热塑性树脂由于本身的凝聚态结构赋予其高韧性,使其复合材料相对传统的热固性复合材料具有更为优异的性能,以及广阔的应用前景。除性能要求外,国内外对于航空业的环保性提出了更高的要求,欧盟据此提出了针对性的大型科研计划——“清洁天空(Clean Sky)”计划,目的在于通过降低能耗和噪声污染,减小航空运输对环境的影响。由于热塑性复合材料的成型过程中不发生化学反应,因此具有可回收再利用的独特优势,在提升性能的同时,对环境友好。同时,其预浸料可在常温下无限期储存,成型效率高,能够有效降低制造成本。
由于以上优势,热塑性复合材料已在大型民航飞机、直升机等航空领域取得广泛应用。如空客 A350 飞机机身卡箍采用 TenCate 公司的碳纤维织物增强 PPS热塑性复合材料制造,如图 1 所示;空客 H–160 直升机采用碳纤维增强 PEEK 热塑性复合材料代替原钛合金材料制造旋翼桨毂中央件,在降低制造成本、减轻重量的同时,提高了结构损伤容限及可维护性,标志着热塑性复合材料在直升机主承力结构上的成功应用,如图 2所示。
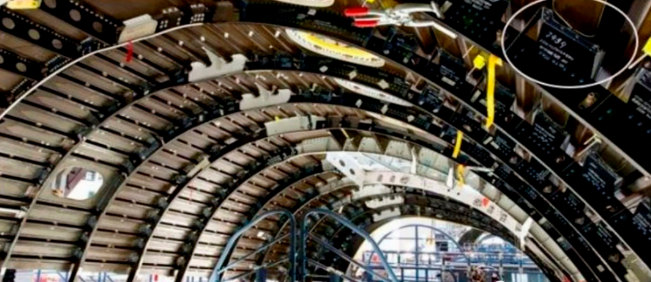
图1 空客A350热塑性复合材料机身卡箍
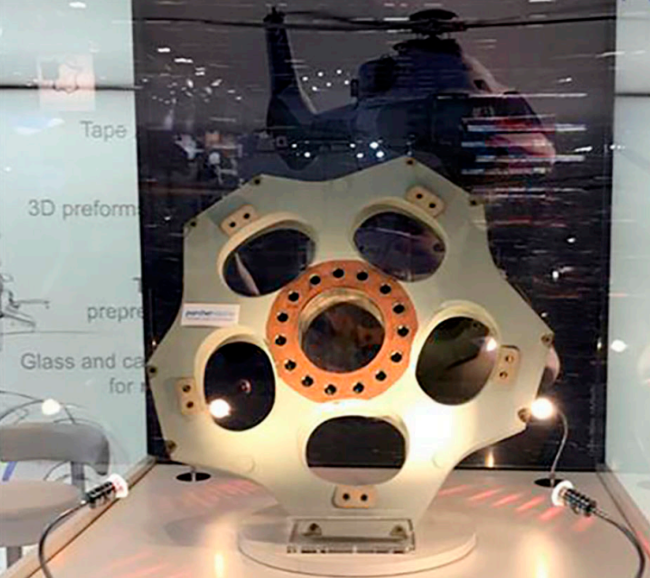
图2 空客H–160直升机热塑性复合材料桨毂中央件
在航空发动机领域,热塑性复合材料虽无法满足涡轮盘等热端部件的使用要求,但在发动机冷端部件及短舱结构上具有广阔的应用空间。目前,国外厂商已经在吊挂、进气道降噪声衬等部位使用大量热塑性复合材料,并有 GKN 航空福克公司的专家认为在风扇罩上可以借鉴飞机经验应用热塑性复合材料,如图 3 所示。
