表1 复合材料应用历程
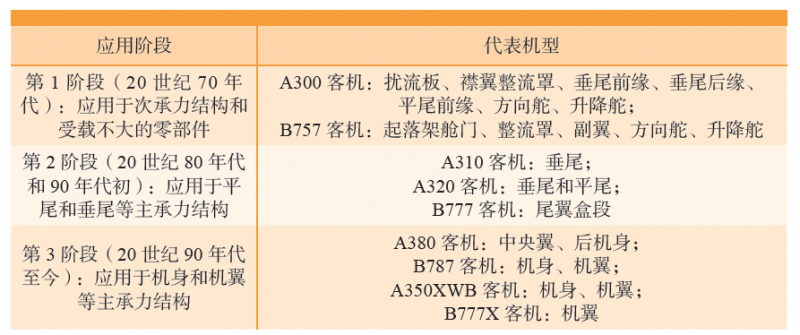
我国民机复合材料结构应用技术的研究起步较晚,但在复合材料结构设计、制造工艺方面也进行了探索和实践。“十五”至“十二五”期间,开展了“民机复合材料次承力结构设计技术研究”、“民机全尺寸复合材料尾翼与舵面设计和分析及制造与试验验证”、“民机复合材料机身与中央翼基础与关键技术”、“民机复合材料机头基础及关键技术”和“大型客机复合材料机翼设计制造与验证技术研究项目”等民机预研课题的研究。“十三五”规划出台后,以复合材料为代表的新材料技术被列入国家发展战略。在“十四五”规划中,创新和关键核心技术自主可控被提升到新的高度,先进复合材料的国产化势在必行,大尺寸复合材料主承力结构件的技术攻关也被摆到了突出位置。
波音公司
波音公司在民机主承力结构上应用复合材料的尝试始于B777 客机的尾翼,随后在B787 客机上实现了跨越式发展,将应用范围扩大至机翼和机身,最新的B777X 机翼则集成了目前世界上最先进的复合材料制造、装配和检测技术。
1 B787 客机
波音公司787 项目于2004 年4月启动,B787 客机于2009 年12 月首飞,2011 年9 月首架交付。B787客机是世界上第一款将复合材料应用于机翼和机身主承力结构的大型民机,复合材料单机用量约25t,占全机结构重量的50% 左右。日本东丽公司为B787 客机研发了第三代增韧环氧复合材料T800S/3900–2B,属于经改进的大丝束碳纤维,该材料的冲击后压缩强度值(Compression after impact, CAI)达到了315~345MPa。
B787 客机的机翼展长约60m,由日本三菱重工委托日本新明和工业株式会社研制。机翼壁板为整体的I 型加筋壁板,采用“湿蒙皮+ 干长桁”的共胶接工艺,蒙皮采用预浸料自动铺带(Automated tape laying, ATL)工艺制造。机翼前、后梁长度均约为28m,分别由3 段组成,由人工在阳模上铺贴、热压罐固化成型,如图1 所示。B787 客机的机身由6 段筒体组成,每段机身筒体采用纤维自动铺放(Automated fiber placement, AFP)工艺制造,如图2 所示,纵向桁条为帽形闭合剖面,与机身蒙皮共固化整体成型,隔框为“C”形剖面框(图3)。该机身筒体制造方案减少了约1500个零件和40000~50000 个紧固件。
