该演示件采用特殊材料制成(LM_PAEK),不易损坏,比铝制组件轻约一吨。此外,该演示件还使用了全新的生产和装配技术,实现了具有成本效益、资源节约的生产流程,最大限度减少了能源消耗。
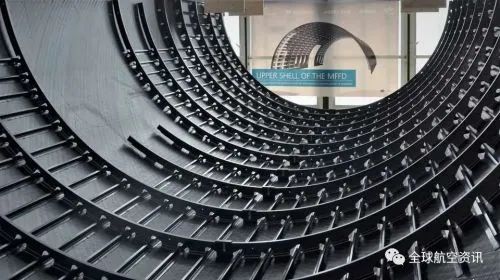
MFFD多功能机身演示器
该演示件的机身半壳(飞机机身的上半部分)在奥格斯堡的DLR制造,目的是研究使用的材料并展示必要的技术。该演示件长约8米,是作为欧洲洁净天空2研究计划大型客机计划的一部分而开发的,目标是将飞机机身重量减少10%,运营成本降低20%,以达到每月60-100架飞机的生产效率。2023年7月18日,MFFD项目合作伙伴成功完成半壳交付。
热塑性碳纤维复合材料(CFRP)具有特殊性能,在一定温度范围内重新加热时可以重塑形状,这意味着部件可以更有效地进行修复和回收。热塑性CFRP上壳的设计由Premium AEROTEC公司主导完成。自动化生产和机器人工具主要是由DLR轻量化生产技术中心(ZLP)开发,目前研究人员已经掌握了三项基本技术——激光原位光纤放置、连续超声波焊接和电阻焊接。
激光、超声波和电阻焊接
为了生产飞机外壳,DLR团队使用了一个倒挂的机器人,使用激光精确加热材料条并将其分层,形成复合材料层压板。由于材料浪费极少,因此该系统材料利用率极高。这在平衡成本方面非常重要,因为CFRP的成本比铝高得多。此外,由于不需要在热压釜中固化,该系统将生产时间缩短了40%,从而进一步降低了成本。
在下一个生产步骤中,外蒙皮必须安装纵向加强筋,而且44个纵梁不是铆接的,而是通过超声波焊接到部件上的,这在世界上尚属首创。为此,ZLP团队让机器人沿着纵梁移动,并进行高精度自动路径校正。这种方法比传统的机械过程要快得多,而且与后续的连接技术一样,具有不产生切屑或灰尘的优点,因此无需在最终组装之前将机身外壳连接在一起。
DLR团队开发的第三项技术涉及横向加强筋的安装。该技术使用电流对肋条进行加热,并使用专门工具进行电阻焊接,可提供极高的焊接强度。与铝合金相比,热塑性CFRP减少了生产时间,降低了制造成本,而且由于没有孔洞,可使飞机蒙皮保持完整且无灰尘。
奥格斯堡团队改进了电阻焊接工艺,将纵向加强筋连接到横梁上。由于这项工作非常细致并且在极其狭窄的条件下进行,研究团队将标准机器人与小型轻型机器人结合起来,这种灵活控制的“协作机器人”能够自动与框架和纵梁对齐,并快速准确地焊接数十个连接元件。
计划和潜力
通过MFFD,DLR成功生产了世界上最大的由纤维增强热塑性复合材料制成的飞机部件。该项目开发的技术成熟度显著提高,且碳足迹非常大幅降低。因此,DLR为气候友好型飞行做出了重大贡献。正如当前项目所示,ZLP团队已为开发下一代飞机铺平了道路。该技术提高了地区、国家和欧洲层面的竞争力。
自6月中旬以来,机身半壳运抵项目合作伙Premium AEROTEC公司,并在其奥格斯堡工厂完成了门框的精加工和安装工作。成功交付后,该部件目前正被运送位于施塔德的弗劳恩霍夫制造技术和先进材料研究所(IFAM),在那里它将与来自荷兰的机身下壳体(STUNNING项目)连接起来,在今年年底前形成完整的机身外壳部分。随后,空客公司将在汉堡应用航空研究中心(ZAL)对这些技术进行最终验证。