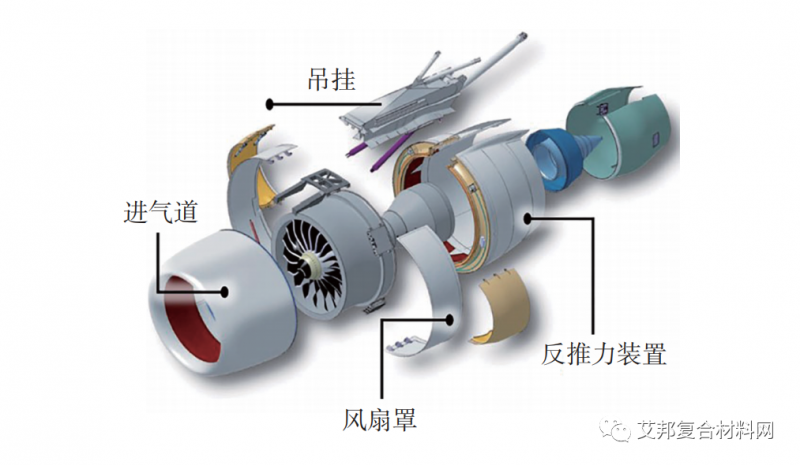
图3 热塑性复合材料在航空发动机短舱上的应用
1. 高性能热塑性复合材料及其成型工艺
目前航空结构中使用的复合材料绝大多数采用环氧、双马、聚酰亚胺等热固性树脂作为基体。与热固性树脂基复合材料相比,热塑性树脂基复合材料具有下列优势:
(1)经合理优化凝聚态结构的热塑性基体具有较高的基体韧性,热塑性树脂基复合材料耐疲劳性能好,冲击损伤阻抗和损伤容限都比热固性树脂基复合材料高。
(2)孔隙率低,吸湿率低,耐环境性能好。
(3)成型过程为熔融 – 固结的物理过程,没有固化反应,因此可重复成型和焊接成型,成型周期短、效率高、可修补。
(4)热塑性预浸料可以室温储存,且有近乎无限的储存期。
经过多年的技术积累,国外已逐步建立起热塑性复合材料完整的技术体系,主要供应商包括荷兰的TenCate、美国的 Cytec 等公司,近年来,德国 Evonik 公司以及日本 Teijin 公司也陆续开发了热塑性复合材料体系。国外热塑性复合材料制造商主要提供的热塑性复合材料有碳纤维、玻璃纤维及芳纶纤维增强的聚醚酰亚胺(PEI)、聚苯硫醚(PPS)、聚醚醚酮(PEEK)、聚醚酮酮(PEKK)等高性能热塑性树脂。这其中以荷兰TenCate 公司的材料体系及应用技术体系最为完整。
表 1 列举了国外著名制造商商品化的热塑性预浸料牌号,已形成不同种类、不同耐温等级的材料体系,并在航空发动机、商用大飞机、直升机,以及无人机等各类航空结构上均取得广泛应用。