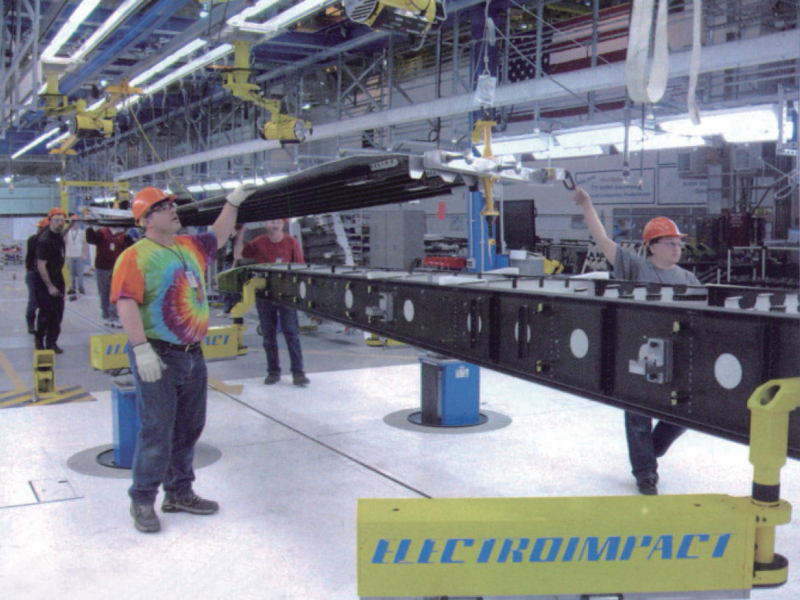
图1 B787 翼盒装配
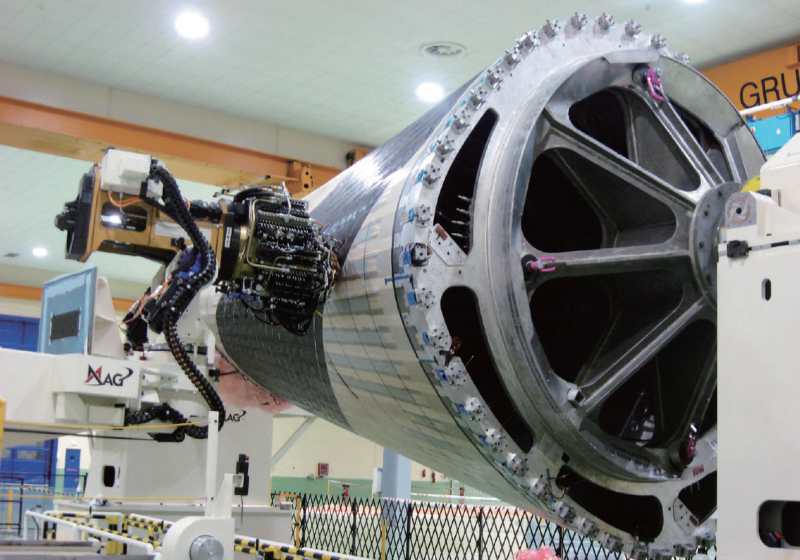
图片
图2 B787 客机机身蒙皮的AFP 工艺
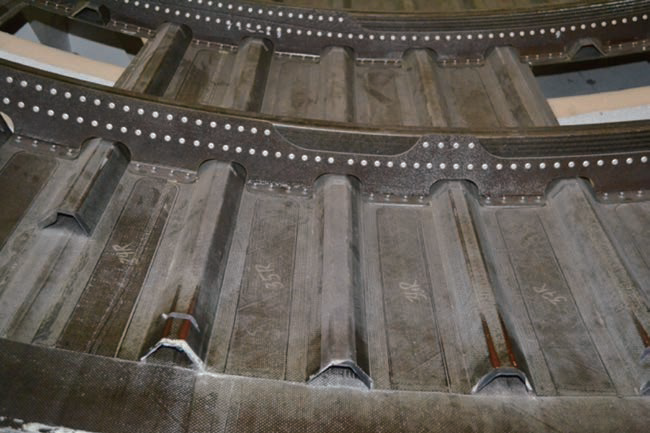
图3 B787 客机机身壁板
2 B777X 客机
B777X 客机于2020 年1 月25日首飞。客机采用全复合材料机翼,翼展达到了71.8m,是目前世界上最大的复合材料机翼结构,其代表了当今最先进的复合材料技术水平,使得大型复合材料结构件的制造与装配向着全自动化迈进了一大步。
B777X 机翼蒙皮、长桁和翼梁均采用了AFP 工艺,长达32m 的翼梁不分段整体铺贴成型,大幅减少了零件数量和装配工作量。B777X 机翼壁板和翼梁的制造使用了两套创新的龙门式高速AFP设备。
(1)壁板AFP 设备。12.8m 的主龙门梁上装有20 个盘型卷轴的AFP铺丝头,其重量达1.7t,龙门可以沿着机翼壁板模具移动超过30m,铺丝头可以跨越龙门移动7.5m,能覆盖最宽处达9m 的模具。机翼壁板在置于工作区域内的低曲率阳模中制造,铺丝头在其上做往复运动,20 个卷轴同时输送38mm 宽的预浸带,即一次可铺放760mm 宽的预浸带。
(2)翼梁AFP 设备。装有16 个丝轴的铺丝头,其重量达0.5t,可将12.7mm 的预浸带铺放在“U”形模具上(图4)。该系统最快可在10min 内完成超过30m 长的一层预浸带铺放。
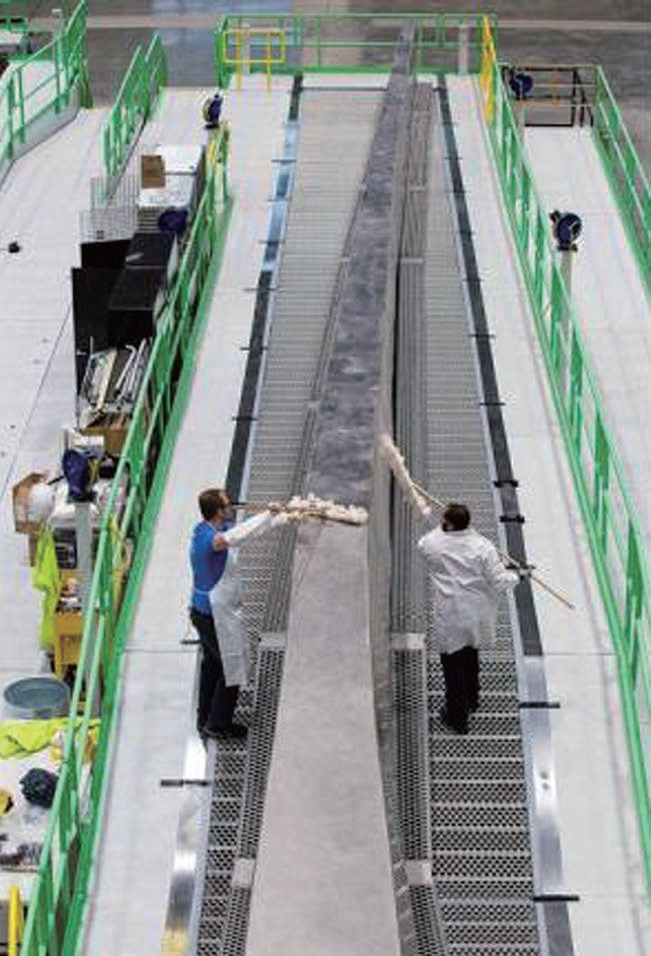
图4 B777X 客机翼梁“U”形模具
空客公司
