但这些塑料在阻燃这个安全问题上的表现其实并不理想,阻燃及其相关产业伴随“汽车轻量化”一起成为汽车行业的热点。
01 汽车零部件用阻燃塑料发展方向
目前,用于汽车零部件的常见阻燃材料类型有PP、PA、PU、PC、ABS材料,以及由它们组成的各种改性材料和复合材料。
相比于传统燃油车,新能源汽车新增了电池组模块、充电桩及充电枪等部件。
单台新能源车电池组模块工程塑料的使用量约30kg,新能源车塑料壳体目前主要使用改性PP,以及改性PPS、PPO等耐高温塑料。
充电桩由于较高的使用标准和严苛的使用环境对工程塑料需求较大,每个充电桩约需6kg工程塑料,目前常见的主要有PBT、PA和PC等。
制备阻燃塑料时大多会将其极限氧指数LOI提升到25-35%左右,才能有效提升汽车整体安全指数。此外,加上目前电气化和碳中和的双重背景,塑料以及各种含有卤素的阻燃剂,都将会受到更多限制。
所以,未来阻燃塑料的发展方向除了需要足够的机械性能以满足轻量化需求之外,在电动汽车等领域还会需要材料注重电气、加工、环保方面的要求。
阻燃剂将会朝着无卤化及高性能化方向发展,而高性能阻燃剂研究重点将朝着复配协效阻燃技术、无卤化阻燃、膨胀型阻燃、超细化、纳米化技术、高效表面化学修饰技术以及多功能化技术等方向发展。
02 阻燃材料在汽车零部件上的应用
当下应用的阻燃塑料主要以PP、PU、ABS和PC为主,根据汽车零部件的特殊需求也相应有复合材料(合金化)、PA、PBT和PMMA等材料的使用。
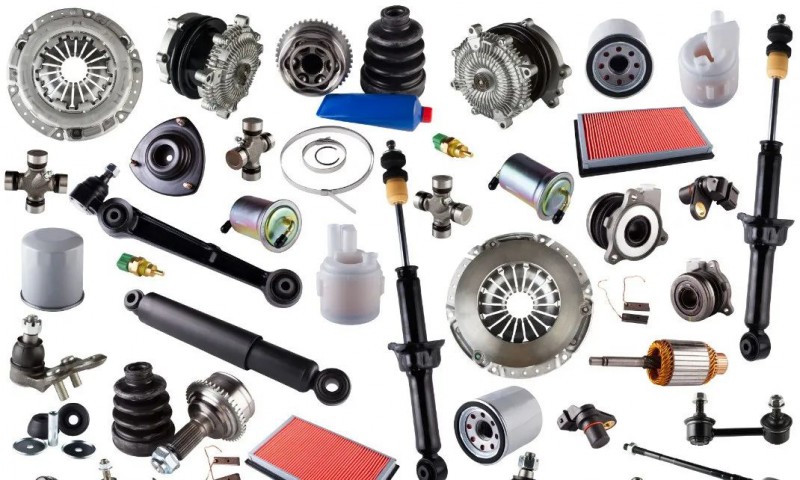
阻燃PP
PP是车用塑料中用量最大的高分子材料,具有优异的耐化学腐蚀,并且加工过程简单、成本低。广泛应用于汽车仪表盘、电池包外壳、门护板、立柱、座椅护板、保险杠等。
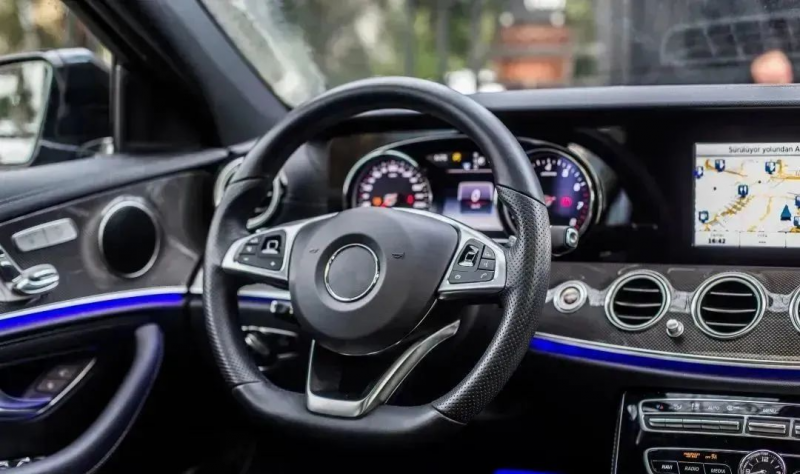
但由于未添加阻燃剂的PP阻燃性能很差,其LOI仅为17.8%,非常容易燃烧。对汽车阻燃用PP研究主要围绕对PP基体进行改性,同时通过添加低毒、无卤阻燃剂,开发具有优异力学性能和阻燃功效的PP复合材料。