表1 国外商品化的热塑性预浸料牌号
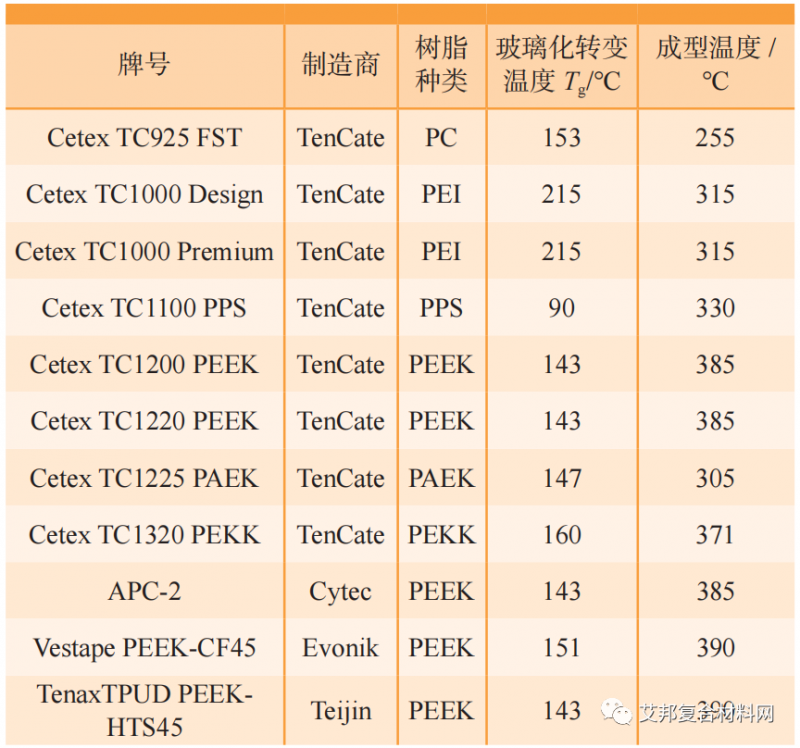
除完善的材料体系外,国外在热塑性复合材料的成型工艺方面也已发展了包括模压成型、热压罐成型、隔膜成型、冲压成型以及自动铺放成型(Automated Fiber Placement, AFP)等多种成型工艺技术。
其中,AFP 技术目前已成为热塑性复合材料低成本快速成型工艺技术的代表。由于热塑性复合材料的成型是一个先熔化再凝固的物理变化过程,采用 AFP 技术,实现了对预浸料加热融化、自动铺放、原位固化的同步工艺过程实施,从而极大地提高了成型效率、降低了能耗,降低了复合材料的制造成本,AFP 成型过程如图 4所示。
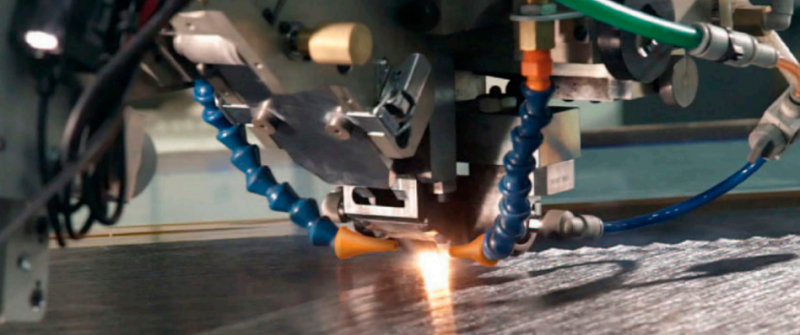
图4 自动铺放成型技术
对于大尺寸制件,采用 AFP 技术避免了固化时由于使用热压罐对于制件尺寸的限制,以及模具热膨胀系数不匹配的问题。此外,利用单向带短切纤维模压成型也为复合材料工程应用提供了另一种低成本高性能的思路,特别用以替代现有铝合金结构方案时优势明显,如图 5 所示,为 TenCate 眼镜蛇复合材料结构团队(CobraComposite Structures,CCS)采用热塑性团状模塑料(Bulk Molding Compound)通过模压工艺成型制件过程。
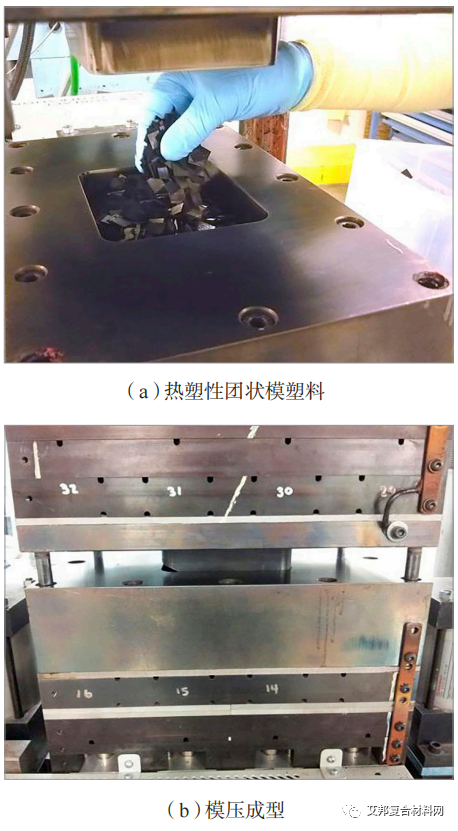
图5 TenCate公司热塑性团状模塑料模压工艺成型过程