空客公司的复合材料应用比例是渐进增长的,从最初在A300 上不足5%,到A310、A300 上约5%,再到A320升至10%,A380 则达到了25%,A400M升至30%,直到A350XWB 的52%。
1 A380 客机
A380 客机的复合材料用量为25% 左右,应用部位包括了中央翼盒、尾翼、襟翼、副翼、扰流板、机身上壁板、机身地板梁、机身后体球框、整流罩等,其最大设计特点是首次将复合材料应用于中央翼盒,并达到减重1.5t 的效果。A380 客机中央翼盒采用ATL工艺制造,复合材料层板厚度达到50mm 以上,翼身对接区更达到100mm 以上,突破了大厚度复合材料结构的设计、制造和验证技术。
A380 客机的水平尾翼和垂直尾翼同样采用了ATL 工艺,而在后机身和机翼外襟翼上使用了AFP 工艺,后机身压力框采用了树脂模渗透成型(Resin film infusion, RFI)工艺。
2 A400M 军用运输机
A400M 是2003 年推出的一款军用运输机,于2009 年12 月首飞,复合材料用量约为30%,应用部位包括了机翼、平尾、垂尾和货舱门等,主要的创新工艺有翼梁的热隔膜预成型(Hot drape forming)工艺、舱门及后压力隔框的真空辅助树脂渗透(Vacuum assisted process, VAP)工艺,机身后部装卸坡道和发动机进气道的树脂渗透技术(Resin infusion, RI)工艺等。
A400M 复合材料机翼由英国GKN 公司负责生产,材料为美国Cytec 公司提供的977–2 碳纤维增韧环氧预浸带。A400M 复合材料翼梁具有一定的代表性,采用了“ATL 工艺+ 热隔膜预成型+ 热压罐固化”制造,前、后梁均长19m,前梁分为12m 和7m两段,后梁分为14m 和5m 两段。制造翼梁的具体工艺过程为:首先通过ATL 工艺铺放出平板预成型体,如图5 所示,再将该预成型体夹在两层隔膜之间并转移至热隔膜机上,在隔膜之间抽真空后封装,从预成型体上方进行红外加热至所规定的工艺温度,此时树脂可流动,隔膜可延展,然后再次抽真空,将预成型体均匀压到模具上,进行一段时间的保压以保证预成型体弯成为“C”形,最后取下预成型件,撕去隔膜,将“C”形预成型件转移到固化工装上装夹好进行热压罐固化成型。其工艺优点在于生产效率较高,缺点是制造复杂外形零件较困难,因为生产工序较多,纤维容易褶皱,设备要求较高。