目前,适用于PP的阻燃剂主要为添加型阻燃剂,应用较多的有卤系阻燃剂(如溴系阻燃剂、溴-锑协效阻燃体系)、无机填充型阻燃剂(如氢氧化镁、氢氧化铝)、磷氮系(如MPP、APP、MCA、磷腈、磷酸酯等)以及膨胀型阻燃剂(IFR)。
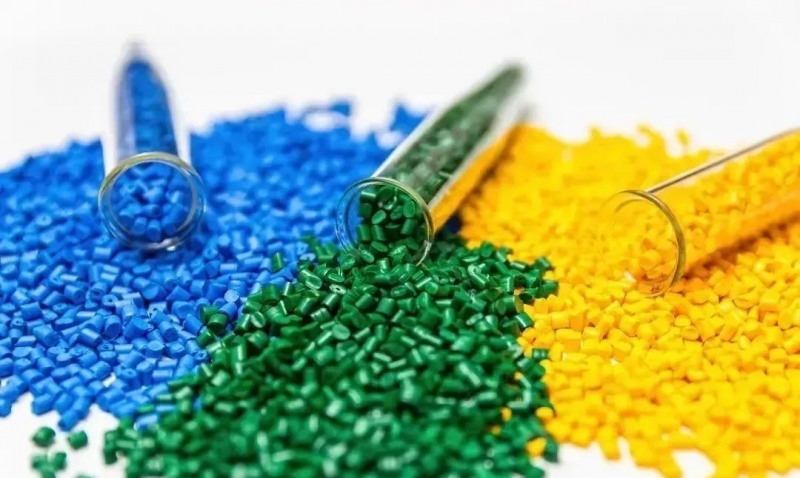
随着严苛的环保政策的施行,高分子材料用阻燃剂无卤化已是大势所趋。
结合具体案例来看,目前已经有以PP为基体,以长玻纤(LGF)为填充材料,加入磷氮系无卤膨胀型阻燃剂、MCA等,制备得到LGF增强无卤阻燃聚丙烯电池槽的例子。
制备过程中采用双母粒制备法,通过分别制备LGF母粒和无卤阻燃母粒,将两者混合均匀后直接注塑制得阻燃PP制品。
双母粒制备法避免了长玻纤母粒制造过程中,由于过度剪切引起的剪切区温度过高,引起阻燃剂降解和玻纤长度短造成的力学性能下降问题。
阻燃PP无卤化改性技术中,IFR因其对PP加工流动性和低密度优势影响最小、阻燃效率优异、用量少、低烟无毒等优点,被认为是无卤阻燃PP中最优前景的发展方向之一。
阻燃PP在中国起步较晚,但发展很快。特别是近年来增长迅猛的新能源汽车行业直接推动了阻燃PP需求量的快速增长,国内众多高校、科研机构以及企业参与到车用零部件阻燃PP的开发中来。
今后,车用阻燃PP的研究将重点聚焦于高效和环保:通过选择无卤阻燃剂、膨胀型阻燃剂、磷氮系阻燃剂以及复配型阻燃剂同时结合其他助剂,开发出性能优异的阻燃PP材料。
阻燃ABS
ABS在汽车行业崛起之前,也是全球用量最大的家电高分子材料之一。
据不完全统计,中国约80%的ABS消费量来自于家电领域,而这主要得益于ABS出众的表面涂装性能、耐久性和防腐性。
也是这些特点,让ABS在汽车涂装领域成为了典型。但ABS树脂的分子结构中只有C、H、O三种元素,所以不具备阻燃性能,在高温阶段的稳定性很差,极易燃烧。同时在燃烧过程中还会产生刺鼻气味和黑烟,无法直接用于汽车零部件。