国内高性能热塑性复合材料研究开始于“七五”计划期间,最早由吉林大学开展国产 PEEK 研制,“八五”至“十五”期间陆续与北京航空材料研究院合作开展了淤浆法、静电粉末法等预浸料制备及复合材料制造技术研究,完成了以某型固定翼运输机为型号背景的加筋口盖及加筋壁板类结构的制造工艺验证及装机验证考核。但后期受树脂稳定性、预浸料制造工艺等限制,国产高性能热塑性复合材料的应用研究几乎停滞不前。
近来,东华大学先进低维材料中心热塑性复合材料科研团队(原吉林大学团队),在近 20 年的 PEEK、PAEK 树脂合成及改性工作基础上,开展了连续纤维增强 PEEK 预浸料及其复合材料的研究工作。其中,所研制的树脂基体(LP–PEEK 和 CO–PEEK)与国外热塑性复合材料用专用树脂基体相比,玻璃化转变温度提高约10℃,但完全熔融温度降低约 40℃,即可在较低成型温度下,获得性能更优的热塑性复合材料,如表 2 所示。
表2 热塑性预浸料用PEEK性能对比
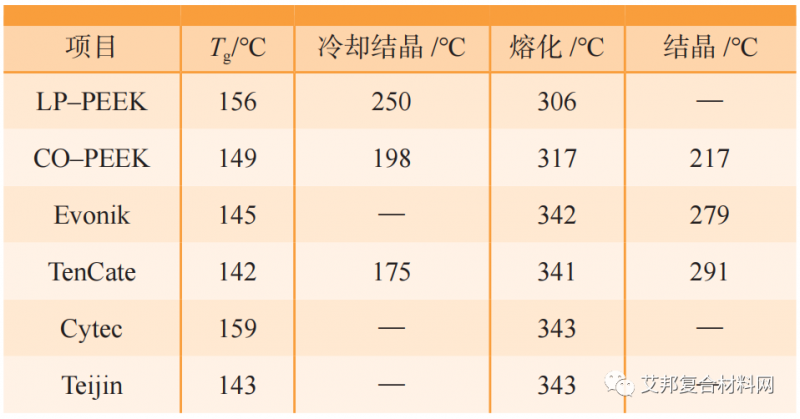
同时,采用东华大学先进低维材料中心热塑性复合材料科研团队(原吉林大学团队)自主研发的热熔预浸料设备,研制了连续碳纤维增强 PEEK 窄带预浸料(幅宽 100mm),如图 6 所示,并采用热压成型工艺制备了复合材料层合板,经超声波 A 扫描无损检测,结果显示层板内部质量完好,如图 7 所示。

图6 国内自主研发的热熔法连续碳纤维增强PEEK窄带预浸料
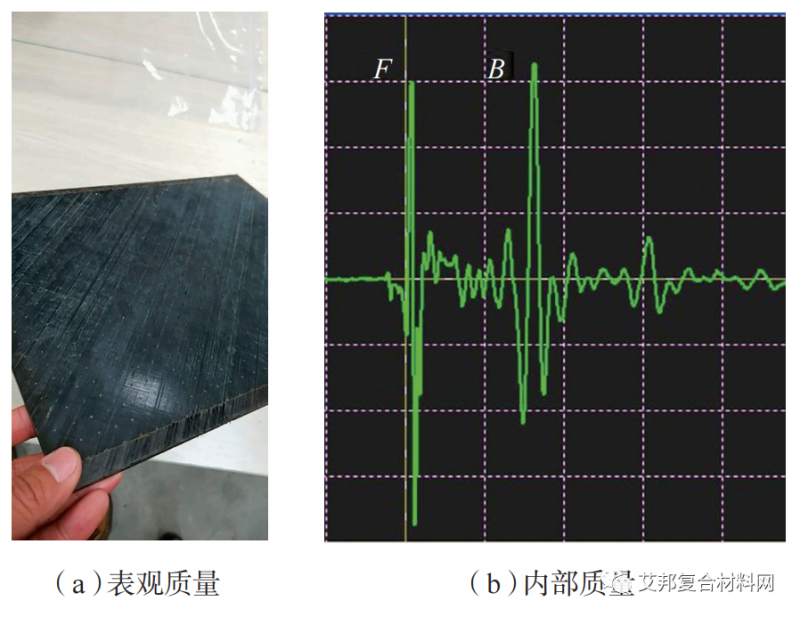
图7 国产预浸料模压工艺成型连续碳纤维增强PEEK复合材料层板