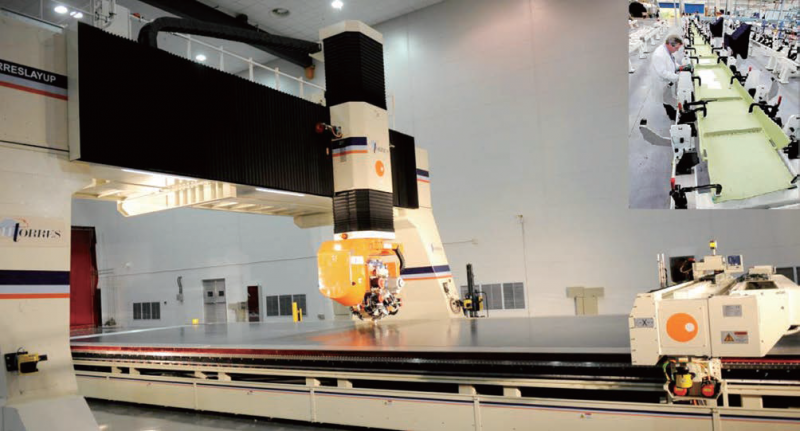
图5 A400M 翼梁采用ATL 工艺制造
3 A350XWB 客机
A350XWB 客机项目于2005 年10 月启动,客机于2013 年6 月首飞,2014 年12 月首架交付。其结构材料几经修改,最终和B787 客机类似,在机翼和机身上大量使用了复合材料,用量达到了52%。A350XWB 机翼和机身的复合材料选用了美国Hexcel 公司生产的M21E/IMA 预浸料。早期,A350XWB 机翼蒙皮采用ATL 工艺制造,但随着AFP 工艺在复杂轮廓和变厚度铺层方面的优势,机翼蒙皮也同长桁和翼梁一样,改为了AFP 工艺制造(图6)。以翼梁为例,前、后梁长均约31m,分别由3 段组成:前梁内段长7m、中段长12.7m、外段长11.5m,后梁(图7)每段长约10m。前梁在制造过程中,采用了可旋转的15m 殷钢芯轴,在其上铺放纤维丝束,铺放完成后,对称切割成两件“C”形梁,再转移到固化模具上,进行热压罐固化;后梁采用殷钢模具和五坐标自动控制,模具固定在转动芯轴上铺设,机器可按要求自动控制铺放厚度,铺设完成后的热压罐固化与检验同前梁一致。
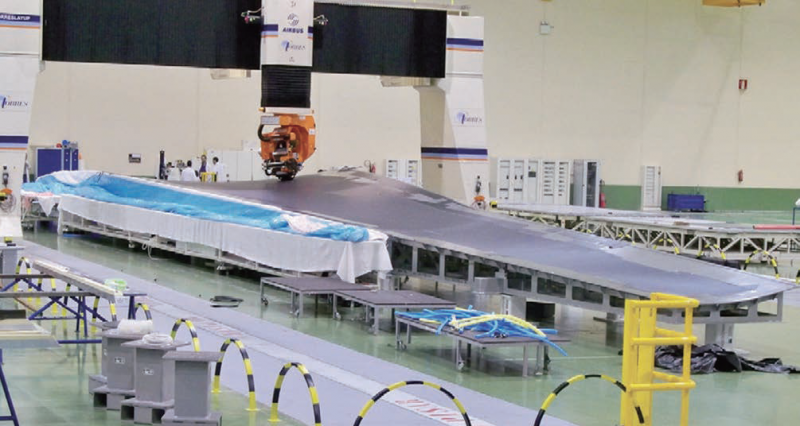
图6 A350XWB 机翼下壁板蒙皮AFP 工艺
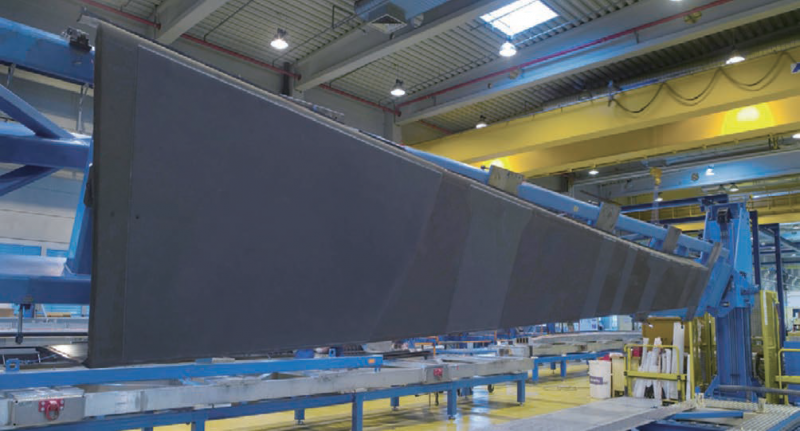
图7 A350XWB 机翼后梁
A350XWB 机身制造方案与B787不同,机身筒段分为前、中、后3 段,每段筒段由4 块壁板拼接而成,壁板蒙皮和长桁共固化成型,再通过铝合金框装配而成,图8 为机身蒙皮的AFP工艺。这种分块式机身筒段壁板方案,在兼顾可制造性的同时,能根据筒段各处受力情况进行结构优化,在维修性上也具有一定的优势。A350XWB 客机具有代表性的AFP 设备为:
(1)翼梁AFP 设备。由西班牙M.Torres 公司提供,如图9 所示。该设备考虑了在纤维丝束按45° 铺放到90° 弯角时边缘可能出现的问题,可实现沿着梁的“U”形结构进行铺丝,考虑到M21E/IMA 预浸料的低黏度,其铺丝头可以提供更高的温度和更大的压力。该设备的铺丝速度高达60m/min,大幅提高了生产效率。
(2)机身AFP 设备。由美国Electroimpact公司提供,采用了专用于机身铺放的双头自动纤维铺放机,在完成铺放的同时还能执行切割动作,能够弯曲双向铺覆倾斜且复杂的表面,进给速度可达50.8m/min。
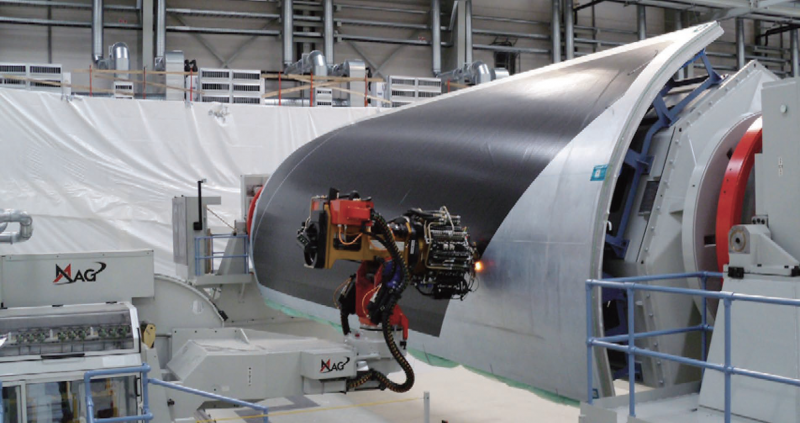
图8 A350XWB 机身蒙皮AFP 工艺
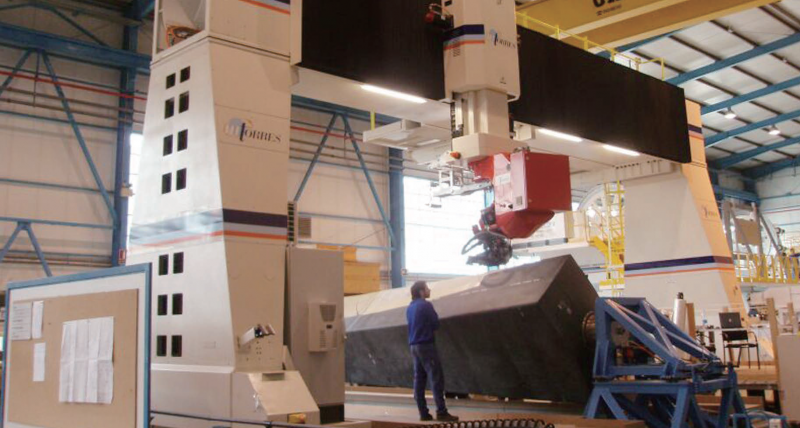
图9 A350XWB 翼梁AFP 设备
中国商飞
中国商用飞机有限责任公司作为国内最大的民机主制造商,在推动复合材料应用于民机结构方面做了诸多尝试。
(1)首架正式投入航线运营的ARJ21 支线客机复合材料用量为2%左右,其方向舵和翼梢小翼采用了碳纤维/ 环氧树脂复合材料,翼身整流罩和机头雷达罩采用了玻璃纤维/环氧树脂复合材料。
(2)2015 年底下线、2017 年首飞的C919 客机,其复合材料用量达到了12%,应用部位包括了水平尾翼、垂直尾翼、翼梢小翼、后机身、雷达罩、副翼、扰流板和翼身整流罩等。C919 客机中央翼盒原计划采用复合材料,但由于缺乏应用及验证经验,为了保证研制进度,最终改为了传统的金属结构。
(3)2015 年12 月,中国商飞北京民用飞机技术研究中心完成了远程宽体客机前期论证项目复合材料机身曲面加筋壁板工艺验证件的研制。该壁板弧长6.05m、航向长度3.5m,由29 根帽形长桁、6 套“C”形隔框和连接角片组成,如图10 所示。帽形长桁采用热隔膜预成型工艺,固化后的干长桁与AFP 工艺铺贴的湿蒙皮共胶接成型。该壁板是国内第一件采用AFP 工艺制备的大尺寸机身曲面壁板,为后续宽体客机型号研制在验证工艺方案可行性和积累工艺参数方面奠定了基础。
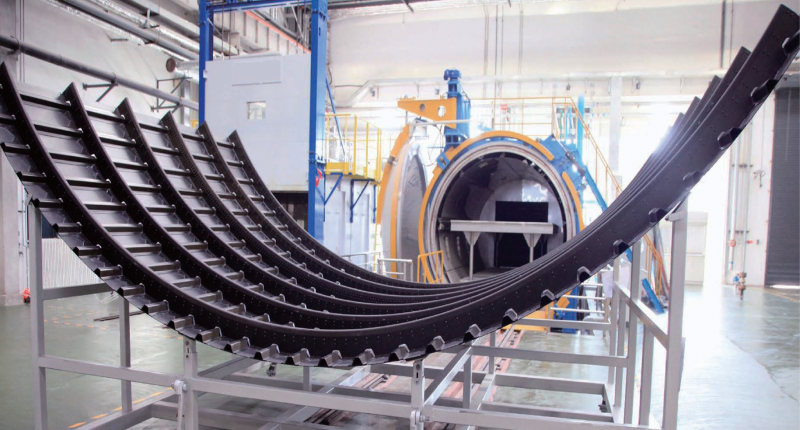