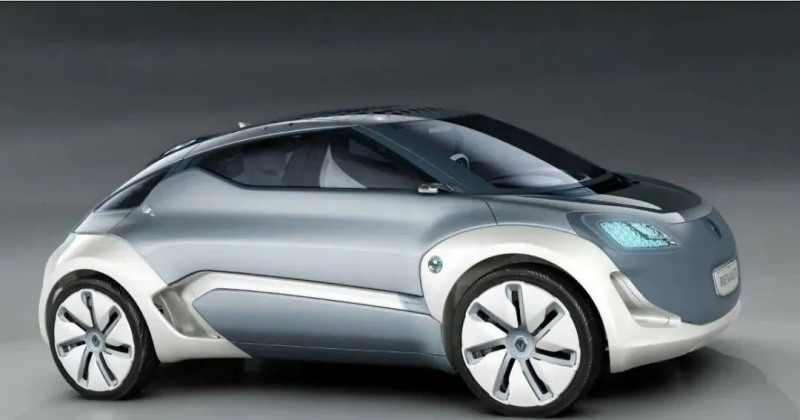
目前,ABS的主要应用方向是通过阻燃或耐高温改性,亦或者与PC共混合成PC/ABS复合材料。
对于ABS而言,卤系阻燃剂的阻燃效率比较高,其中溴系阻燃效果又好于氯系。虽然卤系阻燃成本低、效果好,但从业者众所周知,今后卤素阻燃会面临来自政策和环保法规的巨大压力。
所以,ABS的阻燃改性仍然是重要的研发方向。
不过对于阻燃标准严格的应用场景,溴系阻燃剂还是目前最主流的选择。据悉,用于电子电器产品中的ABS约有70%都采用溴系阻燃剂。
PC/ABS兼备二者优点,具有更好的HDT和稳定性,加工性能也更好,目前已是产量最大、技术最成熟的塑料合金,也是目前在汽车零部件领域应用最广泛的材料之一。诸如汽车仪表板、蓄电池组、车身、内饰等部位,都用到了PC/ABS材料。
不过要注意的是,在某些指标上还是有“1+1<2”的情况:PC本身是一种自熄材料,UL94可达V2级,但PC/ABS的阻燃性能有所下降,需要补足。
目前常用的除了卤系和磷系,值得关注的发展方向还有纳米阻燃剂,诸如纳米级的三氧化二锑、氢氧化铝、氢氧化镁以及纳米层状双氢氧化物等等。
阻燃PC
PC作为五大工程塑料之一,在汽车零部件上的应用也相当成熟,诸如汽车仪表板、车灯系统、加热板、除霜器甚至是一些PC合金制作的保险杠等等。
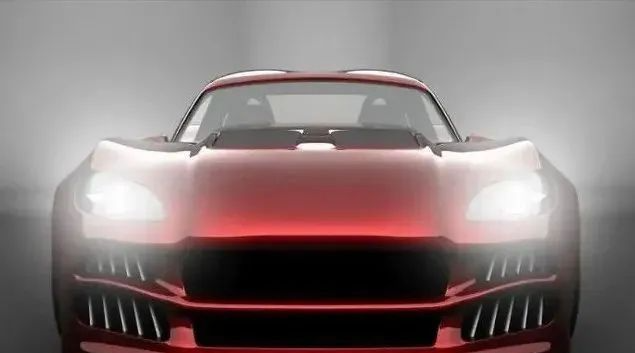
PC本身具有一定阻燃性,相较于其它高分子材料(如PE、PP等)拥有一定优势,LOI可到21-24%。然而对汽车零部件阻燃要求相对较高的应用领域,仍需要对其进行阻燃改性。
溴系阻燃剂能明显提高PC的阻燃性能,常用的有十溴二苯醚(DBDPO)、四溴双酚A(TBB-PA)等。但含溴的阻燃材料在高温下容易分解产生腐蚀性气体,使汽车零部件受损。
而且,溴系阻燃剂的添加会严重影响PC的透明性,同时也不符合欧盟无卤化、环保政策的要求。
当前,工业化的PC产品中使用最多的磷系阻燃剂。
主要是TPP、RDP和BDP
