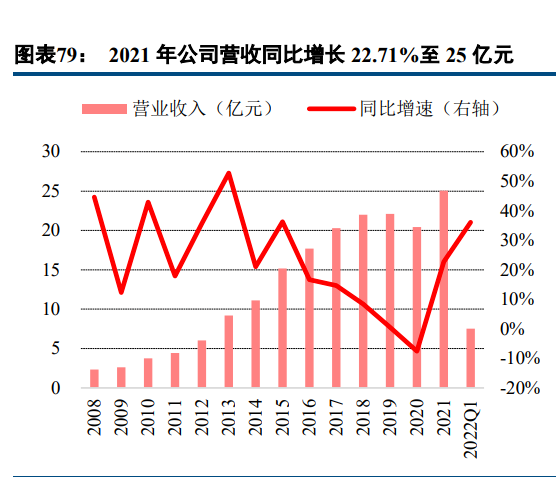
公司实现全产业链布局,玻璃纤维及制品仍为支柱业务。2012~2021 年,公司营收呈现多元化发展,玻璃 纤维及制品收入占比从 92.20%下降至 68.76%;化工制品(不饱和树脂等产品)收入占比从 7.80%提升至 27.24%。2015 年新增玻璃钢制品业务,收入占比保持稳定,从5.29%下降至3.77%;2018 年新增气体销售业务,收入占比较小,2021年仅占主营业务收入的 0.23%。公司产品布局逐渐完善,从横向、纵向两个方面积极扩展自身业 务,持续优化产品结构,其中玻璃纤维及制品仍为支柱业务。细拆玻纤结构,公司毡类及热塑纱产能占比预计 超过一半,并且在国内车顶毡市场的市占率已超过 50%。
公司近年来毛利率和净利率呈上升趋势,盈利空间充裕。2021 年,公司毛利率达33.72%,同比提升 5.33pct;净利率达 22.80%,同比提升达 9.56pct。2022 年一季度毛利率同比增长 5.78pct 至 38.81%;净利率同比提升 11.11pct 至 30.23%。分业务来看,公司玻璃纤维及制品毛利率明显高于其他业务;化工制品近年来毛利率相比其他业务增速最快,随着树脂项目产能的全面释放,盈利能力仍有提升空间。
公司期间费用率稳中有降,研发费用与人数持续上升。2015~2021 年,公司期间费用率整体趋于下降;截 至 2021 年,销售费用率同比下降 1.54pct 至 2.36%;管理+研发费用率同比下降 0.50pct 至 7.70%;财务费用率同 比下降 0.62pct 至 0.45%。近 3 年公司研发费用率稳定在 4.1%以上;研发人员数量稳步提升,2021 年研发人员 数量增至 263 人,占比提升至 11.4%。
内生+外延打造玻纤制品全产业链,可转债重磅加码短切毡产能
公司深耕玻纤制品领域,专注打造完整产业链。公司拥有以玻纤纱、玻纤制品及玻纤复合材料为主的纵向产业链;2015 年收购子公司常州天马集团,横向拓展至不饱和聚酯树脂业务。通过整合,公司实现了横向、纵 向产业链的延伸,形成了产业链优势并实现协同效应。公司与天马集团在原料、产品、设备、客户等方面存在 极高的相关度与协同性,天马集团生产的化工辅料是公司现有各类玻纤制品的重要原材料之一,而公司生产的短切毡、薄毡等玻纤制品则应用到天马集团玻纤增强材料产品中去,形成了较为完整的玻纤纱—玻纤制品—树 脂—玻纤复合材料产业链。
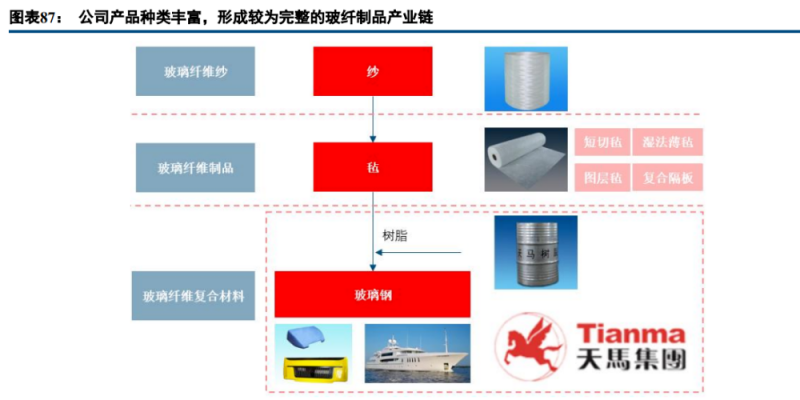
完整产业链形成原材料自给自足,材料成本持续降低。公司为国内为数不多的拥有玻纤生产、玻纤制品深加工到玻纤复合材料制造的完整产业链的玻纤企业。产业链的完整,使得公司能够按照上游产品性能,提高玻纤产品质量,降低生产成本与产品开发周期,提高企业的综合竞争力。2015-2021 年,玻璃纤维及制品的成本中, 材料成本占比从61.27%累计下降 14.99pct 至 46.28%,降本效应显着。2017-2021年,公司玻璃纤维及制品的单吨成本从5770元累计下降13.42%至4996元。
