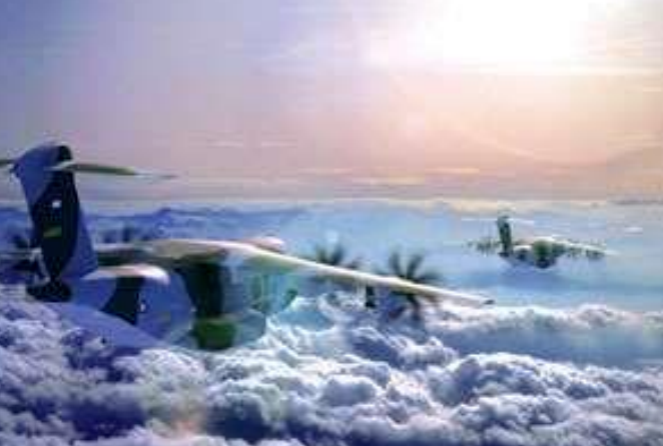
艺术家的构思展示了货舱的后端,由两部分组成的货舱门形成了后机身光滑、上翘的下腹。
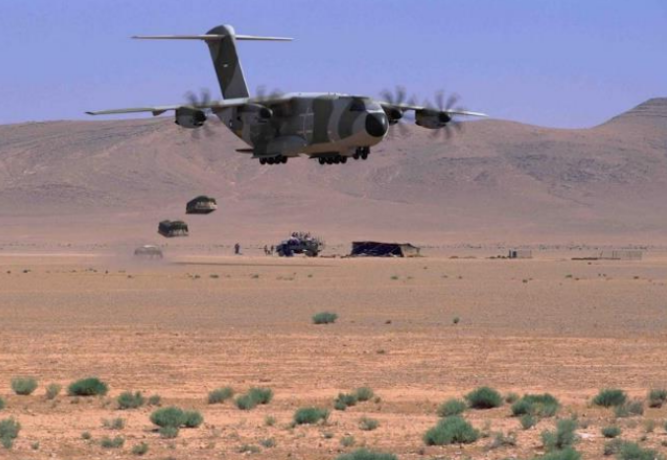
A400M 不同寻常的分体式货舱门配置允许在无需降落和起飞的情况下进行设备/补给空投等战术演习。
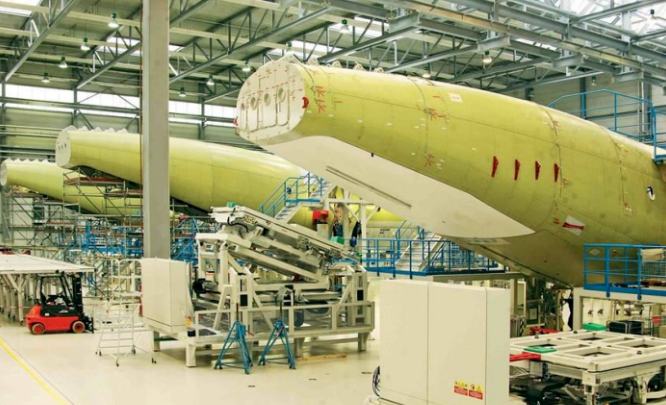
三个A400M机身段已准备好安装舱门,最近的机身段上已安装好复合材料上部。
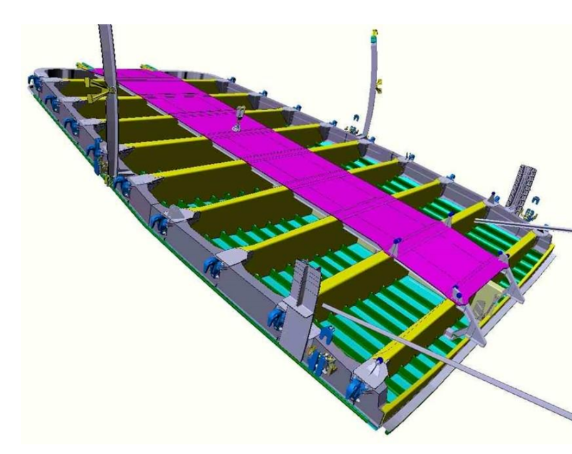
步骤1:CAD图纸显示整体零件设计:外板为蓝绿色,整体加劲桁条为深绿色,横梁为黄色。较小的部分内门显示为粉红色。注意零件周边的端壁。大钩连接处用于在飞行中密封门。
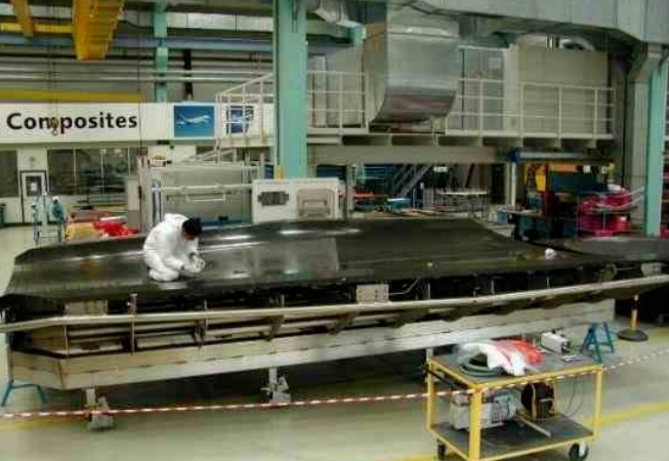
步骤2:一名技术人员将干式多轴无卷曲织物和单向碳纤维增强材料,放置在一个复合材料凹模模具中,成为门板外蒙皮。
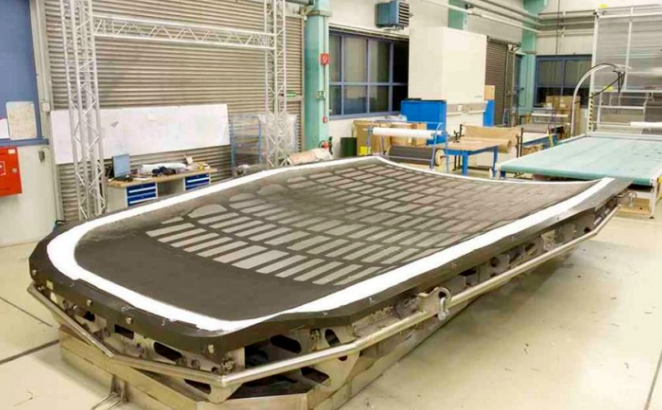
步骤3:完成外蒙皮铺放。注意桁条和横梁位置处的堆积模式。
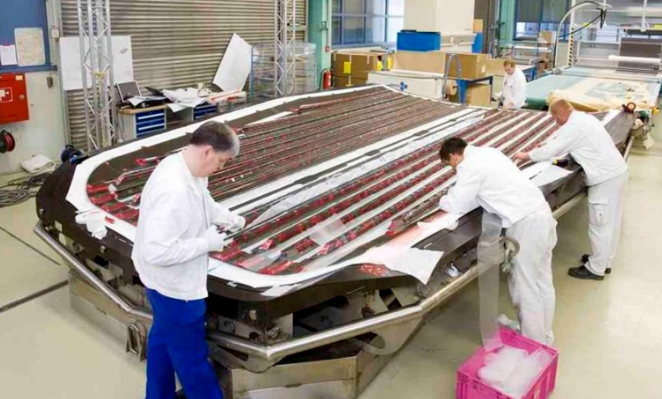
步骤4:将预成形长桁放在门板上,并用GORE-TEX薄膜装袋。在装袋和输液过程中,一系列胶带将预成形长桁及其相关工具固定在一起。
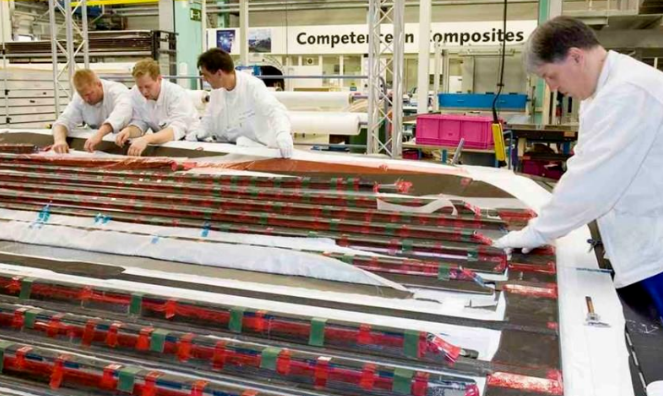
步骤5:装袋过程的特写,显示桁条在门板上的位置。