此外,针对热塑性复合材料自动化成型工艺,东华大学与南京航空航天大学合作开展了基于热塑性预浸料的自动铺丝工艺验证,结果表明预浸料树脂的低熔融温度特性,降低了成型工艺温度,基本满足了自动铺丝工艺性要求,如图 8 所示。
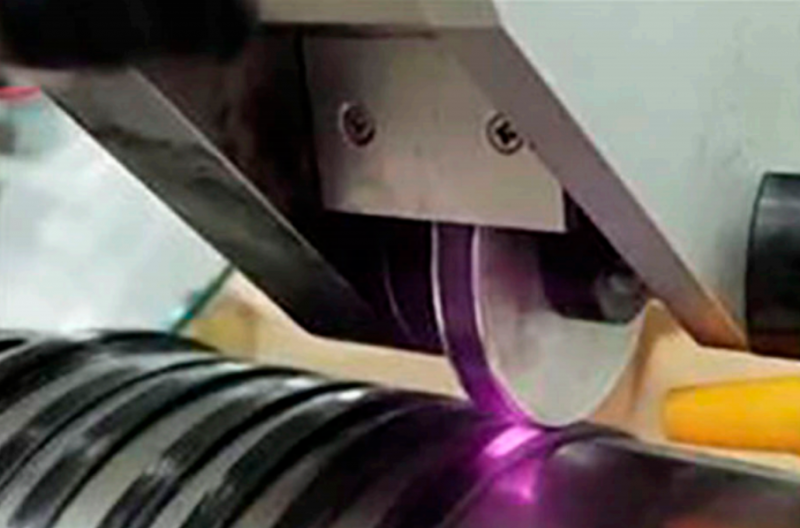
图8 国内热塑性预浸料自动铺丝工艺验证
2. 热塑性复合材料在航空发动机短舱上的应用
由于民机噪声指标已成为适航取证的强制性指标,为降低发动机噪声,在研究发动机降噪技术的同时,发动机短舱结构的降噪技术也在不断发展,消音衬垫技术是其中一种主要技术方案。该结构为具有消声功能性的复合材料蜂窝夹层结构,TenCate 公司开发的CF/PEI 热塑性复合材料层板,作为发动机短舱进气道降噪声衬蜂窝结构面板,已在空客 A380 飞机发动机上实现商业化应用,如图 9 所示。
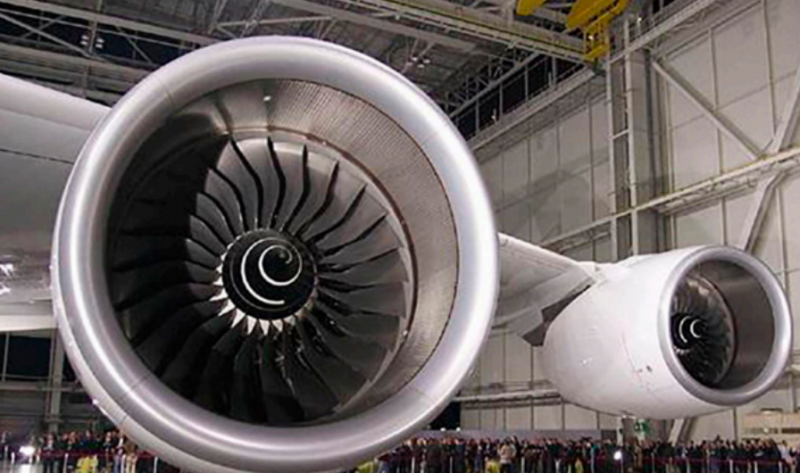
图9 空客A380飞机发动机短舱降噪声衬热塑性复合材料蜂窝结构
为保证飞机降落时迅速减速,缩短制动距离,减小制动器的磨损,发动机上均采用反推力装置。反推力装置开启时,使发动机外涵道气流流动方向发生大于 90° 的折转,从而在与正常推力相反的方向上产生推力分量,达到使飞机减速的目的。反推力装置所处的工作环境,对于材料的短时耐高温性能提出了较高的要求,以 PEEK、PEKK 为基体的高性能热塑性复合材料有望成为反推力装置选材的备选方案。风扇罩是位于发动机短舱中部的整流罩,与飞机结构类似,或成为短舱研制方开展热塑性复合材料应用的首选部件。
