由于油缸十字轴限位端面与半月板间磨损严重,间隙较大,半月板及轴套更换后需使用不锈钢调整垫片填充间隙,避免油缸十字轴运行中在轴套内滑动,从而保证变桨油缸装配后工作位置精度。
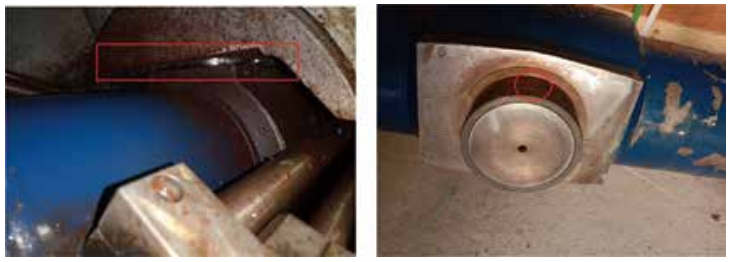
图9:改进前油缸十字轴限位端面与半月板存在间隙
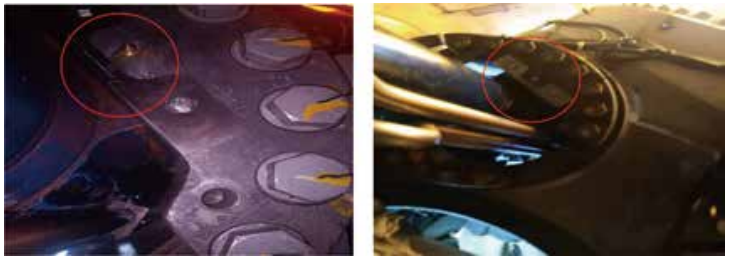
图10:改进后油缸十字轴限位端面与半月板使用垫片调整间隙
3.3.3 改进变桨油缸活塞杆护套。
原护套材料为丁基橡胶布,被液压油及水浸泡后易老化变硬,最终随着活塞杆反复运动被撕裂,现改进为防水防油的优质弹道尼龙材质的油缸活塞杆伸缩护套,更加柔顺、耐磨,较目前现场使用护套寿命至少提高2倍,能有效地避免划伤油缸活塞杆,提高油缸密封性。
3.4 其他改进措施
除变桨油缸本体及支撑结构的改进以外,还对以下几方面进行改进:
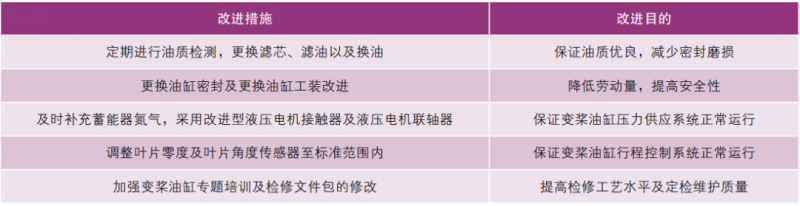
4 .改造效果
经过近一年的改造及持续跟踪观察,风机油缸漏油情况明显好转,最早一根采用上述应用的油缸更换到#34风机A桨的时间为2019年10月28日,截至2021年1月15日,未发现漏油情况,其后陆续更换过的油缸也未发现漏油情况,全场风机液压故障大幅度降低,已基本实现预定目标。
按照单台风机平均故障处理时间4小时计算,平均降低单台风机液压故障12台次,以及一支变桨油缸更换节约时间4天计算(生产管理系统中统计得出),2020年全年单台风机平均降低4×3×24+4×12=336小时故障处理及检修技改时间,按照全场24台风机计算,减少电量损失为:2000kw×336×0.61元/kW·h(度电价格)×24台×0.45(容量系数)=442.71万元,节约人工成本336小时/24小时×500元/天×24台=16.8万元。
成本测算:1、变桨油缸返厂检修,单支大概1.2万元;2、油缸返修后安装,单支大概0.8万元;3、特氟龙轴承、活塞杆护套、半月板等备件,单台大概0.4万元,全场24台歌美飒风机总投入大约158万元左右。
投入与产出:按全场总投入大约158万元左右,减少电量损失442.71万元以及节约人工成本16.8万元计算,即可创造直接经济效益442.71+16.8-158 =301.51万元。
5. 总结
5.1 该改造项目集油缸本体及支撑结构、密封材料、检修工艺、检修工装、油缸配套附件、液压油品质、油缸控制及检修维护管理于一身,全方位综合治理该油缸漏油问题,虽然花费成本较高,但是效果明显,具有极高的市场推广价值,值得在类似高风速风场的液压变桨风机或者同款油缸的漏油处理及日常维护定检工作中推广。
5.2 课题组将以目前的工作成果为起点继续优化改进变桨油缸设备检修工艺,特别是加强变桨油缸各执行元件、控制元件、反馈元件的检修维护技术突破以及如何降低液压油温等技术难点,将作为下一步工作的重点进行开展,并进一步提高变桨油缸运行可靠性,降低漏油率。
参考文献:
[1]陈云程.风力机设计与应用[M].上海:上海科学技术出版社,1990.
[2]贾福强,高英杰,杨育林,等.风力发电中液压系统的应用概述[J].液压气动与密封,2010(8):13-14.
[3]顾鑫兆.《瓦级风力发电机组液压变桨系统研究》.江南大学硕士毕业论文,2008.
作者:华电福新发展有限公司福清分公司 李明