步骤6:蒙皮和桁条固化完成后,将部分完成的零件放入临时木制夹具中进行无损检测。资料来源:EADS军用航空系统公司,奥格斯堡
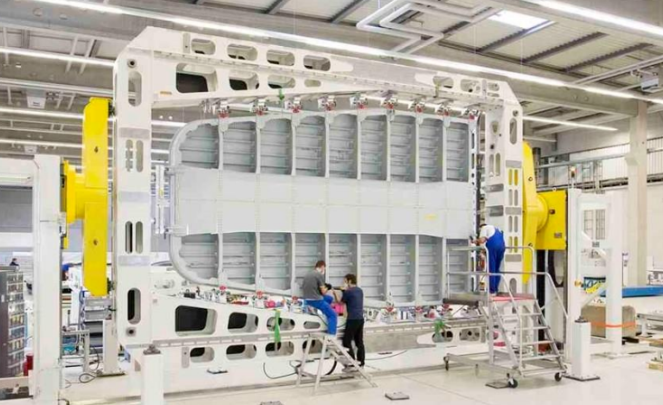
步骤7:一个可操作的夹具将零件固定在适当的位置,用于钻孔和精加工步骤,因为横梁、端壁和铰链都用金属紧固件连接。
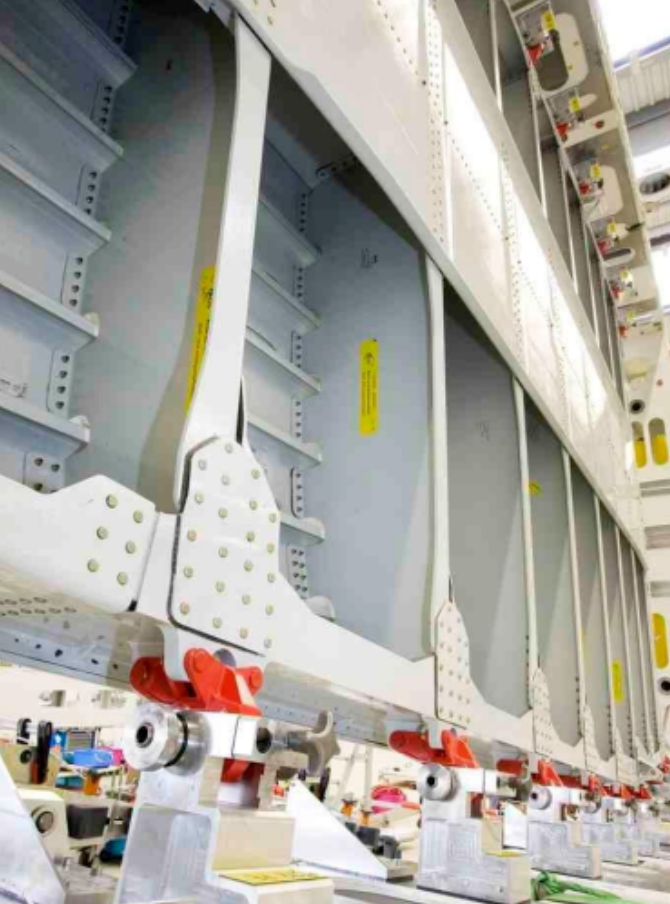
步骤8:涂漆部分的特写显示了将横梁固定在外板和端壁上的金属紧固件。
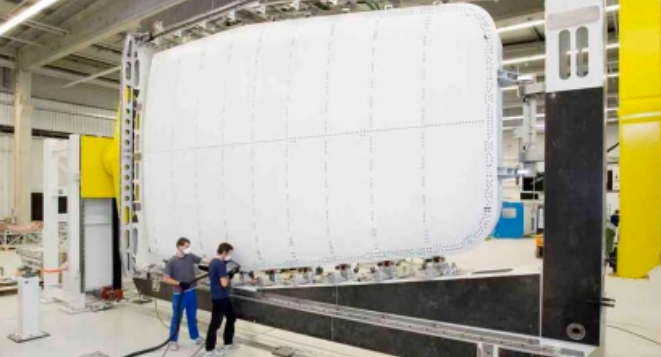
步骤9:完成的门的外表面
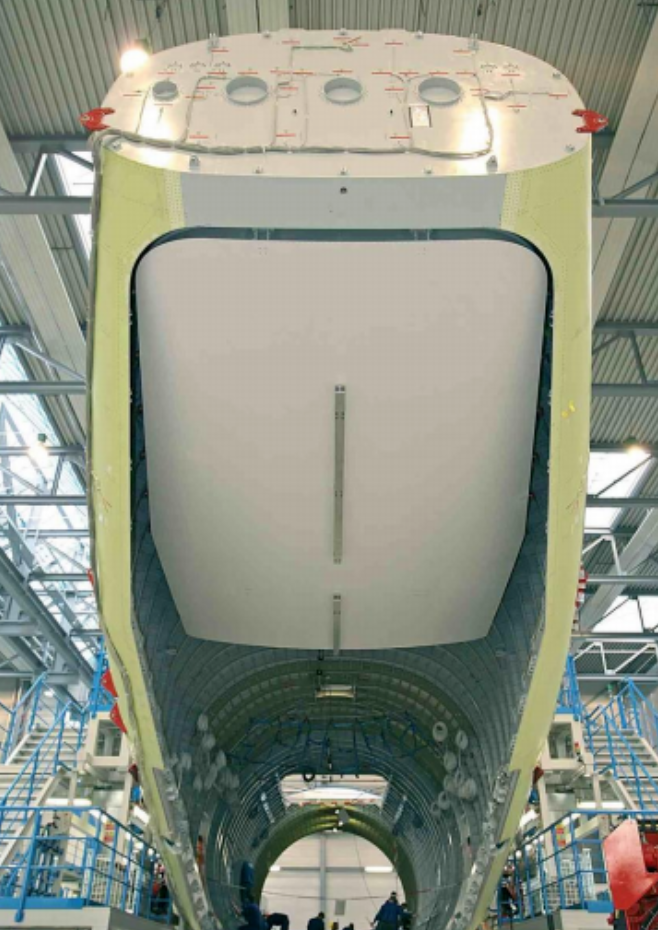
步骤10:安装在A400M后机身上的第一扇舱门。
空运能力和物资便携性是任何国家军事和应急准 备的关键要素。到目前为止,波音公司的 C-17“环球霸王”和洛克希德·马丁公司几十年前推出的 C- 130J“大力神”已经构成了世界上大约2300辆老化军用运输工具的大部分,其中许多将进行翻新。空中客车军用公司(法国布拉尼亚克)希望通过其新型A400M货机占领这一战略市场的一大块。
新的空运机比C-130J稍大,但比C-17小,是复合材料密集型的——A400M的复合材料翼梁的设计和制造,将支持世界上最大的涡轮螺旋桨飞机发动机,在上一期的HPC中有描述。该飞机的垂直和水平尾翼在西班牙生产,也是一种大型碳纤维/环氧树脂部件。
