1 不同模具在复合材料制造中的优缺点
铝合金模具具有密度低,致密性好,良好的热传导性能,使得铝合金升温快,在构件制造中能更好的加热成型,但在制作复合材料构件时,由于其膨胀系数与复合材料的膨胀系数差异过大,导致在制造构件时会产生较大内应力,使得复合材料产生变形,不利于复合材料构件性能的稳定性。机械加工合金钢模具虽然具有良好的耐久性,并且热膨胀系数比铝合金低50%,但其质量大、升温性能低、温度分布不均匀,容易产生应力,因此难以用于制造高精度的复合材料制品。
镍电铸模具具有比合金钢模具密度低,热传导性能好,热升温性能好,并且可以制造复杂型面的优点,但其模具本身的制备加工周期长,零件维修困难,其热膨胀系数为12.3×10-6/℃,远高于复合材料的热膨胀系数,导致也不适用于制备高精度的碳纤维复合材料(热膨胀系数为2——4×10-6/℃)和芳纶纤维复合材料制品。
石墨模具的导热率高,升温效果好,虽然石墨的导热速率没有铝合金和其他金属模具高,但石墨模具的热膨胀系数与芳纶纤维复合材料,碳纤维复合材料相匹配,因此适用于复合材料构件的加工,其次石墨模具的热质量低,与复合材料相近,使得石墨模具在升温时在单位体积内所需要的热量和复合材料相同,但石墨模具的强度和耐磨耗性低,脆性大,抗冲击性能差,容易受到损伤,不利于制作大型或者复杂的型面,且其真空性差,成本高,制造周期较长,并且在大批量加工生产存在困难。
2 复合材料模具的优点
2.1 热膨胀系数匹配良好
由于复合材料的热膨胀系数小,因此在使用金属模具的时候,由于金属的热膨胀系数太大而复合材料的热膨胀系数较小,在加热固化时可能会产生内应力,而复合材料模具由于也是用复合材料制成,使得复合材料模具与复合材料构件的热膨胀系数相差不大,能够在固化的时候更加适应,减小残余应力的产生,。因为在加热固化的时候,随着温度的升高,模具会受热产生膨胀,进而尺寸会发生变化,导致尺寸变大。因此制造尺寸也会随着发生变化。当固化完成后,随着温度的降低,模具和固化好的制件会发生收缩,若成型模具材料和制件材料的热膨胀系数差距过大,使制品和模具之间产生内应力,则必然会使两者见尺寸产生偏差,而当模具是由复合材料制成时,由于复合材料模具和制品的热膨胀系数相匹配,使复合材料模具在热膨胀和降温收缩的过程中的尺寸变化对制品影响较小,对于制造构件,热膨胀系数不仅会对构件的尺寸带来影响,还会使构件产生变形,脱模的问题。
从构件在加热固化使模具和其构件膨胀中可以知道,当模具和构件固化时热膨胀系数相差过大时,由于内应力的存在,将会对构件的精密度,构件的尺寸产生影响,使得所制得的构件与设定的构件产生偏差,构件报废。下页表1为长度为7m的复合材料构件在200℃成型时,几种常见复合材料模具的热膨胀系数和受热时模具的增长长度,由表中可得,当热膨胀系数越大,其模具在加热时尺寸变化就越大,对构件的影响也越大,并且与低碳钢和铝合金相比,碳纤维复合材料的热膨胀系数更低,因此在制作复合材料构件时模具对构件的影响更小。在制作复合材料构件时应选择热膨胀系数相匹配的材料。据报道,长达18m的Delta-Ⅲ型运载火箭整流罩成型时,就是用了复合材料模具才保证了其要求非常高的外形准确性和尺寸精度。