图10 宽体客机前期论证机身曲面加筋壁板
(4)中国商飞于2012 年启动了C919 复合材料机翼研制攻关项目,以C919 客机为平台,全面开展复合材料机翼的设计分析、制造装配和试验验证。2018 年,C919 复合材料机翼研制攻关项目典型盒段静力和损伤容限试验顺利完成(图11),这也是国内首次干线飞机级复合材料机翼盒段静力和损伤容限试验。该项目形成了较为完整的复合材料机翼结构设计原则、强度分析方法和设计许用值数据库,并首次在国内民机重大预研项目中建立了复合材料机翼的“材料– 设计– 分析– 工艺– 装配–试验”全流程体系。
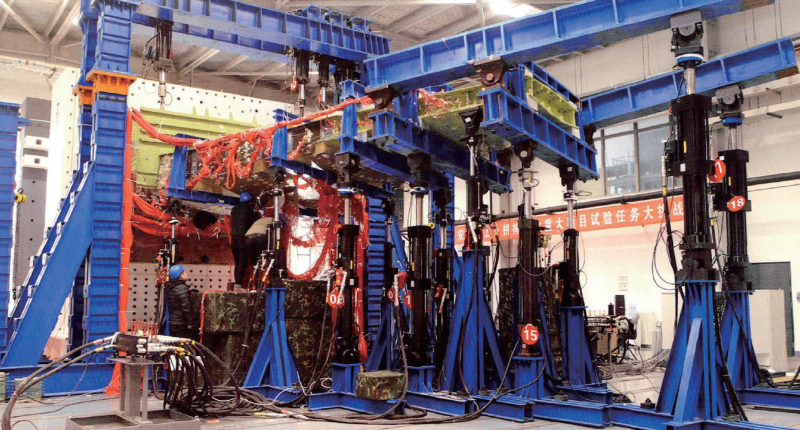
图11 C919 复合材料机翼研制攻关项目典型盒段静力和损伤容限试验
(5)2018 年底,由中国和俄罗斯联合研制的CR929 攻破关键技术难关,CR929 宽体客机复合材料前机身攻关全尺寸筒段顺利总装下线(图12),该全尺寸筒段长约15m,直径约6m,环向壁板分为4 块,由纵缝拼接而成,最大框弧长约6m。该筒段的研制突破了壁板AFP 工艺、全尺寸级长桁制造和装配等技术难题,是国内首次采用全复合材料设计理念开展的宽体客机机身大部段研制工作。
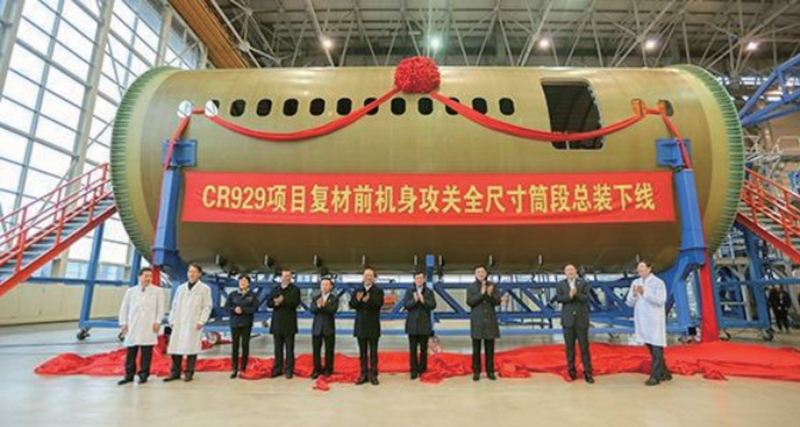
图12 CR929 飞机前机身攻关复合材料全尺寸筒段
CR929 远程双通道宽体客机计划在机翼及机身结构上大面积使用复合材料,预计使用比例超过50%。此项目进一步提升了我国复合材料机身研制技术成熟度。
其他飞机主制造商
1 俄罗斯联合航空制造集团公司
由俄罗斯联合航空制造集团公司(OAK)主持研制的干线客机MS–21(又称MC–21)于2017 年5 月首飞。该机包括了MS–21–200(可搭载135人,航程6000km)和MS–21–300(可搭载163 人,航程5900km)两种型号,其复合材料用量均约40%,可实现机体减重10%~15%,应用部位包括了外翼盒段、中央翼盒、襟翼、副翼、垂尾、平尾和发动机短舱。