今年 1 月,欧洲航空防务与航天公司(EADS)军用航空系统事业部(德国奥格斯堡)向空中客车公司交付了第一扇A400M上部货舱门,这是迄今为止使用真空辅助树脂灌注工艺生产的最大的结构复合飞机部件。EADS Augsburg 是空客家族最大的外部供应商, 并通过其能力中心帮助设计和推广航空结构的创新材料和技术。其中一扇货舱门最近在法国巴黎的 JEC复合材料展上展出。该门代表着在高要求的结构应用中低成本、热压罐外固化的重大突破。
降低成本的设计
A400M有四个涡轮螺旋桨发动机和高机翼,设计有打开机身后部的货舱门。本文中描述的7米/23英尺长、4米/13英尺宽的全复合材料上货舱门向上和向内摆动,而配有金属坡道的下货舱门同时向外和向下旋转,以便装载或卸载车辆和货物。当关闭时,两个舱 门形成光滑的后机身腹部。
EADS奥格斯堡公司的一位设计工程师表示,几何结构复杂的上舱门是为尽可能低的重量而设计的, 目的是减少门机构的负载,并帮助实现 A400M 的整体 重量目标。机身重量较小意味着可以拖动更大的有效载荷。此外,零件刚度必须最大化,因为门位于机身 的加压部分内,在加压循环期间受到显著的疲劳载荷。
EADS 的工程师使用有限元分析(FEA-finite element analysis)软件为预期载荷设计门。他们还选择放弃高压灭菌器,使用 EADS 的专利输液技术 VAP-vacuum-assisted process(真空辅助工艺)制造门,以最大限度地降低生产成本。与目前复合材料行业中使用的许多其他灌注工艺一样,VAP采用真空来促进干碳纤维增强体在真 空袋下的环氧树脂灌注。然后,零件在烘箱中固化, 而不是在热压罐中固化。