表1是各种材料成型模具的热膨胀系数,从表中可知,铝合金的热膨胀系数最大。而invar合金的热膨胀系数很小,用他做成型模具可以很好地与复合材料构件的热膨胀系数相匹配,得到较好的尺寸精度,这是最具有竞争力的一种材料成型模具,但invar合金的缺点是加工较难,且价格昂贵。
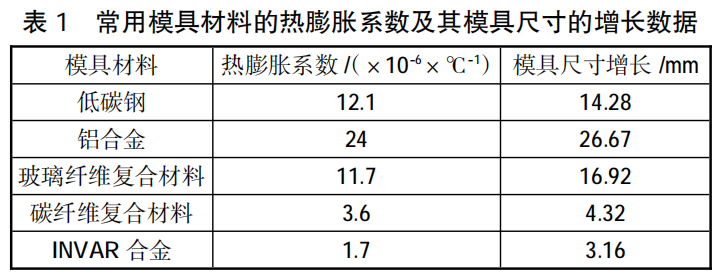
2.2 热熔小
复合材料模具的比热容大,因此在单位质量下,升高一度所需的热量就越大,但由于复合材料的密度远小于金属材料,导致在生产过程中,复合材料模具的质量远小于金属材料模具,使得模具的热容比金属材料更小,在实际生产过程中,由于复合材料热容更小,导致复合材料模具所需的热量就更少,能更加快速升温让构件固化,在更短的时间内完成生产加工,降低了工时,节约了能源,节约了构件生产成本。
2.2 密度小
因为复合材料的密度小,复合材料密度仅为钢材的1/4左右,见表2。因此,用复合材料制造生产的模具质量都比较轻,因此在使用的过程中便于运输。且由于碳纤维复合材料具有高强度,高模量,低密度等特点,所以用它制作的模具成型面厚度一般在6——9mm之间,非常薄,即使是大型复杂的模具也非常轻,方便搬运和使用。
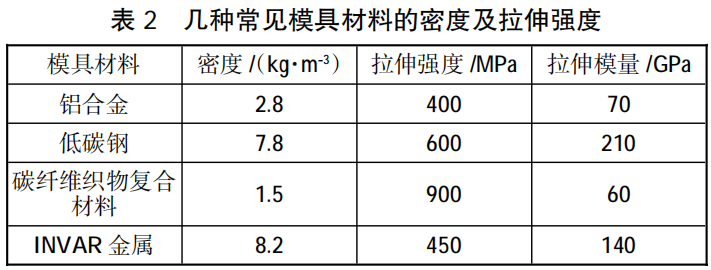
2.4 尺寸热稳定性好
当模具型面非常复杂且尺寸较大时,若用金属模具生产大型型面时,由于金属模具质量大,使用过于笨重,铝液充型时间过长,导致生产的构件表面内部有气孔或者疏松等缺陷,降低了构件的力学性能,也影响了复合材料构件的气密性。若采用复合材料模具生产,由于复合材料模具是由母模翻制而成,并且母模的生产加工难度远小于金属材料,此外还可以在复合材料模具表面喷镀金属,降低了复合材料构件表面的粗糙度。
3 复合材料模具存在的问题
3.1 工艺复杂
相比于金属材料模具,复合材料模具在制造中需要母模,而在母模具的制造过程中,模具的选材受到制造成本和时间,几何形状、质量、升温速度和模具精度等影响,此外模具制造还需要较高的固化温度和压力,因此要求母模具在这样的高温高压下保持稳定,因此对复合材料的选择提供了一定的困难。而复合材料在温度越低时,其内应力越小。为了减少复合材料模具的内应力,科学工作者研究出了多种低温固化方法。
3.2 表面硬度较低
相比于金属材料模具,复合材料模具的表面硬度较低,当受到碰撞时容易造成机械损伤,胶衣或镀层的脱落,从而降低复合材料模具的精度,在制作复合材料构件时会影响复合材料构件的精密度。另外在起吊,运输过程中受到撞击容易产生分层,掉渣,变形等问题,导致复合材料模具损坏,影响其正常使用。
3.3 使用寿命短
相比于其他金属材料模具来说复合材料模具使用寿命相对较短,复合材料模具的使用寿命一半只有十几次,而金属材料模具的使用寿命一般有上千次,进而导致需要大量制造复合材料模具,导致复合材料模具成本变相增加,而复合材料模具由于制造工艺比较复杂,其复合材料模具产品质量不等,可能导致构件精度存在些许差异。虽然,目前在国外存在使用寿命较高,质量良好的复合材料模具,但目前还没有出现使用近千次还未出现问题的例子[3]。
露气寒冷,将凝结也
寒露是二十四节气中的第17个节气,是干支历酉月的结束以及戌月的起始;时间点在公历每年10月8日或9日视太阳到达黄经195°(处于室女座)时。