公司发行可转债助力玻纤纱产能增长50%,重磅加码传统高附加值产品。公司于2020年6月发布向不特 定对象发行可转换公司债券预案,同年12月完成募集5.5亿元,用于建设一条年产10万吨无碱玻璃纤维粗纱池窑拉丝生产线及配套制品深加工车间。项目投产前公司玻璃纤维及制品的产能为20万吨/年,2021 年9月该转债募投项目点火,2022 年一季度逐步实现达产,产能同比增长50%,有效缓解产能满负荷运行的状况。同时, 公司采用国际先进的玻纤池窑拉丝技术、自动化机器人,投产后预计可降低 50%以上人力成本。
可转债募投项目新增玻璃纤维粗纱产能10万吨/年,其中计划2 万吨粗纱加工为直接纱对外销售,5万吨粗 纱加工为短切纱对外销售,剩余 3 万吨粗纱加工为短切毡,本次募投项目还新增短切毡产能 6.88 万吨/年(其中 本次募投项目供纱 3 万吨,其余用纱由公司其他生产线提供)。短切毡相比较直接纱和短切纱而言,其销售单价和毛利率都具有更为明显的优势。以公司 2019 年披露数据为例,短切毡、短切纱、直接纱价格分别为 8900、 4500、3800 元/吨,毛利率依次为 38%、21%、17%。从应用领域来看,公司短切毡主要应用于汽车顶棚等应用,随汽车轻量化的推进,公司新增产能将有效消化,并且实现更高的毛利率。
短期自筹资金加码薄毡与树脂产能,强化产业链优势。1)薄毡:自筹资金拟新增 5 条薄毡生产线(2020、 2021 年各建成 1 条),全部建成后将推动薄毡产能由 4.35 亿平方米增加至 10 亿平方米。2)树脂:全资子公司 天马集团对原年产 2.5 万吨不饱和聚酯树脂生产线进行技改扩建,形成10万吨产能;全部投产后,公司将形成17万吨不饱和聚酯树脂的产能结构。远期智能制造基地建设与技改升级共同推进,加大力度提升市场份额。远期拟投资63.47亿元建设60万吨玻纤产能,截至2022年 4月公司已竞得拟实施该项目的土地,一期计划建设2条15万吨产线,加大力度提升 市场份额。2022年4月,公司公告称拟将常州天马集团3万吨产线升级改造成8万吨高端高性能玻璃纤维及特种织物生产线;定位于高强高模量纱及深加工制品,专用于风电及新能源汽车等高端领域。项目建设期12个月, 总投资 5.99 亿元;建成后现有产能将进一步扩充,产品性能得到优化和提升,持续加强公司市场竞争力。
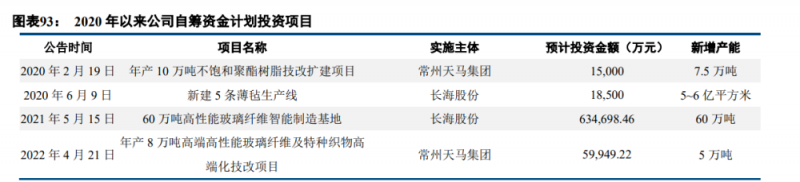
玻璃纤维毡布制品进出口情况
玻璃纤维毡布制品:风电市场未来可期
增强用毡布制品方面,年初部分风电织物生产企业手中仍有2020年订单尚未完成,而随着“双碳”工作启动,风电市场将迎来一个新的持续增长阶段,风电织物细分市场产业格局正在加速调整中。
工业用毡布制品方面,受玻纤纱原材料供应不足和价格上涨影响,部分中低端建筑用玻纤制品市场竞争较为激烈,部分企业通过实施技术装备提升改造或调整市场产品定位,实现差异化发展。此外高温滤料、土工格栅等环保类和基建类玻纤制品发展较为稳定。
电子用毡布制品方面,由于近年来电路板行业产能扩张明显,带动覆铜板及覆铜板上游玻纤布、铜箔和树脂三大原材料出现较大需求增长,其中玻纤布存在一定缺口。上半年国内各大电子布生产企业订单充足,价格持续攀升。
进出口情况
1.出口情况:3年来首次出现正增长