门由几个元件组成。最大的外壳是一个略微圆顶 和锥形的矩形,由实心、无卷曲的碳/环氧树脂层压板制成。蒙皮的内表面由 16 根桁条加固,桁条与机身长轴平行。一个单独的边缘墙,大约203毫米/8英寸高,形成了零件的周边。九根结实的横梁垂直于桁 条,并用金属紧固件连接在蒙皮上。狭窄的内层(见右侧步骤1和7)覆盖舱门内表面的中心部分,并起到 部分内层的作用,以增加刚性。它还用几个小桁条加固。用螺栓固定在外壳上的金属铰链将舱门连接到机身上,在飞行过程中,固定在边缘壁上的大型金属钩用于将舱门固定到位。
设计和VAP过程的一个关键因素是,加强桁条与门的内外蒙皮是一体的,可以节省大量的生产时间, 并消除数千个紧固件。设计团队能够省去将桁条连接到蒙皮上所需的大约3000个金属铆钉,从而节省了紧固件的重量和可观的成本。
无需热压罐
门的制造始于在EADS内部设计和制造的内模线碳纤维/环氧树脂复合材料模具上铺设外蒙皮。虽然该 公司没有公开表层的确切数量和方向,但由SAERTEX (德国 Saerbeck)提供的 0/90°和±45°风格的干碳 纤维多轴增强材料,以及由Hexcel(加利福尼亚州都柏林)提供的干单轴织物组成了层压板。最内层(见步骤3)在桁条和横梁将接触的区域有额外的堆积物。
奥格斯堡的工程师将整体加劲桁条称为“L-Z”设计,其形状基本上类似于大写字母Z,具有垂直腹板,叠加在后向大写字母L上。桁条高约65 mm/2.5英寸,下翼缘宽50mm/2英寸。桁条顶部凸缘中的多 个层板下降到垂直腹板中数量的大约一半;腹板层然 后分裂以形成水平的下凸缘。SAERTEX 0/90°和 ±45°多轴干织物以及Hexcel 的单向材料的组合构成了桁条。为了在预成型期间将干燥的桁条增强件固定到位,Augsburg 报道称,一些增强件在顶面上提供了热塑性聚酰胺面纱或薄膜;当加热时,热塑性面纱熔化并变得粘稠,从而将多层粘合在一起。
