高性能纤维是指对外界的物理和化学作用具有特殊耐受能力的一类特种纤维,是近年来化学纤维工业的主要发展方向之一,按照化学组成可分为有机高性能纤维和无机高性能纤维。高性能纤维不但是发展航空航天和国防工业迫切需要的重要战略物资,而且在推进各类战略性新兴产业和低碳经济、节能减排中起着不可替代的作用,是体现一个国家综合实力和技术创新的标志之一。日本、美国和欧洲发达国家高度重视并长期垄断着全球高性能纤维的研发、 生产和市场。2006年以来,在国家政策和财政的重点支持下,我国高性能纤维产业发展迅速, 建立了较为完整的国产高性能纤维制备技术研发、工程实践和产业体系,大幅缩短了与发达国家的差距,有效缓解了国民经济和国防建设对高性能纤维的迫切需求。以下对常见高性能纤维进行介绍。
碳纤维
碳纤维是一种含碳量在90%以上的纤维材料,具有质量轻、强度高、耐腐蚀、模量高、密度低、无蠕变、导电导热性能良好、非氧化环境下耐超高温、抗疲劳性好等特性,是发展航空航天、新能源、高端装备制造等高科技产业的重要基础材料,是制造火箭、导弹、战斗机、海军舰艇及多种尖端军事武器的必备关键材料,在国防军工领域有着不可替代的战略地位。
相关资料显示,目前碳纤维复合材料在军用飞机中的用量占比为30%——40%,大型客机用量占比为15%——50%。如美国F-22和F-35战斗机的碳纤维复合材料用量分别达到24%和36%,B-2隐身战略轰炸机的用量占比超过50%,美国“全球鹰”无人侦察机的用量达65%,“雷神”无人机用量甚至超过90%。同时在民用航空领域,B-787、A-380等大型客机的复合材料用量均已超过50%。我国军机、国产大飞机、卫星、航天飞船等也开始使用碳纤维复合材料,但应用比例和水平远低于国外,其中三代战斗机碳纤维和材料用量占比不足5%,四代战斗机用量虽有所增高,但仍未达到20%,国产大飞机的碳纤维复合材料用量不足15%,且均为进口。2020年全球碳纤维需求量为10.6kt,中国大陆地区碳纤维正在运行的产能约为3.6kt,实际产量约为1.8kt,居世界第二位。
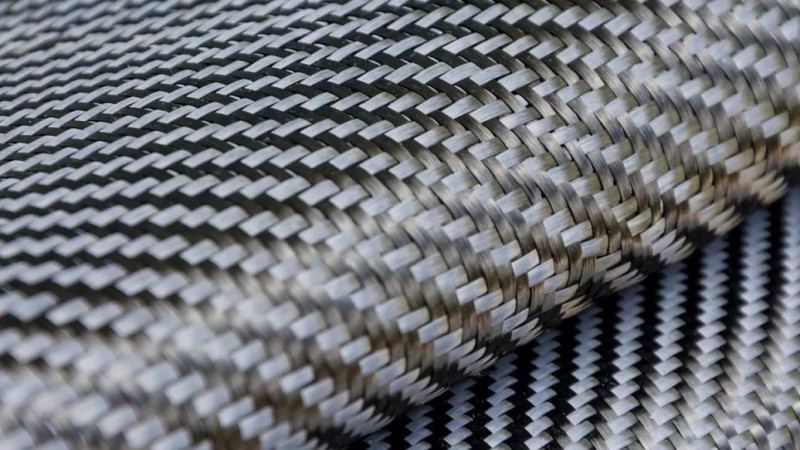
对位芳纶
对位芳纶具有轻质、高强、高韧、耐高温、透波、抗冲击和耐磨等优异的性能,在光缆增强、防弹装甲、石棉替代、个体防护等领域有着广泛的应用。全球对位芳纶市场属于典型的寡头垄断局面,北美和欧洲属于成熟市场,中国是新兴市场,作为潜在的芳纶用量大国,近年来我国对位芳纶的市场需求量增长率保持10%左右,远超全球平均水平。
随着电子通信、国防军工、轻量化材料、5G产业等对芳纶个性化需求的不断增多,带动了对位芳纶行业的高速发展,待开拓市场空间巨大。2020年全球对位芳纶产能为83.7kt,至2022年预计总产能94.6kt,主要集中在杜邦、帝人和可隆三家企业,占全球对位芳纶产能的90% 左右,而国产企业占比较低。
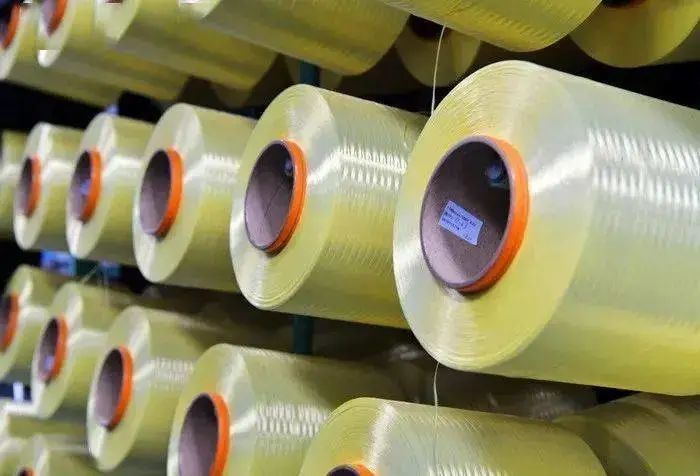
间位芳纶
间位芳纶具有优异的耐热性(分解温度大于400℃,长期使用温度大于 200℃)、耐焰性(极限氧指数大于29%)、出色的耐高温酸碱性、电绝缘性和良好的加工性能,广泛应用于高温防护服、高温滤料、电器工业和复合材料领域。
2017年间位芳纶全球用量35kt,2018年增至43.2kt,其中50%产自杜邦公司,预计2025年将达到66kt,主要用于绝缘纸和安全防护领域,对纤维性能要求高,技术门槛高。2020年,全球间位芳纶市场规模达到63亿元,预计2026年将达到103亿元,年复合增长率为7.3%。
目前国内间位芳纶供应质量已接近国外产品,市场容量逐步递增,并且具有较强的价格优势,由此迫使美国杜邦和日本帝人已基本退出国内间位芳纶市场。但我国间位芳纶产品的60%以上用在相对低端的高温过滤材料领域,技术门槛相对较低,其次才是用于安全防护和绝缘纸领域。与国际市场相比,我国制造的间位芳纶特别是绝缘纸性能仍有很大的提升空间。
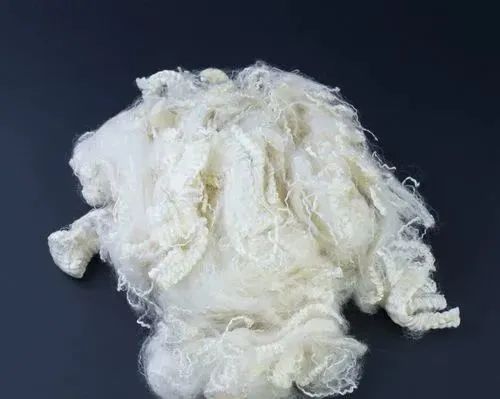
芳纶III
芳纶Ⅲ具有比对位芳纶更高的强度、模量,更好的抗冲击性、阻燃性和抗热氧老化性,同时具有更低的介电常数、介电损耗和更好的复合性能等,在缠绕、抗冲击和结构透波复合材料方面及光纤/缆增强方面具有重要的高端应用,已批量用于洲际导弹发动机壳体、直升机蒙皮、单兵头盔、军警防弹衣等领域。
目前俄罗斯的芳纶Ⅲ仍处于世界领先水平,是唯一可批量生产芳纶Ⅲ的国家。与国外相比,我国芳纶Ⅲ系列产品种类较为单一,主要为高强型和高模型,缺少根据不同用途适当调整性能的差别化品种。
超高分子量聚乙烯(UHMWPE)纤维
UHMWPE纤维具有优异的力学性能、耐化学腐蚀性、耐候性、高能量吸收性、低导电性及防水性等特性,是密度最低的高性能纤维,广泛应用于军事防弹、航空航天、海洋工程、安全防护、交通运输、体育器材、生物医疗和家纺用品等领域。
迄今40多年的发展过程中,UHMWPE纤维的生产技术不断改进,纤维性能、产量均有长足进步,带动了从UHMWPE原料到纤维制品的全产业链的全面高速发展。特别是在防弹制品领域,鉴于UHMWPE纤维的密度仅为对位芳纶的2/3,在轻质防弹制品方面表现出明显优势,且其防弹效果优于芳纶,现已成为美国防弹市场的主要纤维。
目前UHMWPE纤维总量的45%用于生产防弹制品,世界范围内不断发生局部战争以及恐怖事件,对UHMWPE纤维的需求将进一步扩大。随着在工业及民用领域应用的进一步拓展,国内外各公司不断开发UHMWPE纤维新品牌,纤维产能也逐步增大。2011年全球UHMWPE纤维的总产能约30kt,2019年纤维产能达到64.6kt, 而需求量则达86kt,2020年纤维产能突增到80kt 左右,其中国内UHMWPE纤维企业的快速发展对全球产能的突增做出了较大贡献。
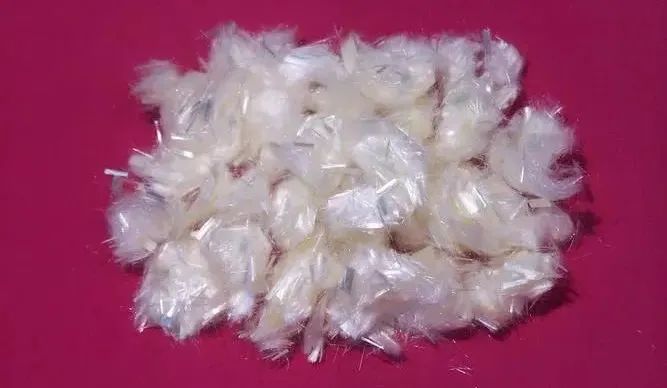
聚酰亚胺纤维
聚酰亚胺纤维不仅具有较高的强度和模量,而且耐化学腐蚀性、热氧化稳定性和耐辐照性能十分优越,在航空航天、国防建设、新型建筑、高速交通工具、海洋开发、体育器械、新能源、环境产业及防护用具等领域得到广泛应用,此外还可以作为性能更加优越的防弹服织物、高比强度系列绳索、宇航服、高温防护服等。
目前,我国冶金行业每年需隔热、透气、柔软的阻燃工作服约10万套,水电、核工业、地矿、石化、油田等领域每年需30万套防护用服,需耐高温阻燃特种防护服用聚酰亚胺纤维500t左右,而消防救援防护服在20万套/年以上,这为聚酰亚胺纤维在高温特种防护领域的应用提供了广阔空间。
聚酰亚胺是一大类材料的总称,化学结构非常丰富,对应于性能和功能不同的纤维品种,具有更大的应用范围。这些品种在聚合物制备、纤维成型等方面有很多共性问题,有利于实现多品种的开发,从而可满足空天极端环境对高性能纤维的需求,将在我国空天探测活动中发挥重要作用。
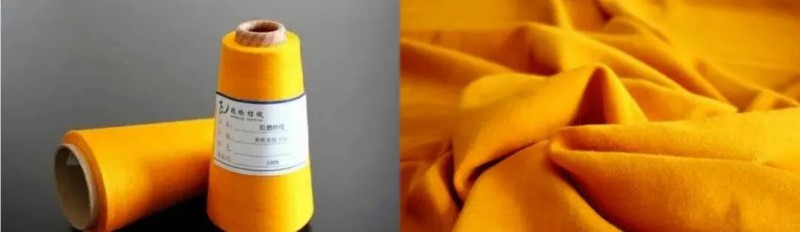
聚苯硫醚(PPS)纤维
PPS是一种分子主链由苯环与硫原子对位相互交替排列、结构规整性好的高分子材料。具有良好的力学强度、耐热性和耐化学腐蚀性等综合性能。
PPS纤维是目前少数可熔纺加工的商品化高性能纤维,是火力发电厂、垃圾焚烧厂等高温、腐蚀尾气袋式除尘核心部件的基础材料,具有过滤精度高(PM10.0、PM2.5)、服役时间长(4 年)的特点。
日本东丽、日本东洋纺等深入研究并掌握了高品质PPS短纤维生产技术,垄断了PPS短纤维的全球市场,产量占全球80%以上。近年来,我国采用纳米复合改性技术,进一步提高了PPS纤维的综合性能,打破国外对高品质PPS纤维的垄断,为我国高温过滤产业提供性价比最具优势的PPS系列产品,为该产业提升市场竞争力、保持国内领先、开拓国际市场提供了重要保障。
PPS纳米复合纤维作为热防护装备的新型基础材料,其发展可打破国外材料对特种防护装备的垄断,并降低高端防护装备成本,提高热防护装备在我国石油化工、金属冶炼、应急救援等苛刻环境下的普及性,市场需求显著,对推动我国个体防护装备研发和提高应急救援水平具有重要意义。
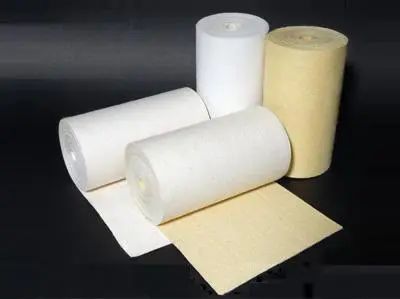
聚芳酯纤维