MS–21 客机机翼壁板、翼梁和中央翼盒均采用了一种复合材料液体成型工艺:真空辅助树脂传递模塑(Vacuum assisted resin transfer molding, VARTM)工艺,即模具型腔抽真空,使用液体树脂以压力注入干纤维然后成形,固化过程使用固化炉而不依赖热压罐。该工艺的实现得益于树脂材料的进步,MS–21 客机选用了由美国Cytec 公司研发的中模高强碳纤维TX1100和EP2400 树脂,该树脂体系采用先进的增韧技术,有效解决了树脂韧性与黏度的矛盾,在提高树脂韧性的前提下,可在低黏度状态下保持足够的工艺时间,使大尺寸制件的树脂完全浸润成为了可能。
MS–21机翼翼盒如图13 所示。MS–21 机翼壁板蒙皮利用龙门立式自动铺丝机在阴模铺贴成预成型体。壁板长桁为“T”形截面,利用自动铺丝机在“C”形阳模进行铺贴,然后分切成两个“L”形预成型体,组装成“T”形长桁后,再与蒙皮组装成壁板预成型体,转移至树脂热注射设备进行注胶,注胶结束后进行固化炉成型。
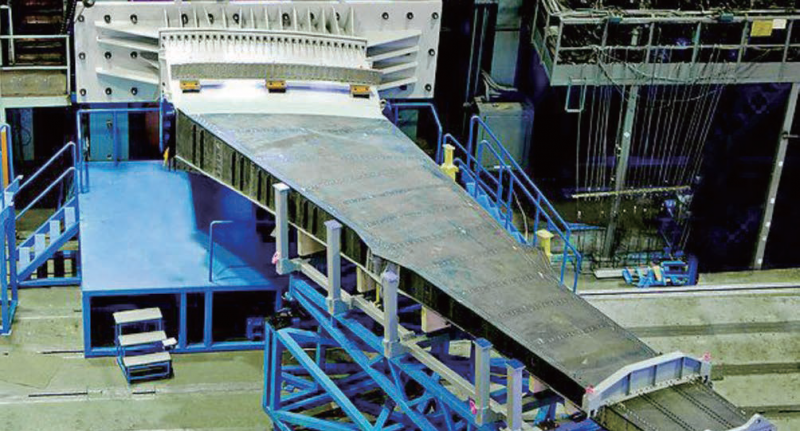
图13 MS–21 机翼翼盒
MS–21 机翼翼梁采用了上下缘条及腹板等厚结构,翼梁不分段整体制造,如图14 所示,翼梁最大厚度12mm,最小厚度4mm,首先在阳模上将碳纤维干丝铺贴成预成型体,再通过转移工装转到阴模后进行注胶及固化炉成型。
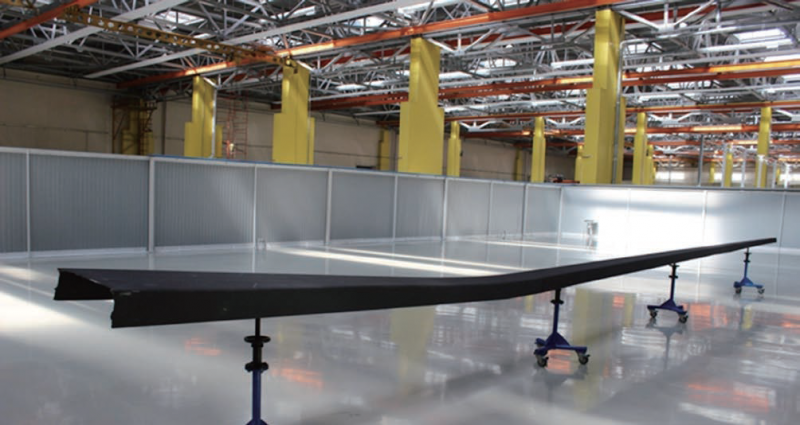
图14 MS–21 机翼翼梁
MS–21 客机是全球第一架采用非热压罐工艺(Out of autoclave)制造主承力结构件的大型民机,零件最大尺寸达到了20m×4m。其工艺实现了大型加筋结构的整体化成型,并具有设备投入少、能耗低、结构减重效果好的优势,这也是MS–21 客机的重要卖点之一,但其也对成型模具提出了很高的要求,需要在工艺可操作性和结构精度方面实现良好的平衡。
新MS–21 客机装备了俄罗斯自主研发的PD–14 发动机,于2020 年12 月15 日完成了首飞。由于国际形势的变化,俄罗斯正开展碳纤维干丝和树脂的自主研发,后续的MS–21客机将转向俄罗斯国产的复合材料。