上半年玻璃纤维及制品出口总量达到75.9万吨,同比增长9.2%,3年来首次实现正增长;出口金额13.4亿美元,同比上涨32.11%,增速明显快于出口量增速。由于新冠肺炎疫情在全球范围内持续肆虐,欧美各国玻纤生产企业供给量持续萎缩,市场供需形势日趋紧张,下游各领域需求纷纷转向中国玻璃纤维及制品供应商。
分种类看,短切玻璃纤维、玻璃纤维制机织物(30cm以下)、玻璃纤维毡(450g以下)、玻璃纤维毡(450g以上)、玻璃纤维席、玻璃纤维制纤维垫等产品出口增幅均在20%以上,反映出国外市场在热塑、风电、房地产等细分市场的快速发展。
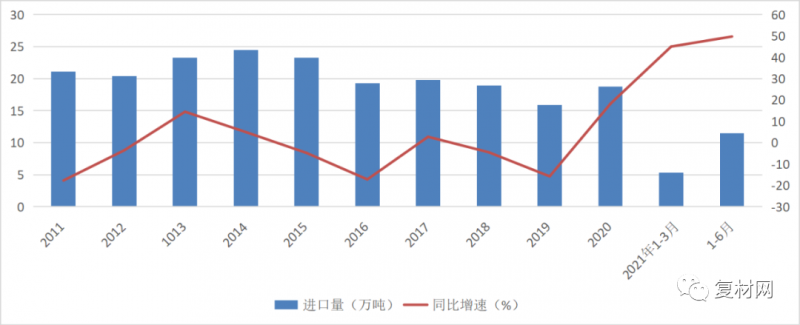
图3 玻璃纤维及制品出口变化情况
2.进口情况:继续保持高速增长
今年上半年我国玻璃纤维及制品进口总量达到11.5万吨,同比增长49.7%;进口金额6.3亿美元,同比增长36.7%。其中,玻璃纤维纱、短切玻璃纤维、玻璃纤维制机织物(30厘米以下)、玻璃纤维制机织物(30厘米以上)、玻璃纤维制纤维垫等产品进口增幅较大,增幅都在45%以上,反映出随着国内新冠肺炎疫情有效控制和宏观经济调控,内需市场正在稳步增长,不断为行业发展注入新动力。同时,也提醒行业需要继续对标各国玻纤企业,补强产品质量管控、品质提升和销售服务等弱势环节。
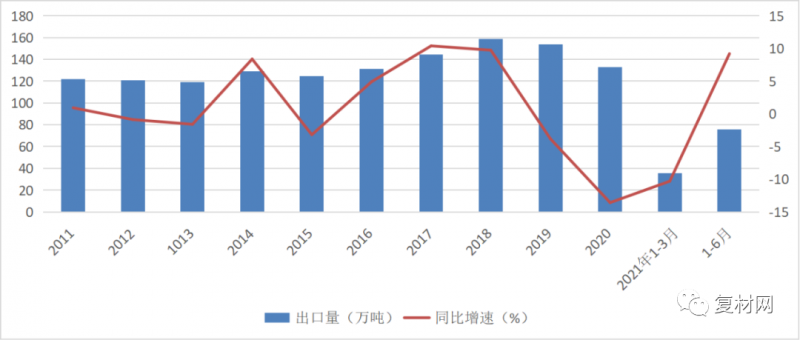
图4 玻璃纤维及制品进口变化情况
2020年电子用玻纤毡布制品产量约71.4万吨,工业用玻纤毡布制品产量约65.3万吨
2021年3月1日,中国玻璃纤维工业协会发布《中国玻璃纤维及制品行业2020年经济运行报告》(CFIA-2021报告),报告对2020年我国玻璃纤维纺织制品领域发展进行了统计汇总,并分析了数据背后的行业发展进程情况。
玻璃纤维纺织制品:产量快速增长电子用毡布制品:2020年我国各类电子布/毡制品总产量约为71.4万吨,同比增长4.54%。据国家统计局数据显示,2020年我国信息传输业基础设施投资规模同比增长16%,同时2020年我国累计实现洗衣机总产量8042万台,同比增长3.9%;彩电总产量19626万台,同比增长4.7%;冰箱总产量9015万台,同比增长8.4%。此外2020年全球PC出货量超3亿台,同比增长13.1%;全球5G手机出货量超2.8亿部,增长40%。随着智能制造和5G通讯持续推进,以及因疫情加速推进的智慧生活、智慧社会建设,带动电子通讯设备与设施市场快速发展。
工业用毡布制品:2020年我国各类工业用毡布制品总产量为65.3万吨,同比增长11.82%。据国家统计局数据显示,2020年我国房地产开发投资达到14.1万亿元,同比增长7%。随着后疫情时代对于房地产、基建等领域的投资加强,建筑外墙保温用网格布、窗纱、遮阳布、防火帘、灭火毯、防水卷材、壁布及土工格栅、膜结构材料、增强网布、隔热保温复合板材等各类建筑及基建用玻纤制品产量保持较好增长势头。云母布、绝缘套管等各类电绝缘材料则受惠于家电等产业的复苏,增长迅速。高温过滤布等环保类产品需求稳定。
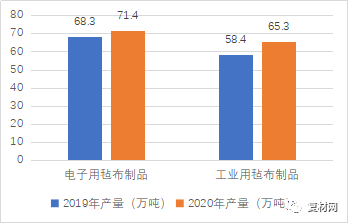
图4 部分玻璃纤维纺织制品产量变化情况
