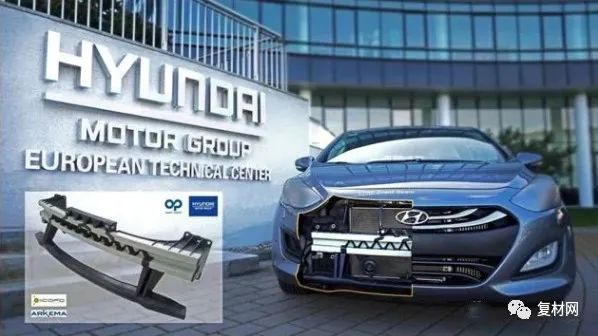
图1 搭载纤维增强热塑性复合材料前组合防撞梁的现代i30
现代汽车欧洲技术中心(HMETC)开发了一款纤维增强反应性热塑性树脂复合材料前保险杠梁。该保险杠梁由纤维增强反应性热塑性树脂拉挤和热塑性树脂嵌件注塑成型,包括由单向玻璃纤维预浸带、玻璃纤维织物、碳纤维和反应性树脂组成。该项目获得2015年AVK增强塑料类创新奖,也是第一个采用反应性热塑性拉挤成型工艺制造热塑性前防撞梁。
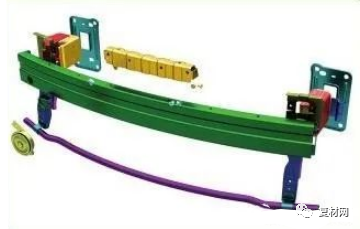
图2 钢制前防撞梁爆炸图
在九个多月的研发周期里,HMETC的工程师根据与汽车相关的原材料供应商以及知名学术人士的大量讨论,彻底研究了最新的复合材料和制造方法。起初,团队在现有的“工具箱”中找不到任何可以满足现代汽车在重量、性能和成本方面的高期望解决方案。例如仅使用碳纤维复合材料可以明显减轻重量,但材料成本与量产条件不符合要求。另一方面,现有i30前保险杠梁结构已经有8.7KG,且全部由高强度和超高强度钢组成,显然现有钢部件的设计优化无法带来巨大的减重空间。无论如何优化,一个2.1米长的钢制前防撞梁制作工艺包括了26个不同的部件、24条激光焊接线和85条电弧焊线,其生产和组装过程相当复杂的。
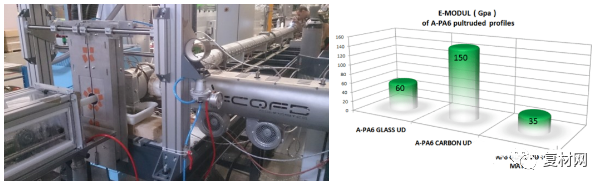
图3 CQFD反应性热塑性塑料拉挤成型设备(左)及其生产的连续纤维增强热塑性复合材料产品可达到的性能(右)
随着传统解决方案的排除,现代工程师不得不跳出“舒适区”思考以实现项目目标。由于与其强度和性能相比成本相对较低,因此很快就考虑使用先进的复合材料,并且该领域也具有很大的创新空间。在研究了不同的先进复合材料和工艺之后,反应性热塑性塑料拉挤成型提供了很好的解决方案。这是由法国拉挤成型设备制造商CQFD Composites开发的一种可连续制造具有恒定横截面的复合材料零件的工艺。玻璃纤维或碳纤维由熔融态热塑性树脂单体浸渍并牵引进入拉挤模具中。然后在成型过程中通过加热使单体聚合,这样纤维和塑料就可以在一个过程中结合——“液态模内反应聚合”。通过拉挤工艺生产出横梁半成品,随后以嵌件的形式放入注塑模具中,以完成前保险杠横梁所有结构成型。这种技术不仅显着减轻了重量,而且大大降低了工艺复杂性。因此,新结构仅包含三个主要部件,在两个连续的生产步骤中生产和组装。
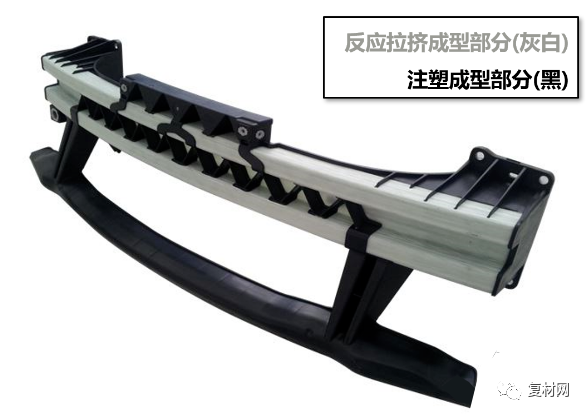
图4 Hyundai纤维增强热塑性复合材料前组合防撞梁
前保险杠梁使用碳纤维和玻璃纤维增强热塑性复合材料后重量显着减轻,与钢制材料相比,使用碳纤维和玻璃纤维增强复合材料可减轻3.6KG的重量,减重达到43%,在其中前保险杠梁结构中使用的玻璃纤维增强热塑性复合材料就可减轻3.4KG。此研发项目其更实惠的成本和快速的生产效率也确保了该保险杠梁可以应用于大批量生产。该复合材料前保险杠梁经过了车辆性能验证,例如低速保险测试、行人保护测试、EuronCAP 50和64 km/h碰撞测试。此外,新结构还包括一个牵引钩,该牵引钩也完全符合所有现代内部负载测试。