技术人员在一个廉价的木制模板上预制桁条,方 法是堆叠无卷曲织物条,然后用小热风枪加热,使热塑性塑料熔化,从而将无卷曲织物条粘合在一起。顶部凸缘上的短层结构由单向材料制成;0/90°和 ±45°的材料通过腹板形成连续的铺层。将一个由小直径碳纤维编织物制成的三角形“面条”或填充物插入铺层分裂处形成的空隙中,形成平坦的下凸缘。
然后将预成型的桁条放置在叠层蒙皮上。长的碳纤维/环氧树脂芯模放置在每个桁条的两侧,以将预成 型件保持在正确的形状,并在固化过程中提供固结压 力。然后,每个桁条及其心轴覆盖由 W.L.GORE&Assoc.(特拉华州纽瓦克)提供的 GORETEX 透气膜材料。
当所有桁条都就位并装袋后,技术人员用标准通气材料和装袋膜将整个门——蒙皮和桁条——装袋, 并为输液做准备。该树脂为RTM-6单组分环氧树脂, 由Hexcel制造。据报道,这种众所周知的灌注树脂易于加工,在 180°C/350°F 的温度下具有良好的热/湿性能,并且它的加工窗口超过两个小时,足够时间灌注这种尺寸的一部分。
当 VAP 过程启动并在外袋上抽真空时,GORETEX允许从每个桁条袋中排出空气。由于仅使用真空压力将树脂引入每个桁条和蒙皮中,GORE-TEX确保树脂留在每个桁条袋中,以便完全浸泡。该公司声 称,这种特殊的薄膜使共聚概念发挥了作用。一位工 程师表示:“GORE-TEX 允许空气通过,但不允许树 脂通过,因此我们可以确保每个桁条完全排空空气和 注入树脂,最大限度地提高最终纤维含量,最大限度减少空隙。”