聚芳酯是一种通过酯键连接芳环而成、一般具有热致液晶特性的特种高分子。在聚芳酯熔融纺丝过程中,其高分子链高度取向,从而赋予聚芳酯纤维高耐热、高强度、高模量、低吸水、抗蠕变、介电常数低等优异特性,广泛应用于航空航天、产业资材等领域,具有重大的军事和工业价值。
1977年聚芳酯纤维被美国国家宇航局(NASA)选用作“火星探险者” 号登陆车的安全气袋,实施软着陆;2004年,又一次用在“勇气”号和“机遇”号火星探测车上;2003年起日本平流层飞艇也开始使用该纤维。平流层飞艇是工作在临近空间的新型平台,具有驻空时间长、成本低和分辨率高等优点,有广阔的商业应用前景和重要的国防价值,被美国、日本、英国等发达国家列为重要发展技术。平流层飞艇囊体蒙皮材料的制备技术是飞艇发展的关键,主要使用聚芳酯纤维作为高比强度织物,结合高阻隔性材料、黏合剂复合构建增强复合材料。
目前,全球仅日本可乐丽有年产2000t的纤维产品VECTRAN,美国塞拉尼斯、日本住友都准备开发该纤维。由于聚芳酯纤维的综合性能优异,该纤维对我国实行限购,且价格极高,严重制约了我国在上述领域的发展。
东华大学聚芳酯纤维的研究课题已于2019年5月18日通过中国纺织工业联合会组织的鉴定,该技术的工业化生产和实施将有力地打破国外对我国的封锁和垄断,满足我国在上述重要领域的迫切需求,解决“卡脖子”的关键纤维及其复合材料问题。
.jpg)
聚对苯撑苯并双唑(PBO)纤维
PBO纤维是目前强度最高、综合性能最好的高性能有机纤维,是继芳纶纤维、碳纤维之后的新一代高性能纤维。其突出性能优势主要表现在以下几方面:
力学性能优异,PBO纤维强度达到5.8GPa(芳纶为2.9——3.4GPa),模量达到280GPa(芳纶为64——144GPa),为有机纤维中最高,同时也高于碳纤维等无机高性能纤维;
耐热性能好,PBO纤维热分解温度达到650℃,同样为有机纤维中最高,耐热工作温度比芳纶高100℃左右;
阻燃性能优异,PBO纤维极限氧指数达到68%(芳纶为29%),在有机纤维中仅次于聚四氟乙烯纤维;
化学稳定性极好,除溶解于100%的浓硫酸、甲基磺酸、多聚磷酸等强酸外 , 在其他所有的有机溶剂和碱中都是稳定的,强度几乎不变。
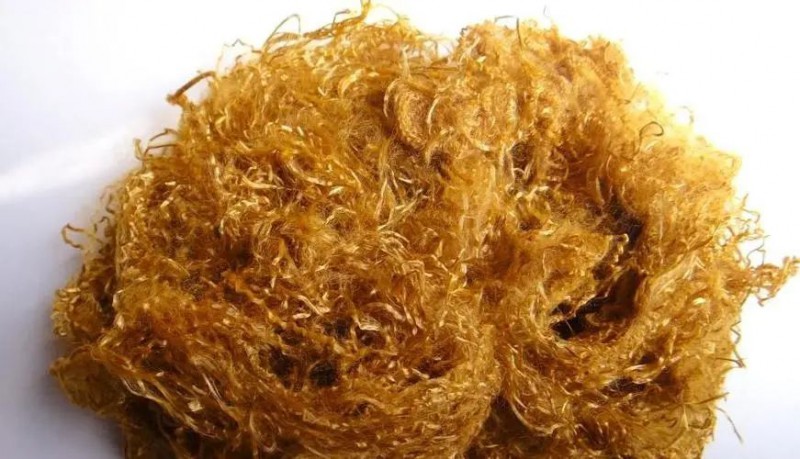
因此,PBO纤维被认为是下一代装甲防护用基础材料及航天结构部件、航空结构/隐身领域的关键原材料,同时在光缆、车辆防护、人体防护、建筑增强和体育用品等民用领域也有着广阔的应用前景,是一种军民两用的高端纤维材料,对支撑传统复合材料产业实现性能跨越式提升、推动升级换代具有重要意义。
碳化硅(SiC)纤维
SiC纤维具有高强度、高模量、耐高温、抗氧化、抗蠕变、耐腐蚀、与陶瓷基体相容性好等一系列优异性能,是一种非常理想的增强纤维,在航空、航天、兵器、船舶和核工业等一些高技术领域具有广泛的应用前景,是发展高技术武器装备以及航空航天事业的战略原材料。
由连续SiC纤维增强的SiC陶瓷基复合材料(SiCf/SiC)强度高、密度低、使用温度高,在高推重比发动机上的应用具有显著的减重效果,是替代现有超高温耐热合金的最佳选择。SiCf/SiC复合材料在航空航天发动机的耐热部件、高超音速运输推进系统、原子核反应堆材料等领域具有广阔的应用前景。
日本、美国等发达国家针对高性能连续SiC纤维开展了大量的基础和应用研究,并已实现了连续SiC纤维的工业化生产。由于连续SiC纤维在军事领域的重要应用前景及其在航空、航天等高技术领域的战略地位,长期以来,西方发达国家对该产品实行垄断政策,并对我国进行严密的产品和技术封锁。
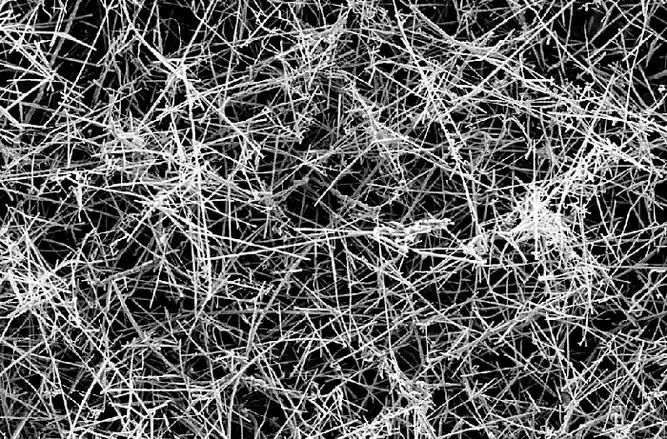
玄武岩纤维
玄武岩纤维是以基性火山岩为主要原料,经高温熔融后拉丝制备的连续无机非晶态纤维。由于火山岩具有较高的二氧化硅、三氧化二铝和铁氧化物等组分,因此赋予玄武岩纤维较高强度、高模量、低导热、耐磨、耐低温高温和良好化学稳定性等特性,目前被广泛应用于混凝土、高温过滤、建筑保温、车辆工程、风电、石油化工和体育休闲等行业。
玄武岩材料作为宇宙天然产物,不仅在地球上广泛分布,在月球、火星以及浩瀚的宇宙中都广泛存在,开发深化玄武岩纤维的制备技术,对人类未来利用太空原位资源具有深远的意义。此外,还有部分高性能纤维如氧化铝连续纤维、氮化硼纤维、硅硼氮纤维等,仍处于研发待量产阶段,需进一步提升前驱体热处理技术,突破产业化生产和应用关键技术,提高纤维性能的稳定性。
其中上海榕融新材料科技有限公司计划2021年年底在上海临港建成连续氧化铝纤维生产线,并预计3年内产量达5kt;山东东珩国纤新材料有限公司于2020年7月在东营投建年产100t连续氧化铝纤维生产线。
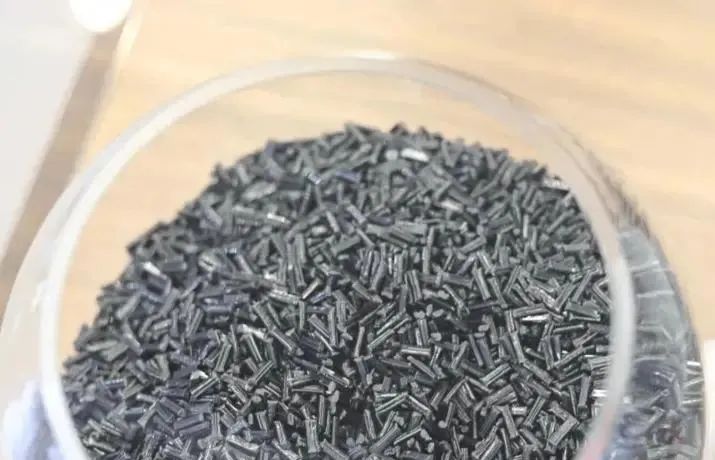
02 高性能纤维产业的国际发展现状及趋势
作为主要的技术发源地,并得益于强大的工业基础和长期积累,美国、日本和欧洲等国家与地区在高性能纤维及其复合材料领域已形成先发优势。美国的优势集中在黏胶基碳纤维、沥青基碳纤维、氧化铝纤维、芳纶纤维等方面,复合材料应用技术也遥遥领先;日本在聚丙烯腈基碳纤维、沥青基碳纤维和陶瓷纤维等方面具有明显优势;欧洲在纺丝装备方面基础好、水平高。他们在高性能纤维材料方面具有很高的相互依存度,技术与资本交叉融合,形成产业生态圈。俄罗斯及东欧国家继承了苏联自主发展的纤维材料技术,其中有机高性能纤维、黏胶基碳纤维技术平较高,各种热加工设备实用可靠,可基本满足其国防工业需求。以下分别对各高性能纤维的国外发展现状和趋势进行介绍。
碳纤维
聚丙烯腈基碳纤维最早是由日本大阪工业试验所的进藤昭南在1959年研制开发成功。在其工作基础之上,日本碳公司在1962年以聚丙烯腈纤维为原料,通过预氧化处理、碳化处理最终制备得到了通用级碳纤维。英国皇家航空研究所(RAE)的W. Watt等人1963年发现在预氧化处理的过程中对聚丙烯腈纤维施加一定的张力,抑制聚丙烯腈原丝在预氧化热处理过程中的收缩,可以明显提高最终碳纤维的力学性能,这一技术的使用为现代聚丙烯腈基碳纤维的生产奠定了工艺基础。
在此之后,英国的Courtaulds公司和日本碳公司都分别在1969年建成了高性能聚丙烯腈碳纤维的工业生产装置。日本东丽工业株式会社与东邦人造丝株式会社在1971年之后也相继加入了聚丙烯腈基碳纤维的生产大潮之中。聚丙烯腈基碳纤维自20世纪60年代末研制开发成功以后,经过1970—1980年的稳定发展以及20世纪90年代的快速发展,其生产制备技术已成熟。
目前,聚丙烯腈基碳纤维产量占全球90%以上,已经分化为大丝束纤维(以美国为代表)和小丝束纤维(以日本为代表)两大类。大丝束适用于普通的工业、民用和体育休闲领域;而小丝束纤维代表世界聚丙烯腈基碳纤维发展的最先进水平,追求高性能,其中日本东丽生产的聚丙烯腈基碳纤维T1100的拉伸强度已经达到了7.0GPa,是目前为止世界上力学强度最高的聚丙烯腈基碳纤维。世界上最主要的碳纤维生产国是日本,其中东丽、东邦人造丝及三菱人造丝依靠其先进的原丝制备和碳化技术等优势,在质量上处于全球领先地位,已发展了高强、高模及高强高模三大系列。
高强度碳纤维已从T-300(力学强度为3.53GPa,模量为230GPa),上升到T-1100(力学强度7.0GPa,模量约324GPa);高强高模并重的“M60J”抗拉伸强度为3.82GPa,最高模量可达588GPa。美国卓尔泰克(Zoltek)公司(已被日本东丽全资收购)和德国SGL集团是大丝束碳纤维的主要生产商,其中美国是大丝束碳纤维的主要生产国。2020年国外主要碳纤维生产企业信息如表1所示。
表1 2020年国外主要碳纤维生产企业信息
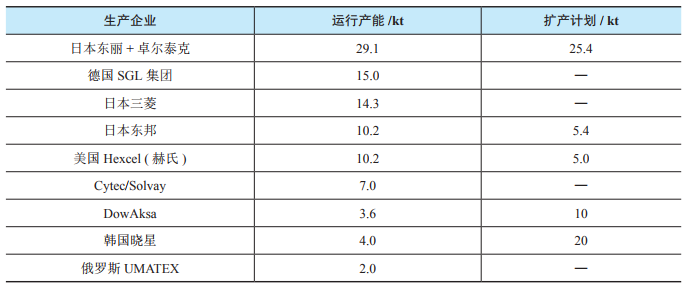
注:本表数据来自市场调研
对位芳纶
对位芳纶最早由美国杜邦公司于20世纪60年代开发成功,1972年开始工业化生产,随后荷兰、日本、韩国及俄罗斯等国家也开始了各自的研究工作。