增强毡布制品:风电市场的异常火爆,带动各类方格布、多轴向布、缝编毡等相关制品产量大幅增长,部分企业产量增速接近50%。
20家玻纤生产知名企业
玻纤产业链中,玻纤生产及供应市场还处于巨头垄断格局。OC、PPG、JM、巨石、重庆国际、泰山等六大企业仍占据着全球近80%的玻纤产能。其中,芬兰Ahlstrom玻璃纤维无纺布及织物业务已被OC收购;而PPG的战略方向是涂料,玻纤已经从亚太撤出。目前,国内的巨石、泰山、重庆国际的总产能大概是250万吨/年,约占市场份额的70%;而威远、山东玻纤、邢台金牛的产能均未超过50万吨。
1. 美国欧文斯·科宁OwensCorning
欧文斯科宁(OC)公司是一家生产建筑材料和玻璃纤维复合材料的跨国公司,全球销售额逾50多亿美元。作为玻璃纤维生产技术的发明者,欧文斯科宁已在中国的上海设立了亚太区中心,采用当今国际最先进的离心法生产技术,在上海、广州、鞍山、武汉、天津投产了五家玻璃棉工厂。最令同行企业头疼的是,OC玻纤的质量好,并且价格不高!
2. 美国PPG工业公司PPGIndustriesInc
PPG创建于1883年,是一家领导全球的多元生产商,主要供应全球玻纤、涂料、玻纤与各种化学品。PPG是世界排名领先的连续拉丝玻纤制造商之一。主要应用于电子、热塑、热固与一般工业市场。全球不少的玻纤企业,都是采用PPG技术,特别是台湾的企业,国内的不少企业也是。但未来PPG有可能完全退出玻纤市场,因为PPG重心转移到了涂料。
3.佳斯迈威
JM成立于1858年,总部位于美国的丹佛市,经过148年的发展,已经成为一个在北美、欧洲和亚洲设有数十家生产基地,拥有近万名员工的跨国集团。公司主要产品为玻璃纤维及其衍生产品、聚酯长纤无纺布等。佳斯迈威公司于2016年2月29日曾宣布,对位于田纳西州埃托瓦的玻璃纤维厂进行扩产,以应对热塑性复合材料对玻璃纤维需求的增长。
4.中国巨石集团
巨石集团是全球最大的玻纤纤维专业制造商,作为世界玻纤的领军企业,巨石集团现有总资产180亿元,员工总数8000人,玻纤生产力超过100万吨,目标为120万吨。拥有浙江桐乡、江西九江、四川成都、国外埃及丶美国五个生产基地。前不久,在美国投资3亿美元建立一个年产8万吨玻纤生产基地。长玻纤产品牌号:362J、362K、352B。
5.泰山玻璃纤维有限公司
泰山玻璃纤维有限公司是以玻璃纤维及其复合材料为主业的国有大型企业,隶属于中国中材集团有限公司的全资子公司。泰山玻纤于1997年建成国内首条万吨级池窑拉丝生产线,经过十几年的发展,目前玻纤及制品总量已达到54万吨/年,目标为70万吨。为全球五大、中国三大玻璃纤维制造企业之一。长玻纤产品牌号:T635B、T635C、TCR735、TCR738、TCR739。
6.重庆国际复合材料有限公司
CPIC成立于1991年,前身是1971年成立的重庆玻璃纤维厂,1999年云天化进入,现由云天化集团有限责任公司主要控股,拥有总资产超过100亿元,员工总数6000余人。公司分别在重庆、上海、珠海、常州以及海外的巴西、巴林建有生产基地,玻纤年产能突破60万吨,玻纤布年产能达到1.5亿米。 生产规模居全国第二、全球第四。长玻纤产品牌号:LFT-PP适用:4305PM与4305N;LFT-PA适用:4301R;LFT-D:4305D;通用型:4300A等。