热塑性复合材料的另一个重点应用部位是发动机短舱吊挂,如图 10 所示。A340 飞机发动机短舱吊挂表面由 12 类、共 22 件蒙皮结构覆盖,均采用 CF/PPS 材料制造。结构长度 700——1400mm,宽度 200——400mm,厚度2.8mm,具有复杂双曲率外形,表面铺设有防雷击铜网表面,如图 11 所示。
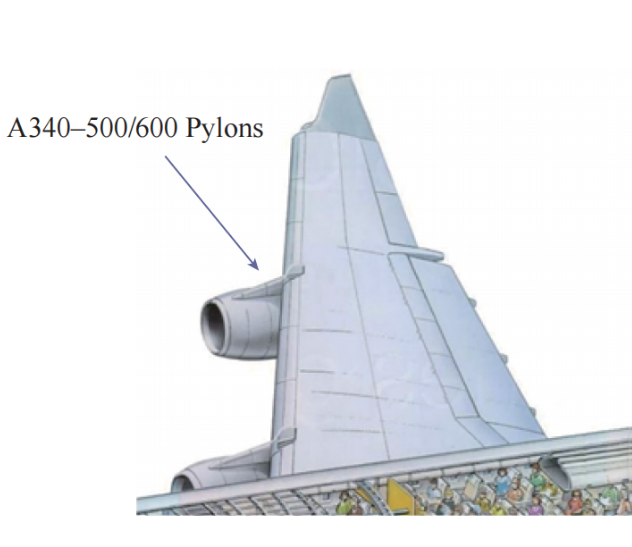
图10 空客A340飞机发动机短舱吊架
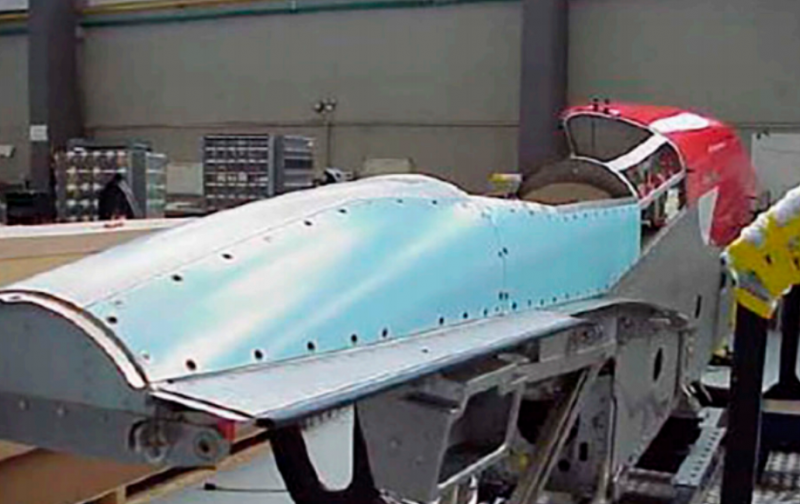
图11 空客A340飞机发动机短舱吊架蒙皮
由法国 Daher 公司承制的空客 A380 飞机发动机短舱吊架蒙皮如图 12 所示。该结构是 A380 飞机发动机上 50 块短舱吊架蒙皮之一,采用 TenCate Cetex TC1100 CF/PPS 材料制造。该材料除具有优异的韧性和耐腐蚀性之外,还具有自熄阻燃性,可采用冲压工艺成型,从而极大提高了成型效率。图 13 为位于法国图卢兹的空客总装厂在对 A380 飞机发动机吊架进行总装前的最后测试。
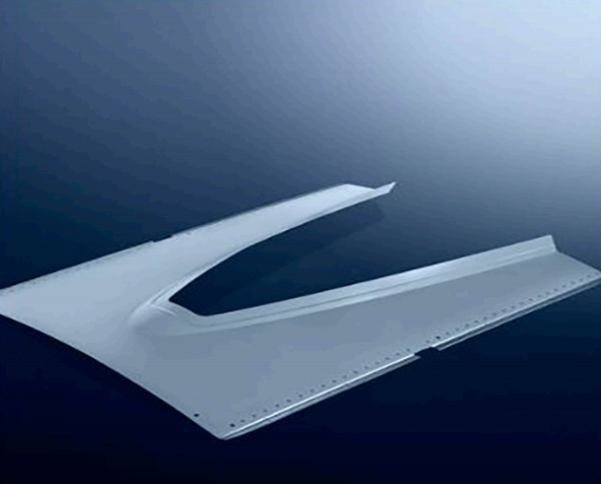
图12 空客A380飞机发动机短舱吊架蒙皮

图13 空客A380飞机发动机短舱吊架总装前测试
目前,荷兰针对热塑性复合材料的大型科研项目——“热塑性经济可承受性航空主结构”第 2 阶段项目(Thermoplastic Affffordable Primary Aircraft Structures 2, TAPAS 2)业已启动,目标是进一步提高主结构材料、制造工艺、设计概念和模具设备的技术成熟度。