作为主要技术发源地,并得益于强大的工业基础和长期积累,美国杜邦和日本帝人在对位芳纶领域拥有绝对的技术优势。杜邦在美国、日本和爱尔兰等多国建立对位芳纶生产基地,2016年时产能为34kt,但自2017年关停美国Cooper River 5kt/a装置后,直至2020年其对位芳纶产能一直维持在29kt/a。帝人的对位芳纶生产基地主要建在日本和荷兰,2020年产能达到32kt,并计划到2022年扩产增加约25%的产能,预计产能达到39kt/a。其中,帝人在日本松山的对位芳纶为三元共聚对位芳纶,是采用聚合-湿法纺丝一步法而成的,商品名为Technora®,产能一直维持在3kt/a。2019年杜邦和帝人对位芳纶产能占全球总产能的83%,2020年由于国内对位芳纶企业的扩产,这两家公司的产能下降至72%。除美国、日本之外,韩国可隆也是较早的对位芳纶生产企业,2020年其产能扩至7.5kt/a ;韩国晓星和泰光也有对位芳纶产品供应,产能分别为1.7kt/a和1.5kt/a。
在对位芳纶应用方面,安全防护、防弹材料用纤维占30%,车用摩擦材料用纤维占30%,光学纤维保护增强用纤维占15%,轮胎用纤维占10%,橡胶增强用纤维占10%,其他用纤维占5%。发达国家在高性能纤维及复合材料方面相互依存度高,技术和资本交叉融合,产业规模逐年扩大,积极重组联合,对大工业应用提前布局。随着高性能对位芳纶全球市场的急速发展和需求增长,对位芳纶及其复合材料新一轮技术突破正在加速推进,同时,全球行业垄断格局也在不断加剧,优势企业主导地位难以撼动。国外主要对位芳纶生产企业产品布局如表3所示。
表3 国外主要对位芳纶生产企业产品布局
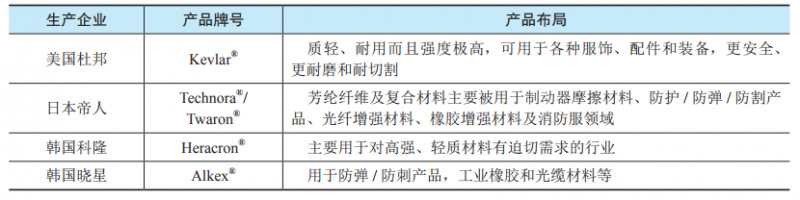
间位芳纶
杜邦公司占据了全球间位芳纶一半以上的市场份额,其产能一直维持在25kt/a,近年来大幅扩大Nomex芳纶纸产能,拟关停部分间位芳纶产能。杜邦公司参与供应链的每一个环节,从多方面控制着全球间位芳纶市场,在短纤维方面,Nomex 纤维用于服装和纺纱,在其他终端领域,杜邦只授权特定纺纱厂,并不向所有终端开放。日本帝人也是间位芳纶老牌供应商,多年来其间位芳纶产能也一直维持在4.5kt/a左右。此外,韩国也有少量间位芳纶供应,分别是韩国Woongjin公司和HUVIS公司,产能分别为1.2kt/a和50t/a。国外主要间位芳纶生产企业产品布局如表4所示。
表4 国外主要间位芳纶生产企业产品布局
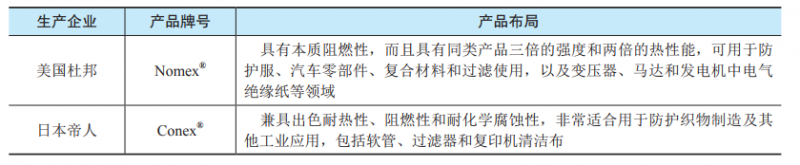
芳纶Ⅲ
芳纶Ⅲ主要由全苏合成纤维科学研究院和全俄聚合物纤维科学研究院进行研发,生产集中在特威尔和卡门斯克两家公司,产品品种主要包括SVM、Armos和Rusar 系列,总产能估计约2000t/a。其中SVM和Armos 是苏联时期实现产业化的,而Rusar是俄罗斯于1990年代采用干喷湿纺工艺开发的新型杂环芳纶,此后其高强高模型Rusar-S(强度5.5——6.4GPa,模量160GPa)和耐热阻燃型Rusar-O[极限氧气指数(LOI)高达40——45]也相继开发成功,尤其是Rusar-S在下游需求驱动下,生产技术不断更新。近几年,俄罗斯多家研究单位联合开发出一种四元共聚型的Rusar-NT纤维,这种纤维是在Armos的三元结构中引入了更经济的含氯第四单体,其强度预计可达到7GPa,弹性模量可达180——200GPa,LOI达40以上,代表了杂环芳纶研发的最高水平。目前Armos已装备俄罗斯多种高性能武器系统,如用于俄罗斯的SS-24、SS-25及当前技术最先进的“白杨 -M”(即 SS-27)等洲际导弹Ⅰ、Ⅱ、Ⅲ级发动机壳体上,发动机质量比达到0.92以上。俄罗斯最新的布拉瓦潜射导弹也采用了Armos纤维用于发动机壳体,此外,俄罗斯还采用Armos制备了BOLIT系列芳纶头盔,并装备了部队,其最新型号的芳纶头盔防弹V50达到600——650m/s,超过了美军PASGT头盔(609m/s)和德军现役头盔(620m/s),且质量仅约1.25kg,大大降低了士兵的负重,提高机动性。俄罗斯芳纶Ⅲ除用于树脂基复合材料增强纤维之外,还用于橡胶增强、消防服、绳缆、缝纫线、降落伞等。
UHMWPE纤维
UHMWPE纤维是由荷兰DSM公司于1978年发明的,美国霍尼韦尔公司购买荷兰DSM公司专利技术并于1984年首先实现了该纤维的产业化,之后荷兰DSM公司与日本东洋纺合作于1986年实现产业化。DSM公司是UHMWPE纤维的发明者,在UHMWPE纤维生产技术和应用开发方面也一直保持世界领先地位。该公司拥有UHMWPE聚合工厂,生产纤维级UHMWPE树脂专门供应本公司纤维生产,除了荷兰本土之外,还在美国和日本建有多条UHMWPE纤维生产线。2009年DSM公司UHMWPE纤维总产能就已超过10kt/a,2012年纤维产能扩至13.2kt/a。除了UHMWPE纤维产能一直领先之外,他们一直研发新产品,开发了强度最高的SK99纤维(强度>40cN/dtex)、高强抗蠕变的DM20纤维、高抗切割的3G12纤维以及医疗用Purity纤维,并开发了专用于UHMWPE纤维的耐磨涂层技术。针对不同应用需求,DSM还基于UHMWPE纤维开发了高防弹防护性能的防弹板、防刺防护背心、雷达罩以及与碳纤维复合材料等。2020年3月,DSM宣布开发生物基UHMWPE纤维,以致力于减少碳排放,并宣称到2030年至少60%的UHMWPE纤维采用生物基原料制成。美国霍尼韦尔公司虽然最早实现了UHMWPE纤维的产业化,但由于其使用的萃取剂对大气层有破坏作用而面临禁用的问题,使其UHMWPE纤维的扩产受到限制,产能上不及DSM在美国投产的UHMWPE纤维生产线,纤维强度也比不上DSM的同类产品,但霍尼韦尔公司是UHMWPE防弹无纬布的发明者,开创了UHMWPE纤维在防弹领域的应用。霍尼韦尔公司的UHMWPE纤维产能一直伴随美国军方对防弹防护的需求在增长,2009年纤维产能为1kt,2012年提高到2kt,最近一次的扩能计划是在2019年,纤维产能扩大到3kt/a并维持至今。霍尼韦尔公司基于其UHMWPE纤维开发了多种规格的Spectra Shield系列防弹防护基材,用于制备软式及硬质防弹制品,包括军用和警用防弹衣、防弹板、防弹装甲等,还将UHMWPE纤维与对位芳纶复合成功解决了UHMWPE纤维基防弹头盔凹陷度大的问题,大大提高了UHMWPE纤维在军用防弹头盔领域的应用,并进一步提高了防弹装甲的防弹性能,其在UHMWPE纤维防弹应用方面的研究一直居于世界领先地位。
聚酰亚胺纤维
20世纪60年代,美国杜邦公司的纺织前沿实验室和苏联相关研究机构就开始了聚酰亚胺纤维的研究工作,但限于当时聚酰亚胺树脂的合成与纤维成型方面整体技术不成熟,纤维制备成本较高,聚酰亚胺纤维没有得到迅速推广和应用。至20世纪70年代,苏联报道了聚酰亚胺纤维的相关研究,生产规模小,产品仅限应用于军工装备、航空航天中的轻质电缆护套等领域。后来,法国罗纳布朗克公司开发了m-芳香族聚酰胺类型的聚酰亚胺纤维,由法国Kermel公司进行商品化开发。如今,为迎合高温气体过滤市场不断增加的温度及化学反应等特殊要求Kermel又开发了Kermel-Tech聚酰胺-酰亚胺纤维。该纤维持续工作温度达到220℃,玻璃化转变温度高达340℃,在极高工作温度下仍可保留其优异的力学性能,目前已被广泛用于能源生产、高温过滤、法国空军作战服、南极科考、极限攀登等严酷环境。20世纪80年代中期,奥地利Lenzing AG公司(目前技术为德国赢创公司独有)以甲苯二异氰酸酯(TDI)、二苯甲烷二异氰酸酯(MDI)和二苯酮四酸二酐(BTDA)为反应单体,推出了商品名为P84®的聚酰亚胺纤维,这也是目前最主要的聚酰亚胺纤维产品之一。P84®纤维可在260℃以下连续使用,瞬时温度可达280℃。该纤维具有不规则的叶片状截面,比一般圆形截面增加了80%的表面积,使其在高温过滤领域得到广泛应用。2009年赢创公司扩大了P84纤维的生产规模,于2010年7月宣布装置投产。经过近10年的发展,赢创公司相继推出了综合性能更优异的P84®HT、P84Premium等创新型纤维产品。以P84Premium产品为例,纤维细度为1.3dtex ,比表面积高达约435m²/kg,比常规2.2dtex的产品又提高了近12%。卓越的除尘效率可带来更低的压降,节约引风机电耗,延长滤料使用寿命,大大降低企业的运行成本,经济效益显著。
PPS纤维