露气寒冷,将凝结也
寒露是二十四节气中的第17个节气,是干支历酉月的结束以及戌月的起始;时间点在公历每年10月8日或9日视太阳到达黄经195°(处于室女座)时。
3.4 成本较高
虽然复合材料模具较金属模具有较多优点,但由于复合材料模具较为繁琐的制作流程和复杂的工艺,其制造成本还是比普通金属模具要高不少。
4 复合材料模具的发展方向
4.1 新技术和新材料的研发
新技术的开发能够在保证质量的同时降低复合材料构件的生产周期,从而减少复合材料的生产成本,提高复合材料生产效率。而复合材料生产与新技术的结合可以在生产复杂型面时更加便利,也能完成多种材质,多种形状,多种功能的模具制作和生产。此外新材料的研发可以降低成本,提高模具质量。在这方面英国先进复合材料公司(ACG)开发的一种商品名为zpreg的预浸料,是一种通过条形浸渍工艺制成的新型织物预浸料。这种预浸料不但保留织物原有的良好铺贴性能,而且提高铺贴过程的排气效果。
4.2 使用寿命延长
由于复合材料模具本身的使用寿命不高,因此我们希望能够提高复合材料模具的使用寿命,而在复合材料的使用中,当孔隙过多,复合材料的强度就会下降,因此提高使用寿命的方法主要就是提高模具的硬度和强度来提高复合材料的抗损伤能力,并且减少孔隙对复合材料的影响,常见的方法就是涂覆胶衣或者金属膜。复合材料的孔隙主要包括泛树脂空隙,夹层孔隙,未浸润孔隙和小分子气化孔隙等,其中在固化工程中树脂中小分子气化中带入的空气是复合材料构件孔隙形成的主要因素。因此在实际操作中往往嵌入气密性良好的弹性薄膜来解决空气进入产生孔隙的问题。
4.3 成本的降低
复合材料模具都是由母模所制成,一个母模可以制造许多的模具,当固定成本一定时,生产的模具越多,复合材料模具本身的成本也就越低,其次在选择模具时应选择最适合生产复合材料的,要对复合材料的性能及其使用寿命进行一个了解,选择合适的模具也可以降低制造成本,还能降低生产周期,避免复合材料生产的浪费。
4.4 复合材料结构的改变
在复合材料的生产中,由于成型模具和构件之间在压力罐的作用下始终紧紧合在一起,因此成型模具表面的温度变化对构件的影响很大,如果复合材料上存在温度梯度,就会产生温度的不均匀,导致其构件固化不一致,形成残余应力,严重则可能导致材料的报废。目前将改进复合材料的结构来减小复合材料上温度梯度的产生,根据花蕾蕾等人的实验,其采用阶梯形非等厚型板通过在高温区域将板的厚度进行阶梯形降低,而不采用突变,可以较大限度地减小温度的突变,改善均匀性,降低表面温差,降低温度梯度对复合材料构件所产生的影响,使温度均匀性达到最佳状态,避免温差过大使得构件力学性能降低。
5 结语
先进复合材料属于新型材料,与普通材料相比,它拥有高强度、抗疲劳性高、较好的抗腐蚀性,因此在20复合材料的推动下,复合材料模具已经逐渐形成产业,目前碳纤维预浸料复合材料模具已经用于制造雷达罩,B757发动机壳体,A320垂尾,B747排放滑动接头等材料。随着航空航天的发展,复合材料模具会取代金属模具并被广泛用于各种领域,而复合材料模具的发展将提高复合材料产品的质量和精度。在未来的发展中,复合材料模具能得到更好的、精度更高的复合材料模具,缩短材料生产周期,为国家建设起到意想不到的收获。
作者:李耀虎