7.四川威玻新材料集团有限公司
四川威玻新材料集团有限公司始建于1957年,拥有总资产30亿元、员工3000余人,是中国第四大、世界第八大玻璃纤维专业制造商、四川华源是其下的公司。企业年生产无碱玻纤纱17万吨,玻纤织物40000吨,玻纤复合材料20000吨,高硅氧玻璃球及纤维10000吨,改性工程塑料5000吨。长玻纤产品牌号:EW758与EW768。
8. 山东玻纤集团股份有限公司
山东玻纤集团股份有限公司是于2013年12月改制成立的国有控股的股份制公司,拥有中碱纤维、ECR高性能纤维、ECER改性纤维、玻璃纤维装饰壁布、单丝涂塑平织窗纱、电子级玻纤毡、连续毡七大类近300多个品种的产品体系,玻璃纤维设计总产能25万吨,织物总产能2.3亿平方米;其中中碱池窑拉丝和ECR高性能玻璃纤维生产规模全国第一,玻纤壁布的生产规模全国第一。
9.四川省玻纤集团有限公司
四川省玻纤集团有限公司(原四川省玻璃纤维厂)是1968年由上海内迁到德阳的三线企业。公司是西南地区玻璃纤维产业集群的奠基者、发展者、带动者。公司资产总额13亿元,公司年产各种玻璃纤维纱4万吨,各种玻璃纤维布1亿米,复合材料300吨,光学玻璃600吨,主营玻璃纤维纱和玻璃纤维布(各型电工绝缘布、电子级玻纤布、环保过滤布、特种工业织物布等)同时兼营功能性复合材料、光学材料等多种产品的集团化公司。公司产品已广泛应用于电子、电器、环保、建筑、航空航天、国防军工等高新技术领域。
10.中材金晶玻纤有限公司
中材金晶玻纤有限公司成立于2004年1月18日,是由中国中材股份有限公司与山东金晶科技股份有限公司合资设立,注册资本20396万元人民币,公司拥有池窑拉丝生产线两条,2006年与美国PPG公司各出资50%合资成立了淄博中材庞贝捷金晶玻纤有限公司,一期已完成投资7950万美元,并成功引进PPG世界一流玻纤生产技术,产能达到60000吨/年。第三条池窑拉丝生产线预备建设中,届时总产能将达到12万吨。拥有玻璃纤维湿法薄毡生产线两条,年生产能力1.5亿平方米,产品品种达几十个。
11.台湾必成股份有限公司
1987年开始和美国PPG合资,目前台湾三个窑炉,大陆有四个窰炉,合计总产能23.4万吨年产能,主营产品:电子级及复合材料级玻璃纤维,其中PFG产量世界最大。凭借PPG技术移转,计划七月份开始生产长玻纤。
12.台嘉玻璃纤维有限公司
台嘉玻璃纤维有限公司,是由台玻集团于2001年6月在昆山投资设立,注册资本额为11,000万美金。现有四条世界上最先进的「池窑拉丝技术」玻璃纤维布生产线,主要生产玻璃纤维布及玻璃纤维纱,年产优质电子级玻璃纤维纱4万吨。
13.江苏长海复合材料股份有限公司
成立于2000年5月,总部坐落于长三角中心区域,江苏省常州市武进区。现有3座玻纤池窑生产线,拥有13万吨玻璃纤维产能,产能总量位居全国前五位。经过十多年的发展,公司已形成了10万多吨的玻纤制品产能,拥有玻璃纤维短切毡、玻璃纤维湿法薄毡、蓄电池复合隔板、玻璃纤维涂层毡等多个特种毡系列产品。
14.邢台金牛玻纤有限责任公司