全球PPS树脂主要生产企业有美国Ticona公司,产能占比9.6%;日本东丽株式会社,产能占比17.6%;日本DIC株式会社,产能占比21.7%;比利时索尔维集团,产能占比12.8%;日本吴羽化学株式会社,产能占比6.8%等,年产能均高达150kt吨以上。其中,Ticona和东丽掌握了多等级多品种的PPS纤维级切片的生产技术,是PPS纤维级切片的主要供应商。目前,也仅有Ticona和东丽具有长丝级PPS树脂的生产能力。21世纪以来,东丽首先采用市场兼并策略,收购了美国飞利浦公司和兰精公司的PPS短纤维技术,成为目前全球PPS短纤维的最大生产商。其次,东丽和东洋纺等日资企业深入研究并掌握高品质PPS短纤维生产技术,垄断了PPS短纤维的全球市场,产量占全球总产量的80%以上。为提高PPS短纤维在高温过滤领域的市场竞争力,东丽和东洋纺等国外PPS短纤维生产企业,通过整合上下游产业链,实现了细旦、异形化PPS纤维制备技术及应用开发,显著提高了滤袋的过滤精度,实现了5mg/m³的超净排放标准;另外,东丽针对除尘滤袋使用寿命短的难题,系统开展了高强PPS纤维的研究,制备了断裂强度高达5.5cN/dtex的短纤维,大幅度提升了高温滤袋的使用寿命,在高端PPS纤维应用领域具有显著的全球影响力。在其他应用领域的拓展方面,帝斯曼公司基于PPS的综合性能,制备了高可靠性和耐久性PPS质子交换膜;东丽将PPS纤维制备成微孔直径大于1.0μm的网眼织物,并与高分子电解质进行复合制备复合电解质膜,应用于电池隔膜领域。
未来PPS纤维的发展趋势主要概括为两点:
PPS纤维的应用技术研究,拓展其应用领域,目前国内外PPS纤维集中应用于燃煤电厂、垃圾焚烧、化工厂等苛刻环境的滤袋产品,市场规模小,且无法发挥PPS纤维优异的综合性能。
PPS纤维的高性能化研究,提高PPS纤维的力学强度、抗氧化性、细旦化和异形化, 加强PPS纤维产品在国际市场的竞争力。
聚芳酯纤维
聚芳酯纤维由美国伊斯曼柯达(该业务后被杜邦和塞拉尼斯收购)、CBO公司 (Carborundum)、塞拉尼斯公司(Celanese)的科学家们首先进行开发。1976年,伊斯曼柯达的Jackson报道了热致液晶聚芳酯(商品名X7G®)可由PET和乙酰化后的对羟基苯甲酸共聚制得,但由X7G®纺成的纤维强度、模量较低,实用价值较小;随后,CBO公司与日本住友化学公司合作开发Ekonol®纤维,其强度为4.1GPa,模量为134GPa,达到高性能纤维的水平,但是都处于实验室研究阶段,并未见工业化报道。由于聚合原料、配方设计、聚合设备、纺丝设备、热处理设备等各方面的制约,真正实现工业化的则是塞拉尼斯和日本可乐丽合作开发的Vectran®纤维。1990年可乐丽西条工厂开始生产Vectran®纤维产品,2005年4月,可乐丽公司并购了塞拉尼斯先进材料公司的高性能纤维业务,成为Vectran®纤维的世界唯一生产商。2007年随着市场需求的快速增长,可乐丽公司对其在西条市的生产装置进行扩能,产能从600t增加到了1000t。2008年可乐丽在北美无纺布及非织造展览会(Techtextil North America)上推出了溶液染色的Vectran®HT新品种,有蓝、绿、橘红等色泽,其抗紫外光性、色牢度和强度均较好,同时还引入了细旦丝产品。为满足日益增长的市场需求,可乐 丽在2017—2018年间将产能由1000t拓展至2000t规模,并计划进一步扩产,预计在2022年将增至年产3000t的规模。
PBO纤维
基于宇宙开发和军事装备等尖端科技领域的需要,20世纪六七十年代,美国空军Wright- Patterson实验室开始了对芳杂环聚合物的基础研究,寻求高强度、高耐热的高性能聚合物的加工制备方法。同一时期,斯坦福大学研究所(SRI)的Wolf等在该领域开展科研攻关,设计了PBO聚合物。但受限于单体制备技术的限制,合成的聚合物分子量较低,PBO的优异性能未能表现出来。20世纪80年代中期,美国陶氏(Dow)化学公司获得了该专利技术,继续开展研究,探求新的单体合成路线和技术路线。1991年陶氏和日本东洋纺开始合作开发PBO纤维。1994年东洋纺出资30亿日元建成了400t/a的PBO单体和180t/a的纺丝生产线。1995年春,东洋纺获得陶氏的授权,开始PBO中试及生产研究,并且取得了小批量PBO纤维产品,1998年10月200t/a的装置正式投产,并确定PBO纤维的商品名为ZYLON。其后2000年左右PBO纤维的生产能力达到380t,2003年达到500t,2008年达到1000t,近年来达到2000t/a。目前世界上的PBO纤维的生产被东洋纺垄断,大部分的文献和专利都是东洋纺公司所有。其纤维产品主要供美国武器装备、航空航天事业、太空资源的开发以及其他尖端科技领域,纤维生产工艺严格保密,相关产品对我国实施禁售。
碳化硅纤维
采用先驱体转化法进行连续SiC纤维的研发可以分为三代:
第一代的典型代表是日本碳公司(Nippon Carbon)的Nicalon NL202纤维和日本宇部兴产公司(Ube Industries)的Tyranno LoxM纤维,在空气中1000℃时仍然保持稳定,但由于纤维中含有较多的氧和游离碳,在空气中1000℃以上或者惰性气氛中1200℃以上将发生显著的分解反应并伴随结晶的迅速生长,导致纤维的强度急剧降低,严重限制了其在陶瓷基复合材料上的应用。
针对第一代连续SiC纤维的问题,日本、美国等国采用不同的技术路线,研制了低氧含量的第二代SiC纤维,典型代表是日本碳公司采用电子束辐照方法替代原有的空气不熔化处理后制得的Hi-Nicalon纤维和日本宇部兴产公司的Tyranno ZE纤维,这种低氧含量的纤维在1300℃的空气中或者1600℃的惰性气氛中能够保持稳定。
随后,在此基础上使纤维中的杂质氧、游离碳含量进一步降低,碳硅比接近化学计量比,结构上也由原来的β-SiC微晶状态、中等程度结晶变为高结晶状态,从而研发出能耐更高温度的第三代连续SiC纤维。其典型代表是日本碳公司的Hi-Nicalon S纤维、日本宇部兴产公司的Tyranno SA纤维以及美国COI Ceramics的Sylramic纤维。
虽然同为第三代SiC纤维,但彼此的制备方法和性能各不相同。Hi-Nicalon S纤维是日本碳公司在电子束辐照交联的基础上,通过在纤维烧成过程中加氢脱碳,进一步将Hi-Nicalon纤维的富余碳去除,从而实现了近化学计量比的组成。Tyranno SA纤维是宇部兴产公司将聚碳硅烷与乙酰丙酮铝反应得到聚铝碳硅烷,从而在先驱体中引入铝元素作为烧结助剂,利用碳热还原反应同时脱去多余的碳和氧,最后经过高温烧结致密化达到高结晶近化学计量比的组成与结构。Sylramic纤维是将钛元素引入聚碳硅烷得到聚钛碳硅烷,随后在纤维烧成过程中引入烧结助剂B元素,经过高温烧结致密化也实现了高结晶近化学计量比。这种纤维现在由ATK-COI陶瓷公司生产,该公司通过在氮气中进一步加热纤维制备了表面富含BN层的Sylramic-iBN纤维。与Sylramic SiC纤维相比,Sylramic-iBN SiC纤维具有更大的晶粒,更好的抗蠕变性和更高的抗氧化性。第三代SiC纤维,尤其是高结晶近化学计量比的SiC纤维,由于制备温度较高,晶粒尺寸较大,在组成、结构和耐温性能上更加接近纯SiC块体材料。连续SiC纤维由第一代、第二代到第三代的发展过程中,有以下基本特征:
纤维的元素组成逐渐接近SiC的化学计量比,杂质氧、自由碳的含量明显降低;
纤维的微观结构由无定形态、微晶态逐渐形成完善的β-SiC结晶甚至高结晶状态;
纤维的耐温性能显著提高,而且,随着组成与结构的不断优化,纤维的密度和模量都有逐渐提高的趋势。
玄武岩纤维
目前全球玄武岩纤维的产量为30——40kt,国外的年产量不足10kt,主要由乌克兰和俄罗斯等国生产,其中以俄罗斯的Kamenny VEK公司较为成熟,目前已经能实现1200孔漏板稳定成纤,此外俄罗斯还有Sudaglass公司、Ivotsteklo公司等生产玄武岩纤维,工艺技术较成熟。另外乌克兰的Technobasalt公司、乌日(Toyota)公司,奥地利Asamer公司也依托苏联的工艺技术,在乌克兰建立了生产线。受性价比等因素制约,每个公司的产能均不高,根据实际情况在300——2000t不等。美洲和非洲地区也有生产玄武岩纤维的报道,如2016年俄罗斯Sudaglass公司在美国俄亥俄建立分公司,2019年美国Mafic公司在北卡罗来纳州的谢尔比市开始生产玄武岩纤维,但是考虑到当地技术成熟度等因素,产能不稳定,该地区的玄武岩纤维仍然以从亚欧买入后加工为主。乌克兰和俄罗斯地区都是依托于苏联的玄武岩纤维熔化成纤技术。该技术主要以顶部燃烧浅层熔化为主,熔化效率较低,采用铂金导流管技术,该技术获得的玻璃液品质高,但是设备维护比较复杂。由于国外复合材料研究起步早、应用广、技术先进,目前玄武岩纤维的功能化和差异化品种也一直由国外引领,我国处于跟跑阶段,如汽车保温、隔声方面、风电叶片增强等方面。国外玄武岩纤维生产企业产能情况如表5所示。