作为TAPAS 2 项目研究计划的一部分,荷兰国家航空航天实验室(NLR)开发了大尺寸、大厚度热塑性复合材料结构的自动铺放工艺技术。采用 TenCate Cetex TC1320CF/PEKK 单向预浸料,通过自动铺放工艺成型发动机短舱吊,如图 14 所示 。该结构长 6m,厚度 28mm,用以替代原有金属结构,显著降低了制造成本、结构重量,提高了燃油效率。
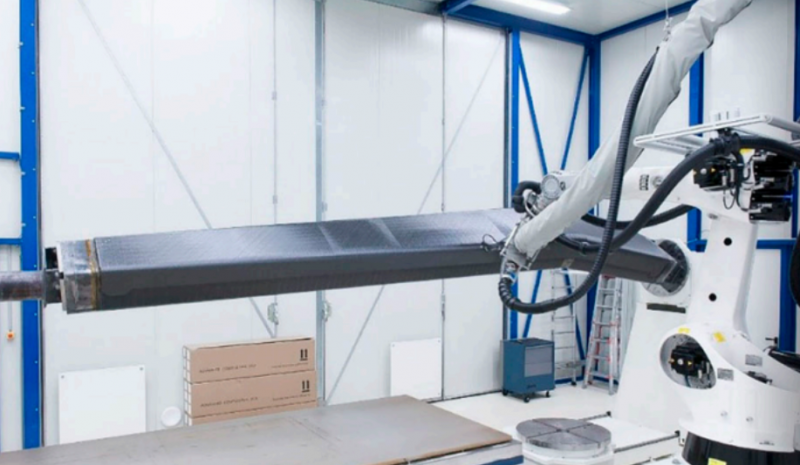
图14 采用自动铺放工艺成型的飞机发动机短舱吊架热塑性复合材料上部梁
3 结论
(1)经过几十年的积累,国外在热塑性复合材料领域积累起强大的技术优势。通过 PEEK、PPS 等高性能热塑性树脂的研发,结合先进的预浸料制备技术,形成了系列化的热塑性预浸料牌号。同时,随着自动铺放设备及工艺的发展,进一步克服了热塑性复合材料加工制造的困难,提高了成型效率,降低了制造成本,为热塑性复合材料在各航空领域取得成功应用奠定了基础。目前已在国外航空发动机短舱进气道降噪声衬、吊架蒙皮、梁等结构上取得成功应用。
(2)国内热塑性复合材料的研究尚处于起步阶段,目前相关研究应用情况与国外还存在较大差距,应进一步加大高性能热塑性树脂的研究力度,开发不同种类、不同耐温等级的新型热塑性树脂;加快预浸料的工程化应用研究,改善预浸料的浸渍质量,提高工艺性。国内航空发动机短舱研制单位应借鉴飞机方研制经验,结集国外、国内资源优势,积极开展热塑性复合材料在短舱典型结构上的验证工作,早日实现热塑性复合材料的工程化应用。