邢台金牛玻纤有限责任公司是由上市公司冀中能源股份有限公司自筹资金独立兴建的无碱玻璃纤维生产企业,隶属母公司是世界500强企业冀中能源集团有限责任公司。2015年7月,邢台金牛玻纤与美国欧文斯科宁公司合作的年产4万吨Advantex玻璃配方玻纤拉丝生产线成功目前企业总资产超过9亿元,年生产能力达到7万吨。
金牛玻纤主要产品有各种规格的直接纱、高强环氧纱、SMC纱、毡用纱、喷射纱、无捻粗纱布、短切原丝毡、LFT长纤、双轴向织物、多轴向织物、缝编毡等品种。
15.建滔(连州)玻璃纤维有限公司
建滔(连州)玻璃纤维有限公司是KB建滔化工集团旗下分公司之一,位于连州市城北建滔工业园内,于2004年9月投产。主要是生产电子级玻璃布,现在月产能为1300万米左右,年产能为14300万米,年产值为4亿元人民币。
16.山东晟昊(裕鑫)玻璃纤维有限公司
山东裕鑫玻璃纤维有限公司成立于1997年4月,位于山东省新泰市羊流工业区,注册资金6188万元,公司占地面积80000平方米,是玻璃纤维及其制品的专业生产厂家,主要生产中碱、无碱玻璃纤维纱,各种规格的玻璃纤维网格布,玻璃纤维土工格栅,玻璃纤维墙布及遮阳布等六大类、五十多个品种。
17.陕西华特玻纤材料集团有限公司
陕西华特玻纤材料集团有限公司前身为陕西玻璃纤维总厂,于1966年由天津市迁入陕西兴平,是中国最大的特种玻纤生产企业,也是西北地区唯一的一家大中型玻纤生产企业。年产玻纤纱7000吨,玻纤织物2500万米,湿法薄毡3500万㎡,玻璃钢2000吨,是国内最早开发耐碱玻纤厂家。
18.林州光远新材料科技有限公司
林州光远新材料科技有限公司是集电子级玻璃纤维产品研发、生产、销售为一体的企业。总规模为年产10万吨电子级玻璃纤维纱和1亿米电子布,生产线采用先进的工艺技术,主要设备全部引进,工艺装备达到国际先进水平。专业生产电子级玻璃纤维纱、工业细纱和电子布、工业织物等,产品规格主有G25、G37、G50、G67、G75、G150、E110、E225、DE37、DE75、DE300、D450、D900等纱产品,以及7628、2116、1080、106等电子布产品。
19.江西大华新材料股份有限公司
江西大华新材料股份有限公司成立于1998年11月,是一家专业化生产玻璃纤维及各种玻纤制品的大型企业集团。公司一直注重科技创新发展道路,具备自主知识产权的玻纤浸润剂研制、铂金漏板加工以及玻纤配套设备的生产能力。总资产达10亿元人民币,年产DHG高性能玻纤9万吨,玻纤网格布1.5亿平方米,耐碱涂覆玻纤网格布加工能力达9000万平方米,其他玻纤制品年生产能力达5000万平方米。
20.江苏九鼎新材料股份有限公司
江苏九鼎新材料股份有限公司(原江苏九鼎集团股份有限公司),成立于1994年,注册资本17576万元人民币。公司专业从事玻璃纤维纱、织物及制品、玻璃钢制品的生产和销售。
21.宁津智远新材料有限公司
成立于2002 年,主要致力于消音隔热保温及高性能耐热纤维制品的研发生产与销售。主要产品有:玻璃纤维消音棉,玻璃纤维管,玻璃纤维成型件,玄武岩纤维消音棉,玻璃纤维针刺毡,玄武岩纤维针刺毡,玻璃纤维隔热垫,玄武岩纤维隔热垫,玄武岩纤维套管,玄武岩纤维带,消声器隔热套,排气管隔热套,增压器隔热套,净化器隔热套,尾气箱隔热套,电池保温套,发动机舱隔热棉,线束隔热套,油管隔热套,油箱隔热套,发电机组隔热套等。