表5 2020年国外玄武岩纤维生产企业产能情况
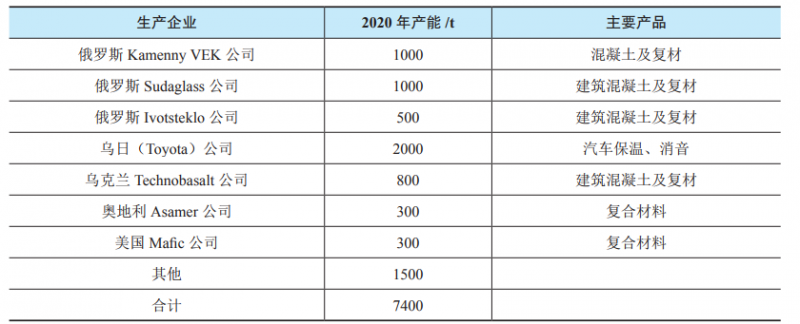
注:本表数据来自市场调研
03 高性能纤维产业的国内发展现状
在国家政策扶持和相关部委的大力支持下,通过各类科技项目的实施,专项能力建设和国家级创新研究机构设立等,我国高性能纤维经过数十年的发展,基础研究、技术和产业都取得很大进步,已经建立起完整的高性能纤维制备、研发、工程实践和产业化体系,不断取得突破性进展,大幅缩短了与发达国家的差距,目前已成为全球范围内高性能纤维生产品种覆盖面最广的国家。以下对主要高性能纤维的国内发展现状分别进行介绍。
碳纤维
我国聚丙烯腈基碳纤维的研制开发工作已有60多年历史。在20世纪60年代初,吉林应用化学研究所最早开始研究聚丙烯腈基碳纤维的生产技术和工艺,并在70年代初完成了碳纤维生产的连续化中试装置。在此之后,东华大学、上海合成纤维研究所、中国科学院山西煤化研究所等科研单位和院校也相继开展了聚丙烯腈基碳纤维的研制及开发工作。经过“十一五”至“十四五”期间的集中技术攻关,国产T300级碳纤维性能基本达到国际水平,航空航天领域应用渐趋成熟;干喷湿法T700级碳纤维实现了千吨化生产,但主要以民用领域为主,航空领域应用处于初级阶段。
目前,中国仍处在以T300和T700为主要增强体的第1代先进复合材料的扩大应用阶段,T800级碳纤维的工程化应用尚处研制阶段,而国外航空航天等领域已经大规模应用以T800级碳纤维为主要增强体的第2代先进复合材料。在碳纤维领域,我国处于跟跑地位。国产碳纤维原丝形成了二甲基亚砜(DMSO)、二甲基乙酰胺(DMAc)、硫氰酸钠(NaSCN)三种生产工艺体系,干喷湿纺和湿法纺丝工艺技术逐渐完善,生产效率进一步提升;碳纤维核心技术不断突破,在实现T300级碳纤维产业化的基础上,又相继实现了T700级、T800级,以及24K以上工业用大丝束碳纤维产业化生产,同时,M40J、M55J等高强高模碳纤维也突破关键技术,处于工程化阶段。但与日本东丽相比,我国二甲基亚砜系列产品尚未覆盖日本东丽同系列碳纤维品种。
T1000级及以上更高性能碳纤维产业化生产技术尚未完全突破,不能有效满足航空航天、国防军工等领域需求。我国碳纤维生产企业有中复神鹰、光威集团、恒神股份、吉林精功、上海石化、中简科技等企业,但因缺乏对基础科学问题与规律、核心技术与关键装备的系统深入研发,产品性能与生产稳定性与国际龙头企业有差距。高精度计量泵、耐腐蚀喷丝板、超高温石墨化炉等设备仍依赖进口。2020年国内碳纤维生产企业产能信息如表6所示。
表6 2020年国内碳纤维生产企业产能信息
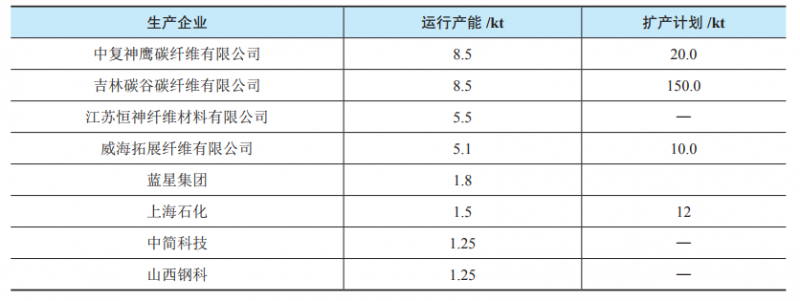
对位芳纶
国内对位芳纶的年消耗量在1.1kt左右,其中光纤领域用量近6000t,防护材料用量约1000t,汽车领域(胶管、刹车片等)用量约2500t,其他工业用约1500t,但80%的产品仍需依赖进口。
随着我国交通运输、光纤通信、高速铁路、航空补强、轻量汽车子午胎用帘子布及刹车片等领域和防护领域应用的快速发展,对位芳纶的需求将呈现更加旺盛的局面,预计2025年国内对位芳纶的需求量达到30kt。
2019年国内对位芳纶产业发展稳中向好,产量实现小幅增长,但国内市场仍呈供不应求态势,总体市场缺口较大,产品价格较2018年上涨了约20%。我国早期对位芳纶生产企业主要有中蓝晨光、苏州兆达、烟台泰和以及仪征化纤。2017年起中化国际集团开始投入对位芳纶生产,在东华大学的技术支持下,将苏州兆达对位芳纶生产线搬迁至扬州,并与其合资成立中化高性能纤维材料有限公司,2019年开始其二期工程5kt/a生产线的建设,于2020年底建设成功,总产能达5.5kt/a。烟台泰和新材股份有限公司2020年在宁夏地区扩建3kt/a的对位芳纶生产线,叠加烟台1.5kt/a,目前共有4.5kt/a的对位芳纶产能,此外,泰和新材正在进行技改项目,预计将进一步提升产能1.5kt/a。泰和新材在2020年收购民士达,募资建设年产3kt的高性能芳纶纸基材料产业化项目。国内主要对位芳纶生产企业近年来产能情况如表7所示。
表7 国内主要对位芳纶生产企业产能情况(单位kt)
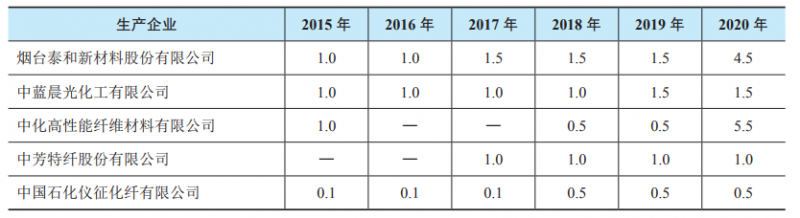
间位芳纶
2017年国内间位芳纶产量约为8.5kt,净进口量约1.1kt,表观消费量超过9.6kt。
由于间位芳纶下游市场整体不景气,并且过滤材料领域竞争激烈,产品价格走低,此外,间位芳纶原料价格大幅上涨,双重因素导致企业经营压力较大。在此市场环境下,部分公司(包括广东彩艳和杭州九隆)相继关停其间位芳纶生产线,导致国内间位芳纶产业集中度提高。
目前国内间位芳纶的生产企业主要为烟台泰和新材料股份有限公司和超美斯新材料股份有限公司(原圣欧芳纶),产能分别为7kt/a和5kt/a。2018年,由于美国军队换装导致杜邦纤维供应紧张以及芳纶原料供应紧张,引起间位芳纶市场供不应求,纤维价格有所提升。2019年,国内间位芳纶产量实现较大增长,产品仍以过滤材料和防护材料为主,高端产品国产比例仍较低。行业整体运行平稳,产品逐步向差异化、功能化、时尚化发展,扩大了高端领域应用。
目前,国内间位芳纶生产厂商和军方展开合作生产作战套服,军队与武警的大人员基数及高频率战损打开间位芳纶产量消化渠道,也为其提供庞大的市场空间。在市场需求的推动下,泰和新材宣布新增4kt/a的间位芳纶生产线,并于2021年8月投产,公司间位芳纶的产能达到万吨级。
芳纶Ⅲ
芳纶Ⅲ生产线最早由中蓝晨光化工研究院有限公司在2009年建成,开始Staramid F-368和F-358系列产品的生产,性能与俄罗斯Armos相当,产能为50t/a,解决了我国杂环芳纶国产化“有无”问题,填补了国内空白。
2013年以后,中蓝晨光开始致力于研发制造第二代芳纶Ⅲ的生产技术,并于2015年初获得了公斤级纤维样品,力学性能优异。之后进一步优化纺丝组件设计,实现了单纺位200——300tex丝束的纺制,性能水平与75——100tex丝束一致,即股丝束密度提高了3倍。
在目前,国产芳纶Ⅲ拉伸强度达到5.0GPa,弹性模量达130——160GPa,性能居国内批产有机纤维之首,达到俄罗斯Rusar批产产品水平,已批量稳定生产并用于军工领域,解决了国防急需,具有重要意义。除中蓝晨光外,国内还有广东彩艳股份有限公司、四川辉腾科技股份有限公司以及中国航天科工六院46所等先后开展了杂环芳纶的研究开发工作。2008年,由广东彩艳承担的国家“九五”重点科技攻关杂环芳纶专题项目和杂环芳纶的核心原料M-3单体研制专题项目通过了科技部的验收。2010年,四川辉腾自主研发生产的商品名为“芙丝特”的杂环芳纶通过国家权威机构检测,并进一步开发杂环芳纶复合板型材和成型构件产品,现已具备50t/a芳纶Ⅲ及100t/a芳纶Ⅲ先进复合材料生产能力。中国航天科工六院46所于1990年代开始研究F-12杂环芳纶,通过对聚合-纺丝-后处理纤维工艺不断优化和完善,1999年研究成功,之后依次进行了3t/a中试、5t/a放大和20t/a产业化及产品应用技术,在国内率先设计研制出多种规格的F12纤维及其织物,其性能达到国际先进水平,产能达50t/a,最近正准备将F-12产能扩至100t/a,以满足我国航空航天及高端战略武器的需求。
UHMEPE纤维
随着UHMWPE纤维在军品、民品特别是量大面广的各类缆绳和家纺等领域的应用开发,国内UHMWPE纤维需求量稳步递增,纤维产能逐步扩大。
