2.4由于轮毂内作业空间狭小,变桨油缸重量大,更换油缸密封或者油缸工作量大,返工率高,将造成巨大的电量损失。
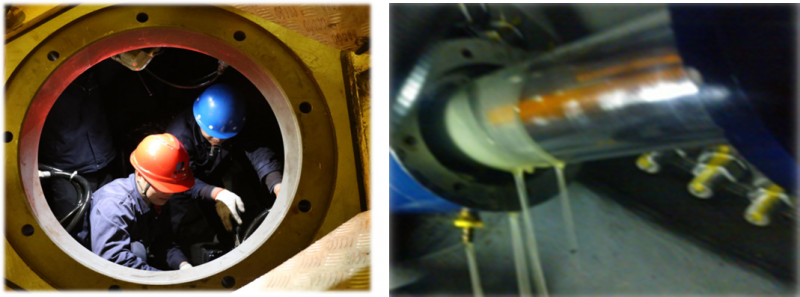
图4:轮毂作业空间狭小、更换工艺差
3. 项目解决方案及改造过程
3.1 油缸密封结构及材料改进
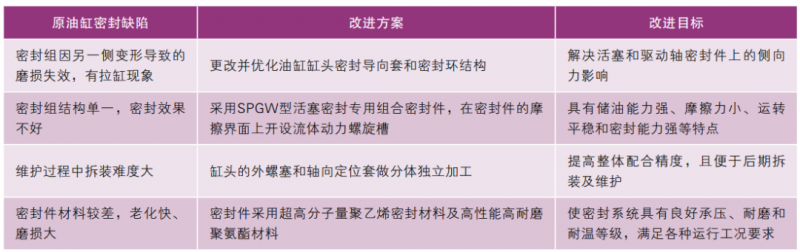
油缸密封结构改进前后见下图:
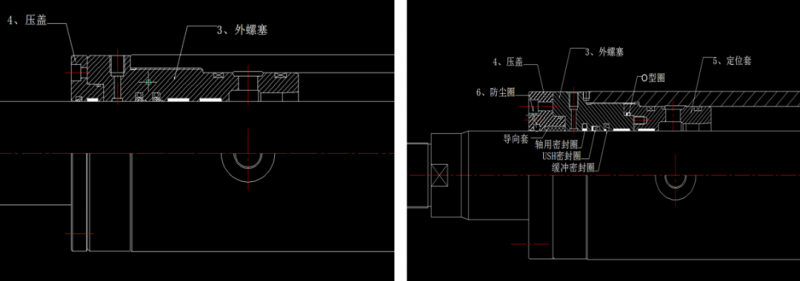
图5:油缸密封结构改进前、后对比
3.2 油缸密封更换工艺改进
更换油缸密封,由原来的风机上、轮毂内更换,改进为拆卸油缸返厂解体检修。改进后有以下优点:第一,厂内作业区大,辅助设备多,人员可借助专用工具进行操作,工作量低,操作简单;第二,可保证缸体竖直进行拆装从而减小更换过程中密封件损伤,同时便于缸头细牙螺纹安装,避免返工;第三,返厂能将解体油缸、密封更换、尺寸优化及修后专业检测等工作一并在厂内进行处理,并出具相应专业检测报告,发至现场直接安装即可。
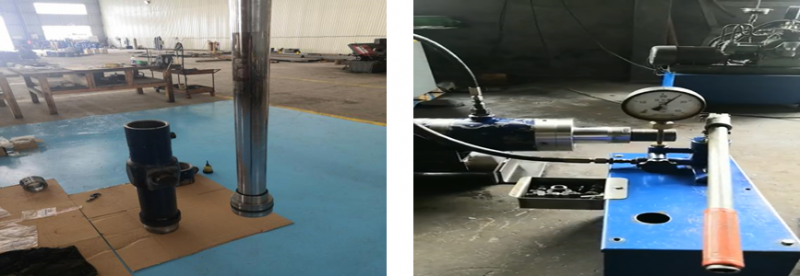
图6:油缸返厂检修过程
3.3 变桨油缸机械回转支撑结构改进
3.3.1 变桨油缸十字轴钢轴套、半月板及滑动轴承更换。
由于半月板及内部钢质滑动轴承与变桨油缸十字轴轴套之间为直接金属摩擦接触,无任何润滑,存在严重的设计缺陷。改进后,第一,定制高强度变桨油缸十字轴钢轴套进行更换;第二,新型半月板轴孔内有预加工的导脂槽便于润滑油脂的注入及对滑动轴承的润滑;第三,将原钢质滑动轴承更换为复合特氟龙材料的滑动轴承,有效规避了半月板、轴承和油缸十字轴间的硬磨损问题,能更好的保证三者间的配合间隙;第四,半月板配套减震垫,对变桨油缸十字轴向的位移能起到减震作用。
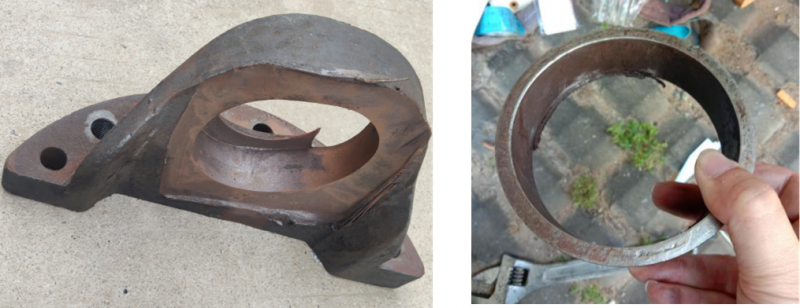
图7:改进前回转支撑结构为硬质摩擦,磨损量大
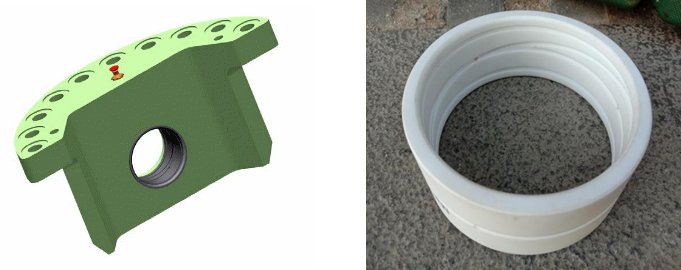
图8:改进后采用新型带润滑结构的半月板以及特氟龙轴承
3.3.2 调整油缸十字轴两侧限位端面与半月板间隙。