2 加拿大庞巴迪公司
C 系列客机是庞巴迪公司研制的新型单通道窄体干线客机,市场定位为100~149 座级的客机,于2013 年9月首飞,包括108 座的CS100 和130座的CS300 两款机型,翼展35.08m。C 系列客机的复合材料用量约为46%,应用部位包括外翼盒段、中央翼、平尾、垂尾、机身尾段和尾锥等。
C 系列客机外翼盒段使用了具有专利的树脂转移注射(Resin transfer injection, RTI)工艺制造,材料为无屈曲织物(Non-crimped fabric, NCF),手工铺贴蒙皮、长桁和翼梁的预成型体,然后将预成型体转移至阴模,并在热压罐内进行注胶及固化。RTI 工艺兼顾了液体成型工艺和热压罐固化的优点,可进行复合材料制件整体化成型和复杂型面成型。热压罐的固化压力可加速大尺寸结构树脂浸渍过程,并保证预成型体的质量以及降低制件的孔隙含量。制件的纤维体积含量可通过注入树脂的含量和热压罐压力有效控制。
结论与展望
综合大飞机的先进性、使用特性、制造技术水平和成本考量等因素,主承力结构使用复合材料已是大势所趋,且向着复合材料结构的整体化、大型化、制造与装配自动化前进。出于经济性的考虑,以液体成型为代表的非热压罐制造工艺以其整体成型、复杂型面成型的能力和低能耗、低成本的优势必将成为飞机主承力结构制造技术的主要发展方向。
先进复合材料作为我国的一项“卡脖子”技术,亟需突破复合材料应用到主承力结构的设计分析、制造装配、试验验证等关键技术,建立符合适航标准的大型民机复合材料主承力结构研制全流程。
我国通过民机型号研制以及一系列民机预先研究,已初步建立了“设计– 制造– 装配– 维修”的复合材料一体化概念和相配套的技术体系,但也面临着材料体系单一、材料规范不全、材料性能数据积累不足、供应链不完善等问题。
随着国际竞争的加剧,先进复合材料作为我国的一项“卡脖子”技术,应以“自主可控”为目标,尽快实现其国产化,并提升其设计分析、制造装配、试验验证等关键技术的成熟度,建立符合适航标准的大型民机国产化复合材料主承力结构研制全流程。