2010年我国UHMWPE纤维生产企业20余家,总产能17kt/a,至2015年发展至30余家,总产能达26.6kt/a。然而,30余家UHMWPE纤维生产企业中年产千吨级的企业仅8家,大多数企业产能仅为300t/a左右,产品单一,生产成本也居高不下。2016年,江苏九九久购买了东华大学专利开始建设UHMWPE纤维生产线,成为国内首个UHMWPE纤维生产规模达万吨的企业,其纤维产品投入市场后引发了国内UHMWPE纤维的价格战。之后,部分工艺、技术落后的企业逐渐退出UHMWPE纤维市场,部分企业则通过重组或吸收资金重建纤维生产线,同时也有一批新的企业投资UHMWPE纤维产业。
目前,九九久公司UHMWPE纤维产能已达16kt/a。此外,山东如意集团于2018年宣布投资建设UHMWPE纤维生产线,产能为10kt/a ;浙江毅聚、江苏领誉也于2018年后开始投入UHMWPE纤维行业,预计产能在3kt/a以上。这些企业生产线全部建成之后,我国UHMWPE纤维的产能将超过60kt/a,占全球生产能力的3/4。国产UHMWPE纤维及制品国际市场竞争力也不断提高,外贸出口量也由50%逐步增大到超过70%。
目前,国内UHMWPE纤维生产企业有20余家,其中产能过千吨的生产企业如表8所示。
表8 国内UHMWPE 纤维主要生产企业产能汇总
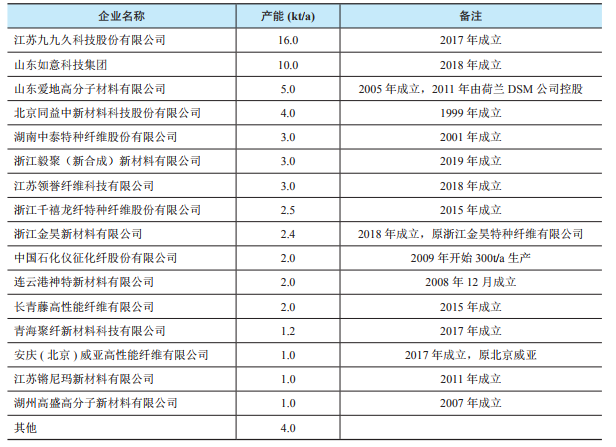
聚酰胺纤维
近年来,我国聚酰亚胺纤维产业得到迅猛发展,相关科研机构也开始重视聚酰亚胺及其纤维的研究与开发。
我国在20世纪60年代由上海合成纤维研究所率先试行过小批量聚酰亚胺纤维生产,主要用于电缆的防辐射包覆、抗辐射的绳带等,最终没有实现聚酰亚胺纤维的规模化开发。20世纪70年代,基于聚酰亚胺纤维独特的综合性能和特殊领域发展的需要,相关单位又恢复了聚酰亚胺纤维的研究工作。
目前,国内聚酰亚胺纤维生产企业主要包括长春高崎聚酰亚胺材料有限公司、江苏奥神新材料股份有限公司和江苏先诺新材料科技有限公司。他们采用不同的生产工艺,形成了耐高温型、高强高模型聚酰亚胺纤维的商品化生产,在环境保护、航空航天、尖端武器装备及个人防护等领域发挥重要作用,也使得我国高性能聚酰亚胺纤维生产技术位居世界前列。中国科学院长春应用化学研究所是较早从事聚酰亚胺 研究的单位之一,开发出一条独具我国特色的聚酰亚胺合成路线,取得了包括美国及欧洲专利在内的数十项专利。2008年在吉林省科技厅的支持下,该所开展了吉林省科技发展计划重大项目“耐热型聚酰亚胺纤维”的研究工作,先后突破了聚酰胺酸纺丝溶液的制备和聚酰胺酸初生纤维的酰亚胺化技术等关键工艺技术瓶颈。开发的聚酰亚胺连续化纺丝技术拥有自主知识产权,工艺成熟,具备了产业化技术基础,生产的聚酰亚胺纤维技术指标达到或超过合同规定的技术指标,综合性能优于商品化的P84纤维。2011年江苏奥神联合东华大学自主开发聚酰亚胺纤维。他们在全球范围内首次提出并建立了“反应纺丝”的新原理和新方法,并围绕干法纺丝成型过程中“反应纺丝”这一创新性思路,攻克了纺丝浆液的合成、纤维干法成型与后处理以及设备的成套等一系列关键技术,建成了国际上首条干法纺耐热型聚酰亚胺纤维1kt/a生产线,生产了甲纶SuplonTM短纤、长丝及短切纤维等系列产品。相关成果荣获纺织工业联合会科学技术进步一等奖,国家科技进步二等奖,经专家鉴定,一致认为整体达到国际先进水平,其中“反应纺丝”技术处于国际领先水平。经过近十年的发展,目前江苏奥神已形成了3kt/a聚酰亚胺纤维生产能力,产品广泛应用于高温过滤、特种防护、国防军工、信息通信等领域。
江苏先诺成立于2013年,是一家专注于高性能聚酰亚胺纤维及其下游产品研发、生产和销售的高新技术企业,建有全球首套年产30t和100t规模的高强高模聚酰亚胺纤维生产线,其技术来源于北京化工大学。该公司提出的一体化连续反应纺丝工艺,可从聚酰胺酸纺丝溶液经凝固、牵伸、热亚胺化连续反应,获得高强高模聚酰亚胺纤维。该技术突破了高强高模聚酰亚胺纤维制备的瓶颈,具有完全自主知识产权,其中3项核心专利获得美国授权,达到国际领先水平。
PPS纤维
国内聚苯硫醚树脂生产企业主要有浙江新和成、重庆聚狮、内蒙古磐迅和珠海长先。
2020年10月,国家商务部出台政策,对美国、日本、韩国以及马来西亚四国进口的PPS,实施保证金形式的反倾销措施,显著提高进口产品价格,促使国内企业产品性价比提升,为我国PPS树脂产业的快速发展提供基础。浙江新和成、重庆聚狮产量分别占全球产量的9.6%和6.4%,未来有望扩产成为全球PPS产能前五的企业。但由于PPS纤维产业应用领域未完全开发,需求量远低于PPS树脂在电子电气领域的应用。因此,重庆聚狮公司主要集中于PPS注塑原料的研究,纤维级切片产品研究较少,产品单一。
目前,仅有浙江新和成建有5kt/a产能的纤维级树脂生产线,生产多种批号的熔喷级、短纤级切片,但其缺乏长丝级和改性级纺丝切片,纤维产品质量低于国际水平。国内也仅有浙江新和成和四川安费尔高分子材料科技有限公司能实现PPS短纤维的连续生产,产能分别为5kt/a和3kt/a ;江苏瑞泰科技有限公司、四川德阳科技股份有限公司等短纤维生产企业因各种原因相继停产停业。2016年,苏州金泉新材料股份有限公司与东华大学联合承担了江苏省科技成果转化项目,实现了PPS短纤维的改性研究,并建成3kt/a的柔性生产线,显著提高PPS纤维的阻燃性、服役温度和寿命,提高PPS短纤维在国际市场的竞争力,但因纤维级树脂原料短缺,无法持续生产。综上所述,国内PPS树脂的聚合生产技术已经具有一定的积累,在国家政策和市场需求双重支持下,产业规模逐渐扩大,市场占有率大幅提高,但仍存在生产技术水平较低、产品品类较少、缺乏长丝级和熔喷级产品、高端产品低于国际先进水平等问题;在纤维产业方面,高端纤维级切片产能不足,市场应用领域狭窄,中低端产品市场竞争环境恶劣,高端应用市场严重缺乏。高温烟尘滤袋领域虽然仍存在50%以上的市场空缺,但随着静电除尘技术的优化升级和新型高性能纤维的市场冲击,PPS纤维市场饱和,急需拓展应用领域。产业集群方面,基于市场竞争激烈化和纤维生产工艺难度大,常规产品价格竞争激烈,利润低,准入门槛高,多数中小企业被迫转型发展,难以实现产业集群效应,国内PPS高质量发展提速缓慢。
聚芳酯纤维
国内聚芳酯纤维规模化生产企业仅有宁波海格拉新材料科技有限公司,通过与东华大学合作,引入聚芳酯纤维纺丝技术,目前已经实现高性能聚芳酯纤维年产50——100t产量规模,所生产的聚芳酯纤维强度大于22cN/dtex,模量大于500cN/dtex,极限氧气指数为28%,干湿强度比为100%,长期使用温度大于150℃,主要供应给下游高性能织物织造等领域的企业。公司计划在“十四五”期间进一步扩大产能至100——200t/a,以满足国内市场在高强线缆、飞艇蒙皮等领域对于聚芳酯纤维日益提升的需求。
PBO纤维
国内对PBO纤维的研究起步较晚,20世纪80年代,华东理工大学率先开始了对PBO单体及聚合物的研究,所制备纤维的拉伸强度仅为1.20GPa,模量为10GPa,性能远未达到Kevlar纤维水平。
由于合成PBO的单体4,6-二氨基间苯二酚盐酸盐(DAR)完全依赖进口,价格昂贵,制约了PBO相关的研究,对PBO纤维的研究也几度被中断。为填补这一空白,国家将PBO高性能纤维作为重点材料列入863国家计划给予支持。在此背景之下,华东理工大学、上海交通大学、哈尔滨工业大学等对DAR单体的合成进行专门研究;哈尔滨工业大学、华东理工大学、东华大学等单位则对PBO聚合及纤维制备开展了研究,另有多家研究机构对PBO的应用及增强材料进行了研究。
经过二三十年的发展,国内高校及研究所在PBO聚合物的合成和纺丝方面取得了一定的进展。东华大学联合上海交通大学自1999年起开始进行PBO聚合、纤维成形的研究,先后攻克了单体合成及纯化技术,设计制造了适用于高黏度聚合体系的特殊搅拌器,发明了PBO的反应挤出-液晶纺丝一体化工艺,在国内首次成功建成了吨级规模的PBO纤维试验线,2005年完成了项目鉴定,制得的PBO聚合物特性黏数达25dL/g以上,强度达4.16GPa,模量达139GPa;之后,继续进行扩大试验,在原有规模上完善和扩产,建成了5t规模PBO聚合、纺丝中试线,于2008年完成项目鉴定,制得的PBO纤维强度稳定在4.95GPa以上,接近日本东洋纺纤维产品水平。2016年左右哈尔滨工业大学以三氯苯为原料合成的DAR单体纯度达到99.5%以上,采用该单体进行PBO的聚合及纺丝,所纺制的PBO纤维拉伸强度达到5.0GPa、模量达 240GPa。