然后将外层蒙皮/桁条部件放置在 180°C/350°F 的烘箱中数小时以固化。不需要后固化。
门的狭窄内蒙皮是以同样的方式制成的,使用同样的程序来固定其整体桁条。其余部件也使用VAP制造。端壁包括由 Rohm Degussa GmbH(德国达姆施塔特)提供的 Rohacell PMI(聚甲基丙烯酰亚胺)泡沫芯。型芯放置在横梁紧固件位置之间的区域,以减轻零件重量。
横梁是厚的实心层压板,沿其下边缘有一系列切口,以容纳桁条。梁的下边缘也有扩展凸缘,以便于通过螺栓连接到外壳上(见右侧的步骤 8)。
生产准备就绪
整个货舱门的组装包括一个大型固定夹具(见右侧步骤 9),该夹具支撑外壳,并能够组装、粘合、钻孔和紧固所有舱门部件和铰链部件。组装完成后,舱门喷漆并交付给德国不来梅的空中客车公司。据空中客车公司称,在HPC付印时,已经组装了三个机身, 其中一个将进行静态和动态测试,直至失效。
奥格斯堡的工程师指出,在全面生产时,奥格斯堡工厂每月至少必须生产三扇门。虽然手工预成型方法足以用于最初的产品,但该公司已与一家德国公司签订合同,生产一台旨在自动化桁条预成型过程的机 器,这将有助于使注入的零件更具成本效益。
A400M的首飞计划于2008年1月进行。空中客车公司拥有190多个固定订单,渴望满足其公布的时间表,并于2009 年秋季开始向客户交付飞机。A400M的成功在很大程度上取决于它——这是一个有潜力重振战略空运市场的新产品。
注:原文见,《 A400M cargo door: Out of the autoclave 》 2010.2.5.
杨超凡 2023.8.5