其中,TPP常温下为固态,热稳定性较差,在PC加工温度下容易挥发,仅发挥气相阻燃作用。
RDP和BDP常温下为液体,具有较好的热稳定性,可同时发挥气相和固相阻燃作用,同时BDP与PC有较好的相容性,可起到增速硬化的作用。
所以PC+BDP体系成为使用较多的一种体系,BDP添加比例大约为10%。
此外,含硅化合物作为新一代环保型阻燃剂,因其高效、低毒、无污染等特性,以及对PC加工性能和物理性能影响较小也逐渐受到关注,如聚硅烷、聚硅氧烷等。
汽车零部件用PC在选用阻燃剂时也在向无卤环保靠近,通过添加多种助剂或者制备复合型阻燃剂等途径,提升PC的综合性能。
此外,PC通过与ABS、PBT等组成复合材料也是提升PC加工性能和阻燃性能的不二选择。
其他阻燃材料
将PP、PU、ABS和PC中两种或以上高分子材料熔融共混制备的复合材料也是目前使用较多的一种材料,如PC/ABS,PC/PBT,PC/FR复合材料等。
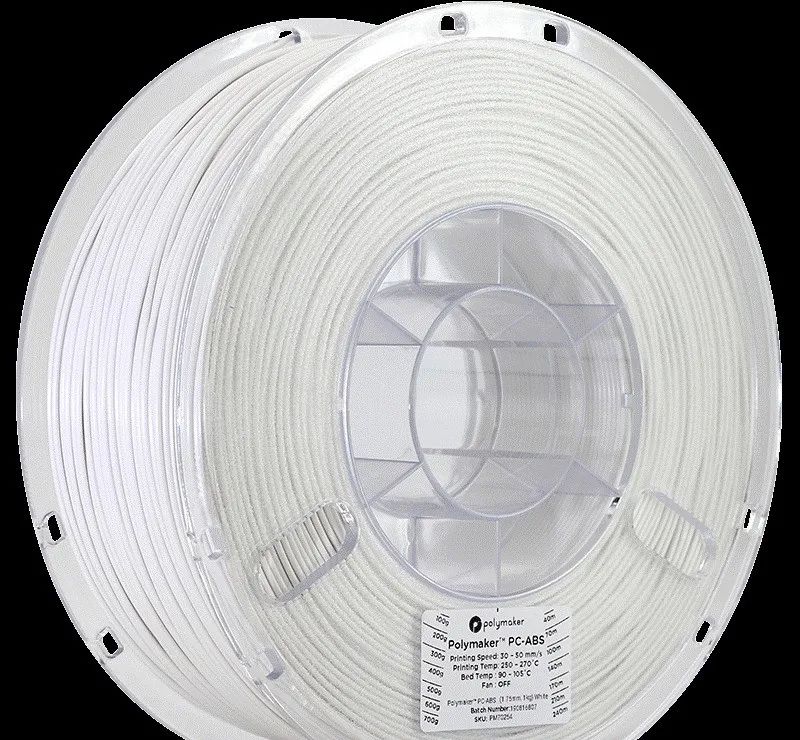
具体到案例上来说,Polymaker公司推出三款基于PC的3D打印材料,将其用于车用零部件的生产,三款产品分别为Polymaker PC-ABS、Polymaker PC-PBT、PolyMax PC-FR,这三款产品各有特色,在耐热性、耐冲击、易加工以及阻燃性能方面,均具有较好的表现。
Polymaker PC-PBT在科思创Makroblend?系列产品基础上进行改进,提升了材料综合性能。同样PolyMax PC-FR是在科思创Makrolon?产品上对阻燃性能做了较大改进,使材料UL94达到V0级,将该材料用于新能源汽车电池外壳。
普利特开发的阻燃高分子材料(如PC/ABS、PP、PA、PBT等)在动力电池上获得广泛应用,该系列材料均满足UL94 V0等级的阻燃及可靠电气性能的要求。
在长期物理耐久性方面具有优异的表现,提高动力电池能量密度的同时可以延长电池包的使用寿命,符合新能源汽车绿色环保、轻量化的发展理念。