在PBO纤维产业化方面,国内近几年也取得了重要进展,数家PBO纤维生产企业陆续投产。中蓝晨光化工有限公司“十二五”期间建成一条2t/a产能的PBO纤维军工小试线,其纤维强度稳定达到5.2GPa以上,并正在将其扩建到20t/a的产能。2018年1月,成都新晨新材料科技有限公司投资约5亿元建设产量达380t/a的高性能PBO纤维生产线,是目前国内产能最大的生产线;2018年8月,江苏中汇特纤新材料公司高性能PBO特种纤维项目试产成功,项目一期具备50t/a的产能;同年,中科金绮新材料科技有限公司投资1.45亿,建成150t/a的PBO生产线。近年来,山东非金属材料研究所因军工需求与东华大学联合推进PBO纤维的产业化建设,2021年在山东济南建成了百吨规模的PBO纤维生产线。综合来看,国内尚处于PBO纤维产业化的初期阶段,市场上产品较少,尚待进一步发展。
碳化硅纤维
为打破美国、日本等发达国家对SiC纤维技术和产品的严密封锁,国防科技大学从1980年开始在国内率先开展了制备连续SiC纤维的研究,独立研发并建立了国内第一条连续SiC纤维的生产试验线,在先驱体合成、纺丝、不熔化和烧成等方面均取得了具有自主知识产权的产品和技术。
所制备的KD型第一代和第二代连续SiC纤维的性能均处于国内领先、国际先进水平,已被国内航空、航天等领域多个研究单位和应用部门所使用,先后获得军队科技进步一等奖(2014年)、湖南省技术发明一等奖(2014年)、国家科技进步二等奖(2015年)。针对第三代SiC纤维的研制,通过加氢脱碳预烧,制备出近化学计量比的KD-S型第三代连续SiC纤维,性能与同样采用加氢脱碳工艺的日本Hi-Nicalon S纤维水平相当;2016年攻克了SiC纤维高温烧结致密化技术,在国内首次成功制备出高结晶近化学计量比的连续SiC纤维,即KD-SA型第三代SiC纤维,该纤维在组成与结构、耐高温和抗蠕变等性能方面与国外的第三代SiC纤维Tyranno SA水平相当。目前该纤维已经实现了小批量生产并提供给应用部门使用,填补了国内空白,使我国成为世界上第三个能够制备出高结晶近化学计量比连续SiC纤维的国家。
厦门大学从2002年开始进入了制备连续SiC纤维的研究领域,采用电子束辐照交联的方法获得了低氧含量的第二代连续SiC纤维,并采用电子束辐照后再加氢脱碳的方法制备了类似于日本Hi-Nicalon S纤维的第三代连续SiC纤维,纤维的组成、结构与性能都与日本相应的第二代、第三代连续SiC纤维水平相当。自2015年以来,中科院宁波材料所针对核工业领域的应用需求,开展类似于日本Hi-Nicalon S纤维的第三代SiC纤维的研制。另外,中科院过程所对含锆的复相SiC纤维、中南大学对含铍SiC纤维也都进行了相关研究。
在产业化方面,2005年,苏州赛菲集团有限公司与国防科技大学对接成果转化,并于2010年在国内首次实现连续SiC纤维的产业化。2016年,宁波众兴新材料有限公司与国防科技大学签署合作协议,开展第二代连续SiC纤维的产业化,目前已建成产能40t/a的聚碳硅烷先驱体生产线以及10t/a的第二代连续SiC纤维生产线(Shincolon-Ⅱ)。2019年该公司与中科院过程所签署合作协议,转化第二代连续复相SiC纤维(Sericafila Z)以及第三代连续复相SiC纤维(Sericafila ZB)。福建立亚新材有限公司自2015年成立以来与厦门大学合作,建成了产能10t/a的第二代SiC纤维、第三代SiC纤维产业化生产线。2018年,湖南博翔新材料有限公司碳化硅纤维事业部(现湖南泽睿新材料有限公司)通过中南大学的科技成果转化建成具有自主知识产权的产能 10t/a 的含铍碳化硅纤维生产线。
玄武岩纤维
2002年,科技部将“玄武岩连续纤维及其复合材料”列入“863计划”,加强对具有自主知识产权的气电混熔和全电熔炉生产技术的发展及推广,使得玄武岩纤维得到快速发展。
但目前我国的玄武岩纤维总体走的是低端路线,集中在混凝土用短切玄武岩纤维的增强材料。2006年,我国第一条玄武岩纤维生产线由上海俄金玄武岩纤维有限公司开发。
目前,我国约有十多家企业从事玄武岩纤维的生产,总产能达到100kt以上,多家企业具有万吨级生产线,包括吉林通鑫、河南登封电厂集团、四川玻纤集团、四川谦宜、贵州石鑫等,但是多数企业的实际产量在数百到数千吨。我国玄武岩纤维的实际总产量为20——30kt,规格多在10——20μm之间,每吨价格在1.2万——2万元,主要应用在水泥混凝土、沥青混凝土、车辆交通、高温滤袋及保温毡等方面。
国内玄武岩纤维生产企业目前仍然处于低价同质化竞争阶 段,对如何提高玄武岩纤维性能,仍需要进一步探索。1200孔及以上大丝束拉丝技术仍不稳定,需要从原料、熔化及成纤工艺等多方面出发攻克技术难题。只有解决了大丝束拉丝技术,才能提高玄武岩纤维的质量稳定性,真正发挥玄武岩纤维高强度、高模量等特点,拓宽其应用范围,突破玄武岩纤维发展的瓶颈。表9总结了我国玄武岩纤维主要的生产企业的生产情况及特点。
表9 我国玄武岩纤维主要生产企业的生产情况及特点
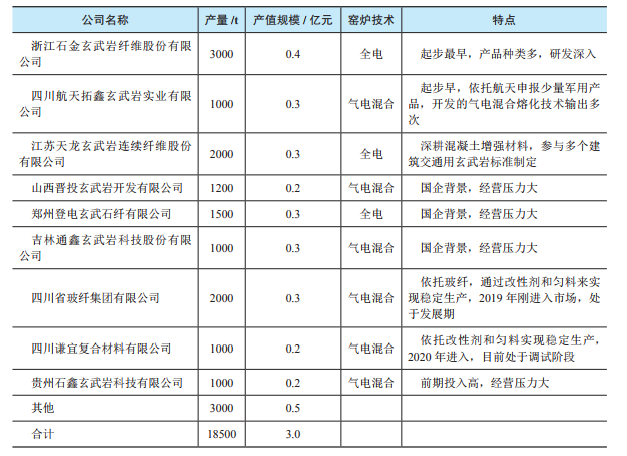
04 发展我国高性能纤维产业的主要任务及存在主要问题
我国高性能纤维研制起步并不晚,但由于经费投入、原材料、装备、人才等复杂的原因进展一直较缓慢,近10年来虽取得了很大的进步,但在产品性能稳定性、生产成本、规模及应用水平方面与日本、美国等发达国家仍有明显差距,其主要共性科学问题是高性能纤维近程、远程和宏观结构(即分子链分布、体系纯度、凝聚态结构、纤维表面结构)的不均匀性引起的产品可纺性、物化性能和批次稳定性不足。目前主要存在的主要问题总结如下:
高端纤维仍存在代差,自主保障能力亟待加强。国外航空航天领域已经大规模应用以T800级碳纤维为主要增强体的第二代先进复合材料,而我国总体上仍处在第一代先进复合材料的扩大应用、第二代先进复合材料的考核验证阶段。高强高模、超高模量碳纤维、差异化对位芳纶(超高强型、超高模型、中等模量型、高黏结型、抗疲劳型等)、高强和无蠕变UHMWPE纤维、高性能杂环芳纶Ⅲ生产技术尚未突破,不具备自主保障能力,在高性能无机纤维等领域,同样存在高端产品缺乏、质量一致性差等问题。
高性能纤维产业技术成熟度不够,大规模高端装备与成套工艺仍未完全突破。高性能纤维产业是一个生产工艺与装备高度耦合的长流程精细产业,国内尚未完全掌握大规模成套生产工艺技术。现阶段国产碳纤维生产仍以12K及以下小丝束产品为主,大丝束、低成本碳纤维工业化生产技术尚未全面突破,而国外已开始将大丝束低成本与小丝束高质量的生产技术融合,不断提升产品质量和降低生产成本。芳纶(对位芳纶、间位芳纶、杂环芳纶Ⅲ)在产品性能与稳定性、生产效率、产业规模、应用领域等方面还存在差距。UHMWPE纤维单线产能低,投资成本高、生产效率低、能耗高,规模化低成本生产还难以实现。PPS纤维和聚芳酯纤维缺乏千吨级产业化成套技术和装备。此外,高性能纤维的产业化成套装备设计与制造能力不足,缺乏设计/仿真模拟工程师,设计/模拟软件依赖进口,基础工业技术(如机 械加工)、精密设备(如计量泵、喷丝板)、装备原材料质量(如高强度钢、耐腐蚀钢材料等) 与国外存在明显差距,导致国内自主装备在精度、效率和使用寿命上不足,设备运行稳定性差、故障率高,制约我国高性能纤维产品性能稳定与提升以及生产成本控制。
基础研究投入不足,部分关键科学问题尚未探明,缺乏前沿产品创新开发动力。在国家政策扶持和重大任务的牵引下,我国高性能纤维参照、仿制国外产品开展研究工作,以产品研制为主,着重解决国家重大需求和应用急需。高校与研究机构研发通常以型号产品为依托,高性能纤维材料成分-结构-工艺-性能之间的深层次关系规律尚未全面掌握,必要的基础科学机理与理论尚未揭示清楚,导致面临新的应用需求时缺乏理论支撑,自主创新能力不足。企业疲于盲目扩产,投入研发经费严重不足,如碳纤维目前国内可工业化的产品仅有几个牌号,而日本东丽有近20个产品型号。
健全的产业体系尚未形成,仍存在低水平重复、无序竞争现象。目前我国高性能纤维产业体系尚不完整,关键装备与配套材料、重要原材料、产品标准和检测评价环节薄弱。在航空航天、国防军工等领域应用的总体规模较小,难以驱动高性能纤维及复合材料全产业链的发展与完善,在以汽车、压力容器、轨道交通等为代表的工业领域仍未实现大规模应用。在国家政策支持和高科技领域投资冲动等多重因素刺激下,目前仍存在低水平重复、脱离产业实际的投资乱象,项目水平参差不齐,不仅造成大量国家和社会资源占用与浪费,同时不利于行业竞争力和可持续产业生态的形成。
针对以上问题,我国高性能纤维产业发展和升级目前面临的主要任务列举如下:
碳纤维
突破高强中模、高强高模、高强高模高延伸碳纤维工程化制备关键技术,实现高强中模碳纤维拉伸强度≥7GPa ;高强高模碳纤维拉伸模量≥650GPa ;高强高模高延伸碳纤维拉伸强度≥5.7GPa,拉伸模量≥370GPa,断裂延伸率≥1.5%,满足高端装备用碳纤维及其复合材料自主保障需求;研究生物基碳纤维氧化、碳化过程结构转化机制,突破生物质基碳纤维连续制备关键技术;突破碳纤维用纺丝油剂和上浆剂等配套材料,突破新型纺丝、预氧化碳化等颠覆性制备技术,实现国产碳纤维稳定化与低成本化,支撑国产碳纤维的规模应用。
有机高性能纤维
突破芳纶、差别化聚酰亚胺和UHMWPE、聚芳酯纤维、PPS纤维等高性能有机纤维产业化制备关键技术,实现在国家重大装备上的稳定应用。开发系列化、功能性对位芳纶,满足差异化应用领域需求,集中提高产业链规模,形成规模效益,提升国际竞争力;突破提升间位芳纶生产效率的新工艺、新技术,进一步降低产品价格,拓宽应用领域,推进产品升级换代,积极开发间位芳纶差异化产品,满足高端领域应用要求;发展新一代高强高模、高复合性、低成本杂环芳纶;开发耐温、抗蠕变UHMWPE纤维,完善中高强度UHMWPE工程化制备技术,解决生产过程能耗大、成本高问题;优化聚芳酯纤维聚合纺丝工艺,实现稳定高品质产品千吨级生产及成套装备研发;开发高性能PPS纤维技术,提升PPS短纤级切片质量,突破PPS长丝级切片关键制备工艺与集成设备技术,拓展PPS纤维及其复合材料的应用领域;开展高纯度DAR单体制备技术研究,提升产品质量稳定性,提升PBO纤维生产规模,并针对性开发PBO专用成套装备,提升装备在酸性、高黏度、高压力状态下的运行稳定性, 保障PBO生产全流程工艺稳定性。
无机高性能纤维
突破高端玄武岩纤维、碳化硅、氧化铝、硅硼氮等纤维及其前驱体的工程化稳定制备技术,突破大丝束拉丝工艺技术,实现无机高性能纤维批量化应用;形成系列无机高性纤维及其复合材料产品库,实现无机高性能纤维基复合材料在航天发动机等重大装备上的工程应用。
05 推动我国高性能纤维产业发展的对策和建议
高性能纤维是全球化纤工业的主要发展方向,近10年间全球化纤产量以年均3%的速度增长,而高性能纤维则以接近30%的速度增长。同时高性能纤维生产国由少数发达国家扩展到包括中国、土耳其、韩国等在内的十多个国家和地区。但全球高性能纤维的生产仍高度集中在日本、美国、欧洲的少数企业,这些公司大都已处于高性能纤维的规模化发展阶段,他们一方面积极投资以扩大其产品的市场占有率,另一方面在主要产品已经较为成熟且完成系列化生产的前提下,将研发重点转向不断提高核心技术与产品质量和性能上,通过技术储备以进一步拉大与竞争对手的差距,保持其行业垄断地位。目前,高性能纤维正向着制造技术先进化、低成本化、材料高性能化、结构功能一体化和应用扩大化的方向发展。
为推动我国高性能纤维产业进一步发展,提高其国际竞争力,建议:
加强顶层设计,强化政府主导作用。当前面临国际大环境的急速变化,应由国家相关部委和行业协会牵头,谋划我国高性能纤维行业发展新路径,保障行业的稳健发展,防止同质产能增长过快,避免走常规纤维发展的老路,影响行业未来可持续发展。支持科技研发和示范应用,坚持长期投入,鼓励迭代和稳定性发展,推动创新产品的研发和规模化应用,以高性能纤维材料技术进步带动产业升级。
加强研发创新,深化产学研相结合。加大自主创新,注重协同创新,构建以企业为主体、市场为导向、产学研结合的技术创新体系,增强内生动力,推动产业高质量发展。加大力度解决制约行业高质量发展的共性难题,重点关注短板问题,加强高品质原辅料、关键装备和零部件等研发,增强产业链供应链的自主可控能力,掌握高性能纤维成分-结构-工艺-性能之间的深层次关系规律,全面提升自主创新能力。
扩大生产规模,开发低成本工艺技术。在聚焦产品性能和研发高附加值产品的同时,重视开发各种成型工艺技术,进一步降低成本,强化收益能力。生产成本决定了市场容量和应用,加快低成本技术的开发,有利于扩大应用范围。扩大生产规模,提高单线生产能力,可进一步提高生产效率,降低生产成本,从而提升产品的市场竞争力。
针对市场需求,加大应用技术开发。通过“下游”带动“上游”,形成具有自主知识产权的系列化产品,加强与配套产业的沟通合作,从制成品的设计端开始就积极融入下游客户的研发工作中,高效地将高性能纤维的优异性能最大化地体现在应用场景中,真正实现其性能与下游应用的精准匹配。
建立监测体系,把握行业动态。健全高性能纤维产业统计,聚焦行业数据研究,加强行业管理和引导,规划发展,制定和完善行业准入条件,发布产品指导目录,避免盲目发展与低水平重复建设,鼓励推动各生产厂家之间协同联动、深入沟通,引导高性能纤维产业良性发展。
加强标准建设,推动参与国际竞争。聚焦高性能纤维国家标准及行业标准建设,包括碳纤维、芳纶纤维、聚酰亚胺纤维、聚芳酯纤维、聚苯硫醚纤维、UHMWPE纤维等及其各类下游制品的方法标准以及产品标准,以规范国内高性能纤维产品,推动产品进入国际市场、参与国际竞争。
06 面向国家2035年重大战略需求高性能纤维产业技术预判和战略布局
我国已建立起较为完整的国产高性能纤维制备技术研发、工程实践和产业体系,产品质量不断提高,产学研用格局初步形成,有效缓解了国民经济和国防建设对国产高性能纤维的迫切需求。但我国高性能纤维及其复合材料的基础理论研究仍相对薄弱,高端优质产品的产业化开发不足,一些关键科学技术问题尚未完全突破,行业自主创新能力不强,部分品种仍受制于发达国家。面向国家2035年重大战略需求,我国高性能纤维产业技术应进行以下布局:
加强高性能纤维的关键科学技术问题研究。高性能纤维是高度复杂性产品,具有对基础研究依赖性强、生产工艺前后关联度高的特点,高性能纤维的性能源于其独特的微观结构,要在生产中确保其微观结构得以实现,就需要对其形成过程有非常清楚的认识,对影响其形成的外部条件有精准的控制。因此,对相关共性基础科学问题的深入研究是解决发展过程遇到的问题、建立具有自主知识产权的生产体系和实现工业化稳定生产的关键。但目前国内企业缺乏对相关基础科学问题的正确理解与清晰认识,需要加大力度凝练共性科学问题,布局前瞻研究,研发具有稳定性能的优质高性能纤维。
高性能纤维的产业化关键技术与成套装备开发的系统集成。高性能纤维产业技术难度高、专业跨度大,是复杂的系统工程和高度的集成创新,具有对设备质量和控制精度要求高、对生产管理要求严格等工程技术特性。需加强多学科、多专业的相互交融和前后衔接,加快高性能纤维及其复合材料高附加值、低成本关键工艺及装备工程化研究,包括有机高性能纤维级专用树脂的研发与产业化,新型溶剂、助剂、萃取剂等的开发,新型纺丝及后处理等连续化工程成套技术及关键设备开发等,提升高水平产业化的系统集成、项目管理和过程融合。
高性能纤维性能、品质提升以及品种系列化、功能化研发。全球主要高性能纤维已经进入技术和工艺全面更新的阶段,生产效率不断提高,成本不断下降,新产品个性化明显,要完善和系列化生产各种型号规格的产品,重点拓展新品种和应用领域。一方面突破国外垄断高端产品的产业化,另一方面通过降低纤维制造成本,来提高产品的市场竞争力和扩大纤维的应用领域。加强高性能纤维产品多领域市场应用开发,携同下游复合材料企业大力发展协同设计、制造、服务,通过下游稳定应用支撑上游行业发展,拓展整体产业上下游产业链的宽度和深度。
从原料到纤维的对应标准和评价体系。瞄准国际先进水平,立足自主技术,健全高性能纤维新材料标准体系、技术规范、检测方法和认证机制。加快制定产品全产业链标准,鼓励产学研用联合开发重要技术标准,积极参与国际标准制定,加快国外先进标准向国内标准的转化。
加强高性能纤维配套的复合材料技术研究。高性能纤维及其复合材料不仅事关国家战略安全,与国防军工、航空航天建设紧密相关,更是践行国家“双碳”战略的重要基础性材料产业,是风电、光伏、交通工具轻量化、氢能源汽车等发展的重要支撑。需要加强高性能纤维配套的设备及复合材料技术研究,开发高效织造、复合材料高效成型等新技术,构筑三维纺织结构和复合材料表界面结构,牵引高性能纤维材料产业发展和升级。